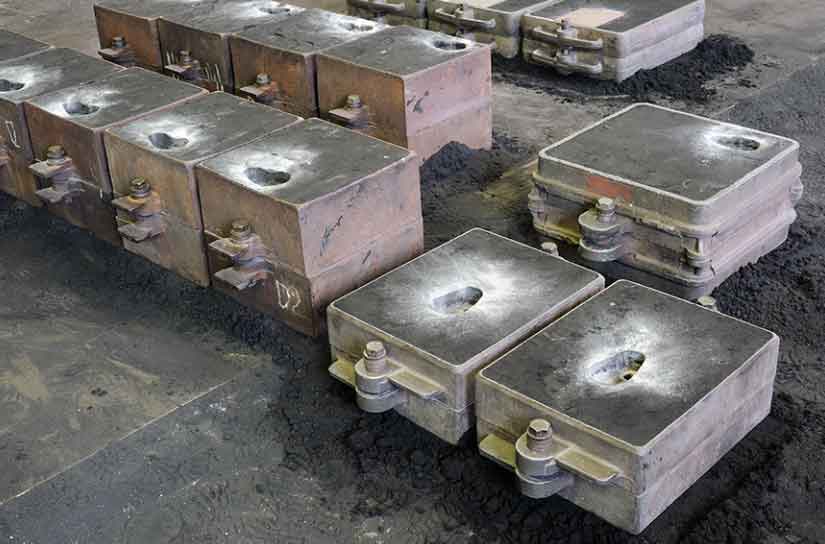
Resin sand casting technology has seen significant innovation and advancements in recent years. These developments have aimed to improve various aspects of the process, including mold preparation, material selection, casting techniques, and overall efficiency. Let’s explore some of the notable innovations in resin sand casting technology.
1. Mold Design and Simulation Software:
The advent of advanced computer-aided design (CAD) and computer-aided engineering (CAE) software has revolutionized mold design and simulation in resin sand casting. These software tools enable engineers and designers to create intricate mold designs, simulate the casting process, and analyze potential defects or issues before production. Mold design and simulation software optimize the mold geometry, gating system, and risering to enhance casting quality and reduce the likelihood of defects, thus saving time and costs.
2. 3D Printing for Pattern Production:
Additive manufacturing, specifically 3D printing, has emerged as a valuable tool in resin sand casting. 3D printing allows for the rapid production of highly complex patterns directly from digital designs. This eliminates the need for traditional pattern-making techniques, reduces lead times, and offers greater design flexibility. 3D-printed patterns also enable the production of intricate internal features and customized designs that were previously challenging to achieve using conventional methods.
3. Advanced Resin Formulations:
Resin technology has evolved, leading to the development of advanced resin formulations specifically designed for resin sand casting. These formulations offer improved flowability, reduced gas generation, enhanced collapsibility, and lower emissions during the curing process. The use of advanced resins improves mold quality, reduces defects, and ensures better surface finish on the cast parts. Furthermore, there has been a focus on developing environmentally friendly and sustainable resin options that minimize environmental impact.
4. Automation and Robotics:
Automation and robotics have found their way into resin sand casting processes, enhancing productivity, efficiency, and precision. Robotic systems can be employed for tasks such as mold assembly, sand mixing, mold handling, and pouring of molten metal. This reduces manual labor requirements, increases repeatability, and improves overall process control. Automation and robotics also enhance worker safety by handling heavy and hazardous tasks.
5. Real-Time Monitoring and Quality Control:
Advancements in sensor technology and data analytics have enabled real-time monitoring and quality control in resin sand casting. Sensors can be integrated into the process to measure parameters such as temperature, pressure, and flow rate, providing valuable feedback and ensuring optimal process conditions. Data analytics and machine learning algorithms can analyze the sensor data to detect anomalies, predict potential defects, and optimize process parameters, resulting in higher quality castings.
6. Hybrid Casting Techniques:
Incorporating resin sand casting with other casting techniques has led to the development of hybrid casting processes. For instance, resin sand casting can be combined with investment casting or lost foam casting methods to produce intricate parts with superior surface finish and dimensional accuracy. These hybrid approaches leverage the strengths of multiple casting processes, expanding the possibilities for complex component manufacturing.
These innovations and advancements in resin sand casting technology have elevated the process to new heights, improving quality, efficiency, and design capabilities. As research and development continue, it is expected that further innovations will emerge, addressing challenges and pushing the boundaries of what is achievable in resin sand casting.