In sand casting, the properties of the molding sand play a critical role in the final product’s quality, particularly in minimizing the occurrence of porosity. This article will explore how molding sand properties can influence porosity and strategies to optimize these properties for higher-quality sand castings.
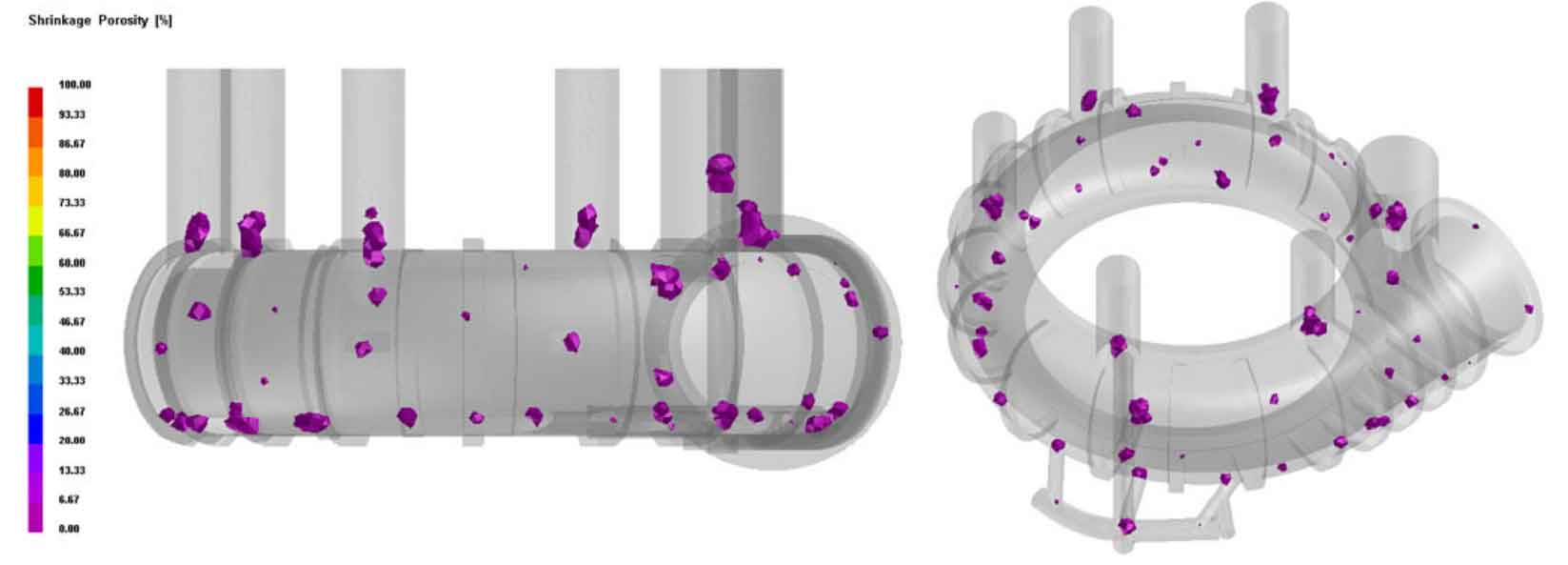
Permeability:
Permeability is the property of molding sand that allows gases to escape from the mold during the casting process. High permeability can prevent gas buildup within the mold, reducing the risk of gas-related porosity. Manufacturers can adjust the sand’s grain size, shape, and distribution to enhance permeability.
Moisture Content:
The moisture content in the molding sand impacts its ability to release gas. Excessive moisture can lead to steam generation when in contact with molten metal, potentially trapping the gas within the casting and creating porosity. Therefore, it is crucial to regulate the moisture content to an optimal level for the casting process.
Binder Content and Type:
Binders are used in the sand to help it retain its shape. However, they can also generate gas when heated. The type and amount of binder used in the molding sand can influence the amount of gas produced, potentially leading to porosity. Manufacturers need to carefully select and control binder content and type to minimize gas generation.
Grain Fineness and Shape:
The fineness and shape of the sand grains can affect the molding sand’s compactability and permeability, both of which can impact porosity. Coarser and more angular grains generally improve permeability, allowing gases to escape more readily.
Additives:
Certain additives can be used in the molding sand to help control gas generation and absorption, further reducing the risk of porosity. For instance, some additives can help to absorb excess moisture or binders, preventing gas formation.
By understanding the role of molding sand properties in porosity formation, manufacturers can make informed decisions to optimize these properties, reducing porosity, and improving the quality of their sand castings. This might involve adjusting the grain size, controlling moisture and binder content, or using appropriate additives. It’s a crucial aspect of process control in sand casting, demonstrating the interplay between material properties and casting quality.