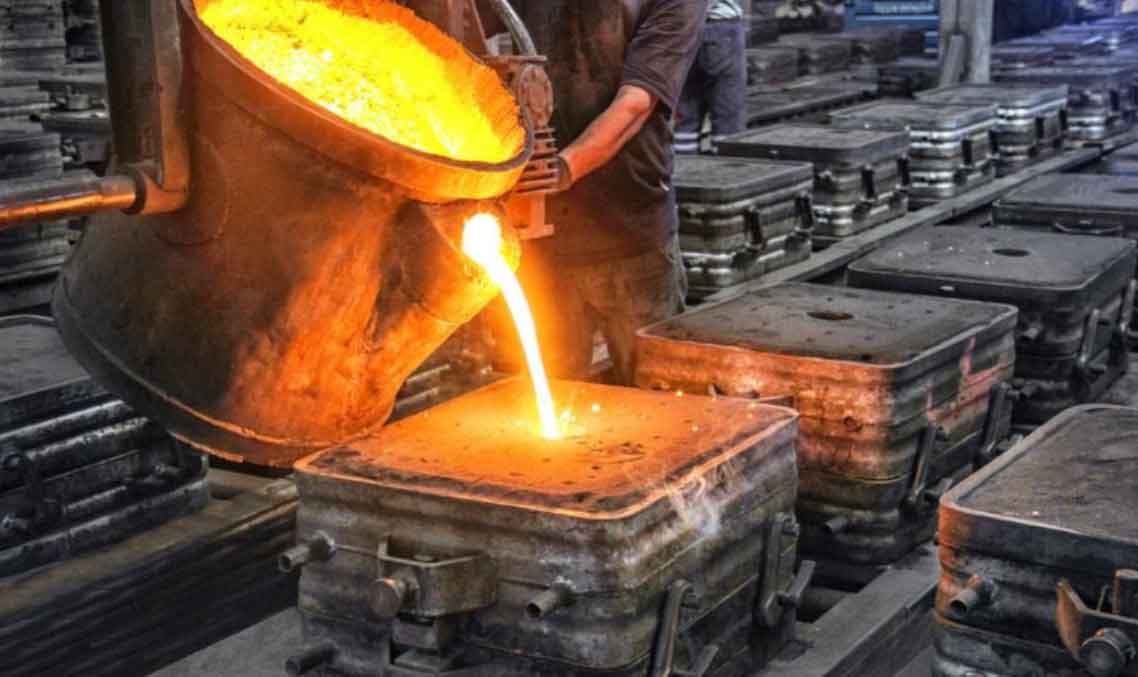
Experienced manufacturers consider several factors when selecting materials for sand casting. The choice of material significantly impacts the performance, durability, and cost-effectiveness of the final castings. Here are some insights from experienced manufacturers on material selection in sand casting:
1. Application Requirements:
Understanding the specific application requirements is crucial. Manufacturers consider factors such as mechanical properties (e.g., strength, hardness, ductility), corrosion resistance, thermal conductivity, and wear resistance to ensure the chosen material meets the demands of the intended use.
2. Material Compatibility with the Process:
The material must be compatible with the sand casting process. Some materials may require specific molding techniques, gating systems, and pouring temperatures to achieve optimal results.
3. Casting Complexity:
The complexity of the casting design plays a role in material selection. Certain materials may be more suitable for intricate or thin-walled components, while others may be preferred for large, heavy castings.
4. Cost-Effectiveness:
Manufacturers consider the material cost and availability to ensure the chosen material is cost-effective for the project’s budget and production volume.
5. Experience and Past Performance:
Leveraging past experience with specific materials and alloys helps manufacturers make informed decisions. They consider how well a material has performed in previous projects and whether it meets quality and performance standards.
6. Material Properties Tailoring:
Some materials can be modified through alloying or heat treatment to achieve desired properties. Experienced manufacturers assess the potential for tailoring material properties to suit specific needs.
7. Industry Standards and Regulations:
Manufacturers consider any industry standards, certifications, or regulatory requirements that dictate material choices for certain applications (e.g., aerospace, automotive, or medical industries).
8. Environmental and Sustainability Aspects:
Manufacturers increasingly focus on environmentally friendly practices. They may choose materials with lower environmental impact, such as recycled alloys or eco-friendly alternatives.
9. Supplier Reliability:
The reputation and reliability of material suppliers are important factors. Working with reputable suppliers ensures consistent material quality and availability.
10. Material Testing and Validation:
Manufacturers may conduct material testing and validation to verify that the selected material meets the required specifications and performance expectations.
11. Design Iterations:
If design iterations are expected, manufacturers choose materials that allow for flexibility in modifications without compromising performance.
12. Future Maintenance and Repairs:
For components requiring future maintenance or repairs, manufacturers consider materials that facilitate ease of repair or replacement.
Material selection in sand casting involves a comprehensive evaluation of multiple factors. Experienced manufacturers draw on their knowledge, past projects, and understanding of specific application requirements to make well-informed choices that lead to successful and reliable castings.