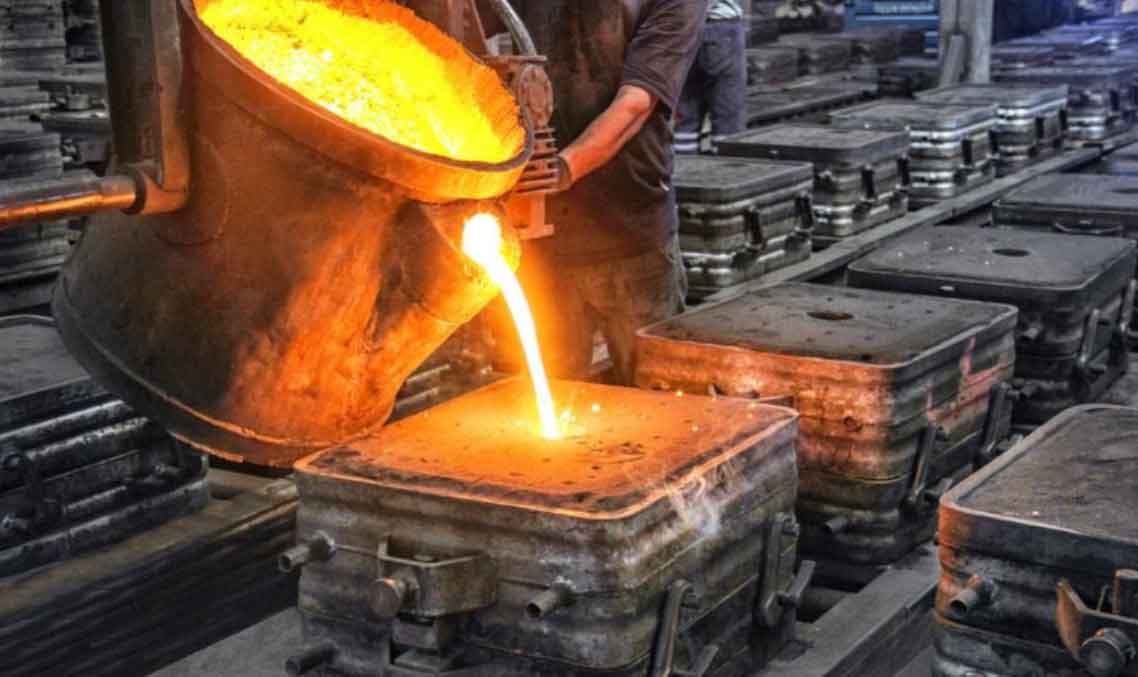
Sand casting technology has seen continuous innovations that enable manufacturers to stay ahead in the competitive manufacturing landscape. These innovations aim to improve casting quality, reduce lead times, enhance efficiency, and address environmental concerns. Here are some key innovations in sand casting technology that help manufacturers stay ahead:
1. Advanced Simulation and Modeling Tools:
- Manufacturers use sophisticated simulation software to analyze mold filling, solidification, and cooling processes. These tools help optimize casting designs, gating systems, and process parameters, leading to improved quality and reduced defects.
2. 3D Printing for Pattern Making:
- Additive manufacturing, specifically 3D printing, is integrated into sand casting to produce patterns and cores more efficiently. 3D-printed patterns allow for rapid prototyping, design iterations, and reduced lead times for tooling.
3. Digital Twins and Process Monitoring:
- Digital twin technology creates virtual replicas of the casting process, enabling real-time monitoring and analysis of process variables. This aids in predictive maintenance, optimization, and ensuring consistent quality.
4. Hybrid Casting Methods:
- Manufacturers combine sand casting with other casting methods (e.g., investment casting or lost foam casting) to leverage the benefits of both techniques. This approach allows for the production of complex components with improved accuracy and surface finish.
5. Green Sand Reclamation Systems:
- Green sand reclamation systems help recycle and reuse sand, reducing the need for fresh sand and minimizing waste generation. These systems contribute to cost savings and environmental sustainability.
6. High-Pressure Molding:
- High-pressure molding processes, such as high-pressure green sand molding and vacuum molding, offer improved mold compaction and casting density, resulting in higher quality and dimensional accuracy.
7. Robotics and Automation:
- Manufacturers are increasingly adopting robotic systems and automation in sand casting operations. Robots handle tasks such as mold handling, pouring, and post-casting finishing, leading to improved productivity and reduced labor costs.
8. Eco-Friendly Binder Systems:
- Alternative binder systems, such as organic binders or water-based binders, are being explored to replace traditional chemical binders. These eco-friendly options reduce emissions and improve the foundry’s environmental footprint.
9. Real-Time Quality Control and Inspection:
- Advancements in non-destructive testing (NDT) techniques, such as digital radiography and 3D scanning, allow for real-time quality control and inspection of castings, ensuring compliance with specifications and industry standards.
10. Material Innovations:
- Continuous research and development in metallurgy lead to new alloys and materials optimized for sand casting. These materials offer improved properties, such as enhanced strength, corrosion resistance, or high-temperature capabilities.
By embracing these innovations, manufacturers can streamline their processes, enhance casting quality, and respond quickly to customer demands. Staying ahead in the sand casting industry requires a commitment to adopting emerging technologies and a willingness to continuously improve casting methods and practices.