Furan sand casting is a popular foundry process used for producing complex metal parts. To maximize productivity and achieve high-quality castings, there are several techniques and best practices you can follow. Here are some key considerations:
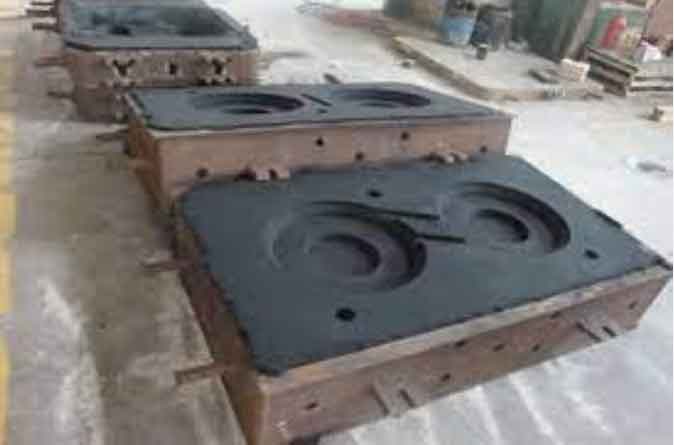
- Pattern Design: Optimize the pattern design for efficient casting. Consider draft angles, parting lines, and core placement to facilitate easy removal of the pattern and minimize the likelihood of defects.
- Sand Preparation: Properly prepare the furan sand mixture to ensure uniform and consistent mold quality. Follow the manufacturer’s instructions for sand-to-resin ratio and mixing time. Use high-quality sand with suitable grain size distribution.
- Tooling Maintenance: Regularly maintain and repair your tooling to ensure accurate and repeatable casting. Inspect and repair any damage or wear to the pattern, core boxes, and gating systems.
- Venting: Proper venting is crucial for the escape of gases during casting. Adequate venting helps prevent defects like gas porosity. Ensure the vents are properly placed in the mold and have the appropriate size and spacing.
- Molding Techniques: Employ effective molding techniques to maximize productivity. Use suitable molding equipment such as jolt-squeeze machines or automatic molding lines. Ensure consistent compaction pressure and proper alignment to achieve uniform mold density.
- Sand Conditioning: Regularly monitor and adjust the sand properties throughout the casting process. Maintain the optimal moisture content and temperature of the sand to prevent defects like sand fusion or excessive moisture-related issues.
- Pouring and Gating: Optimize the pouring and gating system design for efficient metal flow and minimal turbulence. Consider factors like metal temperature, pouring rate, and gating size. Use proper risers and sprues to promote directional solidification.
- Quality Control: Implement a robust quality control process to detect and address any issues promptly. Perform inspections of castings for defects such as shrinkage, sand inclusions, or dimensional inaccuracies. Conduct metallurgical analysis and mechanical testing as required.
- Process Monitoring: Regularly monitor the process parameters such as sand properties, compaction pressure, and pouring temperature to ensure consistency and make necessary adjustments if needed. Use data logging and analysis tools to identify trends and optimize the process.
- Training and Skill Development: Invest in training and skill development programs for your workforce. Ensure that operators and technicians have a comprehensive understanding of the furan sand casting process and its nuances. Continuous improvement and knowledge sharing will help enhance productivity.
Specific techniques and best practices may vary depending on your unique requirements, the complexity of the castings, and the equipment available. It’s essential to collaborate with experienced foundry professionals and consult industry resources for further guidance.