Ductile iron casting is a versatile manufacturing process that offers significant design flexibility, allowing engineers and designers to create complex and innovative components. This article explores how ductile iron casting enables maximum design flexibility and the benefits it brings to various industries.
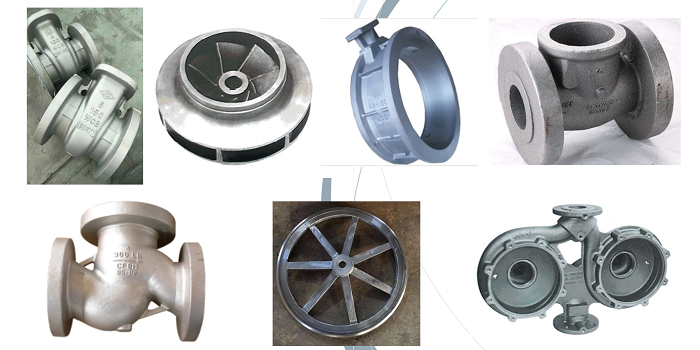
- Complex Geometries: Ductile iron casting allows for the production of components with intricate and complex geometries that may be challenging or cost-prohibitive to achieve using other manufacturing processes. The molten iron can flow into intricate mold cavities, enabling the creation of intricate shapes, thin-walled sections, and internal features. This capability is particularly advantageous in industries such as aerospace, automotive, and machinery, where intricate designs are often required.
- Consolidation of Parts: Ductile iron casting enables the consolidation of multiple components into a single cast part. By incorporating various features and functions into a single casting, the need for assembly and joining processes is minimized. This consolidation not only simplifies the manufacturing process but also reduces the number of parts, assembly time, and potential points of failure. It can lead to cost savings, improved efficiency, and enhanced overall component performance.
- Design Modifications and Iterations: Ductile iron casting offers design flexibility that allows for easy modifications and iterations during the product development phase. As the casting molds can be modified relatively quickly and cost-effectively, design changes can be implemented without significant delays or expenses. This flexibility allows designers to refine their designs, optimize performance, and address potential issues before finalizing the product.
- Integration of Complex Features: Ductile iron casting enables the integration of complex features directly into the casting process. This includes the incorporation of internal passageways, hollow sections, threads, flanges, and other intricate details. By integrating these features into the casting itself, the need for secondary machining, assembly, or welding operations can be minimized, resulting in cost and time savings while maintaining dimensional accuracy.
- Material Customization: Ductile iron casting offers the advantage of material customization to meet specific design requirements. Through the control of alloy composition and heat treatment processes, the mechanical properties of the castings can be tailored to meet desired specifications. This customization allows engineers to optimize the performance of components, such as achieving higher strength, improved wear resistance, or enhanced corrosion resistance, based on the application’s demands.
- Design for Weight Reduction: Ductile iron casting enables the design of lightweight components without compromising strength and durability. By utilizing advanced casting techniques, such as thin-walled casting and ribbing structures, weight reduction can be achieved while maintaining the necessary mechanical properties. This is particularly beneficial in industries where weight reduction is a critical factor, such as automotive and aerospace, as it contributes to fuel efficiency, increased payload, and improved overall performance.
- Cost-Effective Prototyping: Ductile iron casting provides a cost-effective method for producing prototypes and small production runs. The ability to quickly produce complex castings with minimal tooling investment allows for rapid iteration and testing of designs. This accelerates the product development cycle and reduces time to market, giving companies a competitive advantage.
In summary, ductile iron casting offers excellent design flexibility, enabling the creation of components with complex geometries, consolidation of parts, easy design modifications, integration of complex features, material customization, design for weight reduction, and cost-effective prototyping. These capabilities make ductile iron casting a preferred choice for industries that require innovative and optimized designs, ultimately leading to improved performance, reduced costs, and enhanced competitiveness.