Chapter 1: The History and Traditions of Metal Casting China
Metal casting has a rich and ancient history in China, with a legacy of traditional techniques and cultural significance. The art of metal casting in China dates back thousands of years and has played a significant role in shaping the country’s cultural heritage, technological advancements, and artistic expressions.
Ancient Casting Techniques:
- China has a long history of metal casting, with evidence of bronze casting dating back to the Shang Dynasty (16th to 11th centuries BCE). Bronze vessels, bells, weapons, and ritual objects were cast using sophisticated lost-wax casting techniques.
- During the Tang Dynasty (618-907 CE), intricate and elaborate bronze sculptures, such as those of Buddha figures, were created using advanced casting methods.
Cultural Inheritance:
- Metal casting was closely intertwined with Chinese culture and religion. Bronze ritual vessels held spiritual significance, and the casting process itself was considered a form of artistry.
- The Ming and Qing Dynasties (14th to 20th centuries CE) saw the continuation of metal casting traditions, producing ornate sculptures, decorative pieces, and cultural artifacts.
Influence on Art and Architecture:
- Metal casting techniques influenced architectural design, with cast-bronze elements being used to create elaborate doors, gates, and decorative components in temples and palaces.
- Traditional opera masks and figurines were also created using metal casting techniques, contributing to the country’s performing arts heritage.
Innovation and Technological Advances:
- China’s mastery of metal casting techniques allowed for the production of intricate and durable tools, weapons, and utensils that contributed to agricultural and technological advancements.
- The use of metal coins for trade and commerce further demonstrated the influence of metal casting on economic development.
Cultural Revival and Preservation:
- In modern times, efforts have been made to preserve and revive traditional metal casting techniques and skills. Artisans and craftsmen work to pass down these techniques to future generations, keeping the cultural heritage alive.
Contemporary Metal Casting Industry:
- Today, China has a vibrant and diverse metal casting industry that spans various sectors, including automotive, aerospace, construction, and art.
- China’s extensive manufacturing capabilities have made it a global leader in metal casting production, contributing to its position as a major player in the global economy.
The history and traditions of metal casting in China reflect the country’s cultural depth, technological ingenuity, and artistic prowess. While modern manufacturing methods have evolved, the legacy of ancient metal casting techniques continues to inspire and influence the country’s artistic, cultural, and industrial landscape.
Chapter 2: China Metal Casting Industry
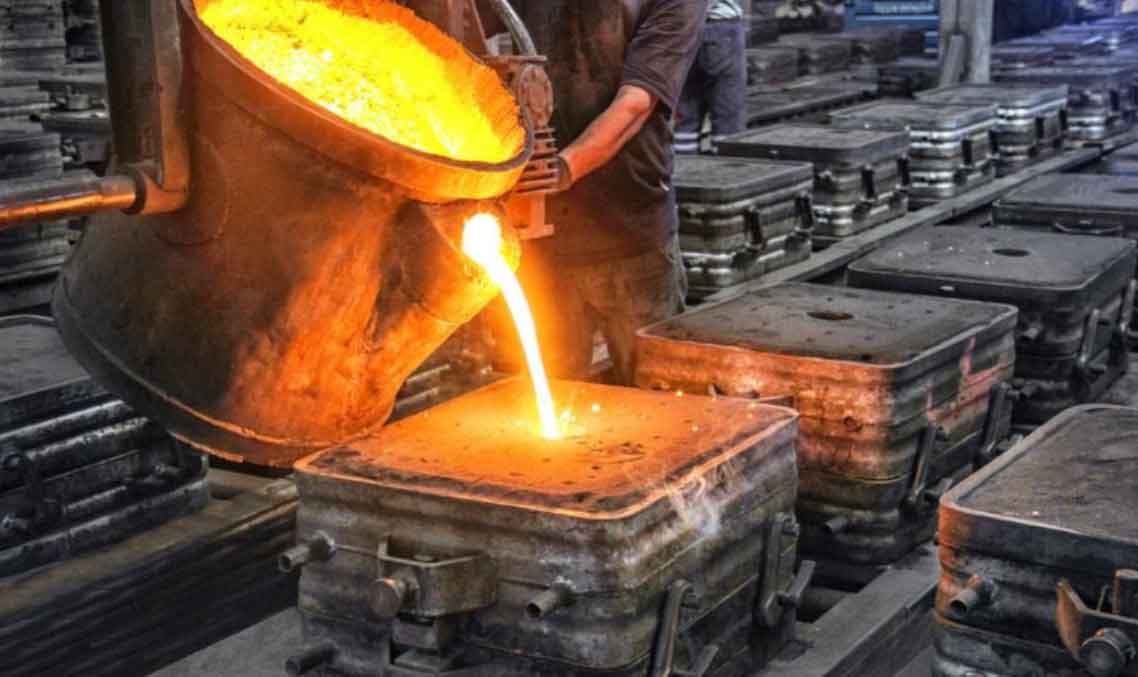
As of my last knowledge update in September 2021, China is one of the world’s largest producers of metal castings, with a well-established and extensive metal casting industry. The industry’s scale, output value, and geographical distribution vary across different regions of the country. Please note that the specific numbers and data may have changed since then. Here’s a general overview of the industry:
Scale and Output:
- China’s metal casting industry covers a wide range of sectors, including automotive, machinery, construction, aerospace, and more.
- The industry produces a diverse array of metal castings, including iron, steel, aluminum, and other alloys, for various applications.
Output Value:
- The metal casting industry contributes significantly to China’s industrial output and GDP.
- The exact output value can vary from year to year and across regions based on market demand and economic conditions.
Geographical Distribution:
- The metal casting industry is distributed across various provinces and regions in China. Some of the key casting production clusters include:
- Hebei Province: Known for its iron and steel casting production.
- Shandong Province: Has a strong presence in foundry and casting activities, producing a wide range of castings.
- Zhejiang Province: Known for its precision casting and investment casting capabilities.
- Jiangsu Province: Home to a significant number of foundries and metal casting facilities.
- Henan Province: Known for its ductile iron and gray iron casting production.
Emerging Areas:
- With China’s rapid industrialization and economic growth, metal casting capabilities have expanded to various regions, including some central and western provinces.
Government Policies and Environmental Concerns:
- In recent years, China has been focusing on improving the environmental performance of its industrial sectors, including metal casting, by implementing stricter regulations and encouraging cleaner production practices.
Please note that the specific data and trends may have evolved since my last update. For the most up-to-date information on the scale, output, and geographical distribution of the metal casting industry in China, I recommend referring to official government sources, industry reports, and statistical data from reputable organizations.
Chapter 3: Commonly Used Materials in Metal Casting China
In the metal casting industry in China, a variety of materials are commonly used to produce castings for different applications. Each material has its own unique characteristics, advantages, and suitable application fields. Here are some commonly used materials in metal casting in China, along with their application fields and characteristics:
1. Gray Cast Iron:
- Application Fields: Automotive components (engine blocks, brake drums), machinery parts, pipes, and construction materials.
- Characteristics: Good machinability, excellent wear resistance, and damping properties. Notable for its gray color due to the presence of graphite flakes.
2. Ductile (Nodular) Cast Iron:
- Application Fields: Automotive components (crankshafts, gears), heavy machinery, construction equipment, and pipelines.
- Characteristics: High tensile strength, excellent impact resistance, good wear resistance, and improved ductility compared to gray iron.
3. Carbon Steel:
- Application Fields: Machinery parts, tools, structural components, and some automotive components.
- Characteristics: Versatile material with a range of mechanical properties depending on carbon content. Can be heat-treated for increased strength.
4. Alloy Steel:
- Application Fields: Automotive parts, machinery components, aerospace components, and specialized industrial equipment.
- Characteristics: Enhanced mechanical properties through alloying elements (e.g., chromium, nickel, molybdenum) for improved strength, wear resistance, and corrosion resistance.
5. Stainless Steel:
- Application Fields: Food processing equipment, medical instruments, architectural components, and marine applications.
- Characteristics: Corrosion-resistant, high-temperature resistance, and aesthetic appeal. Available in various grades with different properties.
6. Aluminum Alloys:
- Application Fields: Automotive parts (engine blocks, wheels), aerospace components, consumer goods, and machinery parts.
- Characteristics: Lightweight, corrosion-resistant, good thermal and electrical conductivity, and suitable for intricate shapes.
7. Copper Alloys:
- Application Fields: Electrical components, plumbing fittings, marine applications, and decorative items.
- Characteristics: Excellent electrical and thermal conductivity, corrosion resistance, and good machinability.
8. Brass and Bronze Alloys:
- Application Fields: Bearings, gears, valves, architectural elements, and artistic sculptures.
- Characteristics: Malleable, corrosion-resistant, and offer various colors and finishes. Bronze is known for its high strength.
9. Magnesium Alloys:
- Application Fields: Aerospace and automotive components, lightweight structures, and electronic devices.
- Characteristics: Extremely lightweight, excellent strength-to-weight ratio, and good heat dissipation.
10. Zinc Alloys: – Application Fields: Die-casting applications, decorative items, and automotive components. – Characteristics: Low melting point, excellent fluidity, and good dimensional stability.
Each material has specific properties that make it suitable for certain applications. Manufacturers in China select the appropriate material based on factors such as mechanical requirements, corrosion resistance, cost, and ease of casting. It’s important to note that the choice of material impacts the casting process, as different materials may require specific techniques and considerations during casting and post-processing.
Chapter 4: Different Processes and Technologies of Metal Casting China
Metal casting China involves a range of processes and technologies to produce a variety of castings for different applications. Each casting process has its own characteristics, advantages, and limitations. Here are some of the commonly used casting processes in China, along with corresponding innovations and developments:
1. Sand Casting:
- Process: Involves creating a mold from sand and a binder, then pouring molten metal into the mold cavity.
- Application: Used for both small and large castings, especially in automotive, machinery, and construction industries.
- Innovations: Advancements in molding materials, binder systems, and automation for improved quality and efficiency. Introduction of resin-coated sand for enhanced mold stability and surface finish.
2. Investment Casting (Lost Wax Casting):
- Process: Involves creating a wax or plastic pattern, coating it with a ceramic shell, melting out the pattern, and pouring molten metal into the shell.
- Application: Suitable for complex and intricate parts in aerospace, automotive, and medical industries.
- Innovations: Use of advanced materials for ceramic shell coatings, implementation of 3D printing for pattern production, and improved precision through digital modeling and simulation.
3. Die Casting:
- Process: Molten metal is injected into a steel mold under high pressure to create intricate shapes with excellent surface finish.
- Application: Widely used in automotive, electronics, and consumer goods industries for high-volume production.
- Innovations: Development of advanced die materials for improved mold life and wear resistance, use of vacuum-assisted die casting for reduced porosity, and integration of real-time monitoring and control systems.
4. Centrifugal Casting:
- Process: Molten metal is poured into a rotating mold, creating cylindrical parts with controlled grain structure.
- Application: Used for pipes, tubes, and cylindrical components in various industries.
- Innovations: Enhanced mold design, use of electromagnetic fields for improved directional solidification, and incorporation of automation for better process control.
5. Continuous Casting:
- Process: Molten metal is continuously poured into a mold to produce long, semi-finished products like billets, slabs, and rods.
- Application: Primarily in steel and aluminum industries for efficient production of metal stock.
- Innovations: Advanced mold materials and coatings, electromagnetic stirring for improved quality, and integration of sensors for real-time monitoring.
6. Vacuum Casting:
- Process: Utilizes a vacuum to assist in drawing molten metal into the mold cavity, reducing porosity and improving casting quality.
- Application: Used for critical components requiring high integrity and minimal defects.
- Innovations: Optimization of vacuum parameters, use of gating systems to control metal flow, and integration with simulation software for process prediction.
7. Hybrid Technologies:
- Combination of traditional casting processes with additive manufacturing (3D printing) to create intricate patterns, molds, and cores.
These casting processes continue to evolve in China and around the world through advancements in materials, equipment, automation, and digital technologies. Innovation is driven by the need for higher efficiency, improved quality, reduced waste, and the ability to produce more complex and customized components.
Chapter 5: Technological Innovation and Research and Development in the Field of Metal Casting China
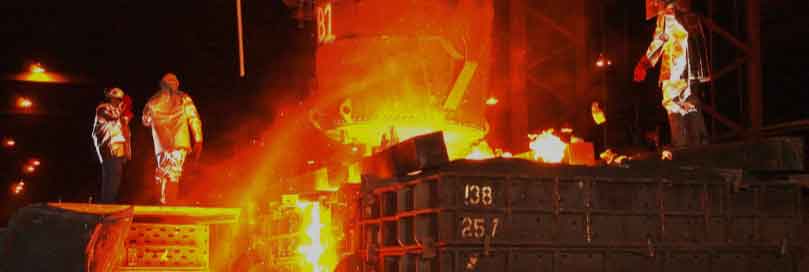
The field of metal casting China is experiencing significant technological innovation and research and development (R&D) activities. As the manufacturing industry evolves and global demands change, metal casting processes are continuously being enhanced to improve efficiency, quality, and sustainability. Some key areas of innovation and R&D in the metal casting industry in China include:
1. Advanced Materials:
- Development of new alloys and composite materials with improved mechanical properties, corrosion resistance, and high-temperature performance.
- Exploration of lightweight materials, such as magnesium and titanium alloys, to reduce the weight of cast components.
2. Digital Manufacturing and Simulation:
- Adoption of computer-aided design (CAD) and computer-aided engineering (CAE) software for virtual casting simulations, optimizing mold design, and predicting casting defects.
- Use of 3D printing (additive manufacturing) to create intricate patterns, molds, and cores, reducing lead times and enabling complex geometries.
3. Automation and Robotics:
- Integration of robotics and automation in casting processes for improved consistency, precision, and reduced labor-intensive tasks.
- Implementation of real-time monitoring systems to track process parameters and ensure product quality.
4. Green Casting Technologies:
- Development of eco-friendly casting methods with reduced emissions, energy consumption, and waste generation.
- Investigation of sustainable materials and practices to minimize environmental impact.
5. Precision Casting Techniques:
- Advancements in precision casting methods, such as investment casting, for higher accuracy and intricate detailing.
- Use of advanced molds and core materials for improved surface finish and dimensional accuracy.
6. Surface Treatment and Coatings:
- Research into advanced surface treatment techniques to enhance corrosion resistance, wear resistance, and aesthetics of cast components.
- Development of environmentally friendly coating materials and application processes.
7. Integration of AI and Big Data:
- Application of artificial intelligence (AI) and big data analytics to optimize casting processes, predict defects, and improve process control.
- Utilization of data-driven insights to enhance production efficiency and reduce downtime.
8. Quality Control and Testing:
- Implementation of non-destructive testing (NDT) methods, such as X-ray, ultrasound, and laser scanning, to ensure product quality and detect defects.
- Advancements in metallurgical analysis and metallography for better understanding of microstructures and material properties.
9. Industry Collaboration and Standardization:
- Collaboration between academia, research institutions, and industry to drive innovation and share knowledge.
- Development of industry standards and best practices to ensure consistent quality across the metal casting sector.
China’s metal casting industry is investing in these areas of innovation and R&D to stay competitive in the global market and meet the demands of various industries. These advancements not only improve the efficiency and quality of casting processes but also contribute to the overall advancement of manufacturing technology.
Chapter 6: Quality Control System and Related Standards of China Metal Casting Industry
The quality control system in the China metal casting industry is essential to ensure the production of high-quality castings that meet industry standards and customer requirements. The industry follows various quality control practices and standards to ensure product consistency, reliability, and safety. Some key aspects of the quality control system and related standards in the China metal casting industry include:
1. ISO Standards:
- The International Organization for Standardization (ISO) has established various standards related to quality management, process control, and product specifications.
- ISO 9001:2015 is a widely adopted standard for quality management systems, ensuring that the casting process is controlled, monitored, and continuously improved.
2. GB/T Standards:
- The Chinese National Standards (GB/T) cover various aspects of metal casting, including material specifications, testing methods, and product quality requirements.
- GB/T 9439-2010 outlines general technical conditions for casting materials, while GB/T 6414-2011 specifies methods for metallographic examination of cast iron.
3. Material Testing:
- Quality control includes material testing for chemical composition, mechanical properties, and microstructure to ensure that the casting material meets required specifications.
- Testing methods may include spectroscopy, tensile testing, hardness testing, and metallography.
4. Process Control:
- Strict process control measures are implemented during pattern making, mold preparation, melting, pouring, cooling, and other casting stages.
- Process parameters such as pouring temperature, mold temperature, and cooling rates are monitored and controlled to minimize defects.
5. Non-Destructive Testing (NDT):
- NDT techniques, such as X-ray, ultrasonic testing, and magnetic particle testing, are used to detect internal defects and ensure casting integrity.
- NDT helps identify cracks, porosity, inclusions, and other imperfections that may affect the quality of the casting.
6. Dimensional Inspection:
- Casting dimensions are measured and inspected to ensure compliance with specified tolerances and geometric requirements.
- Coordinate measuring machines (CMMs) and other precision measurement tools are used for accurate dimensional analysis.
7. Quality Assurance Documentation:
- Comprehensive documentation is maintained throughout the casting process, including material certificates, inspection records, process data, and quality reports.
8. Continuous Improvement:
- The industry emphasizes continuous improvement through data analysis, root cause analysis of defects, corrective actions, and preventive measures.
9. Supplier Audits:
- Manufacturers often conduct audits of their suppliers’ quality control processes to ensure that raw materials and components meet required standards.
China metal casting industry is committed to enhancing product quality and adhering to international standards to maintain customer satisfaction and competitiveness in the global market. Continuous improvement, rigorous testing, and adherence to established standards contribute to the overall quality control system in the industry.
Chapter 7: The Application of China Metal Casting Products
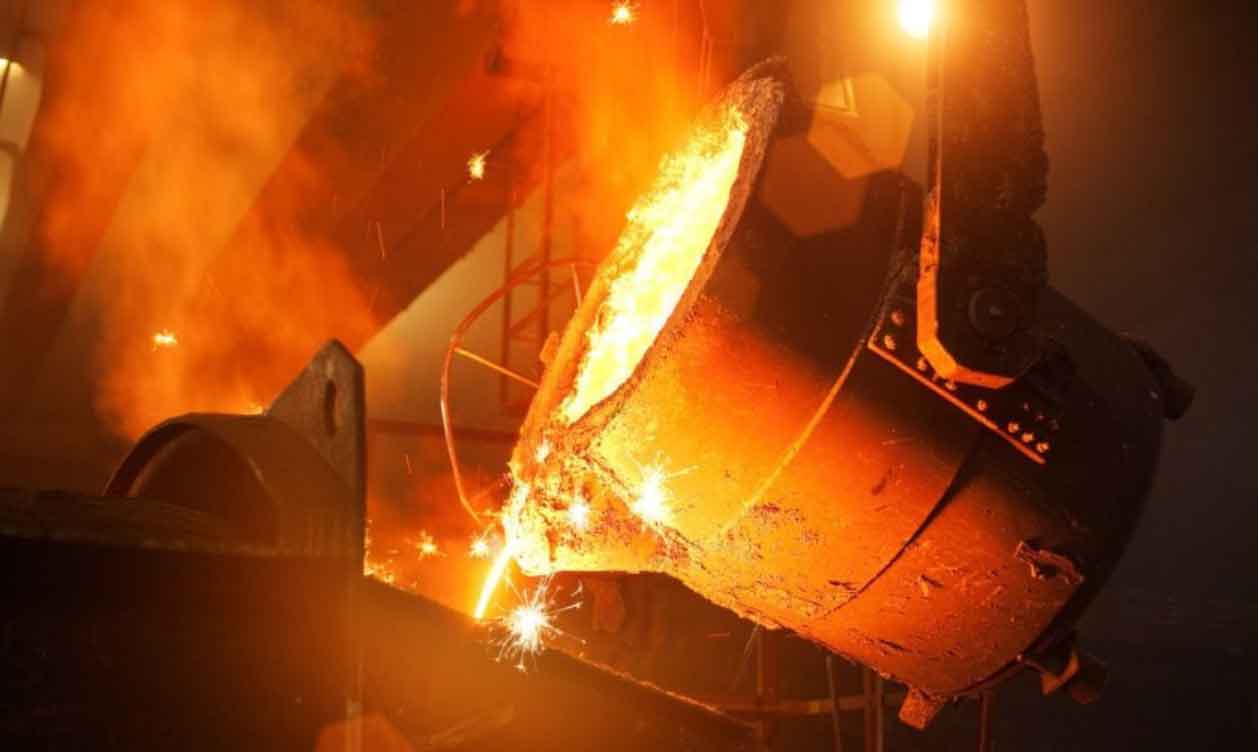
China metal casting products find widespread application in various fields, including:
- Automotive Manufacturing:
- Engine components: Cylinder heads, engine blocks, crankshafts, pistons, etc.
- Transmission parts: Gearboxes, transmission cases, differential housings, etc.
- Suspension and chassis components: Brake calipers, control arms, steering knuckles, etc.
- Exhaust system components: Exhaust manifolds, catalytic converters, etc.
- Mechanical Engineering:
- Industrial machinery: Cast parts for pumps, compressors, turbines, and other industrial equipment.
- Construction machinery: Castings for excavators, bulldozers, loaders, etc.
- Agricultural machinery: Components for tractors, harvesters, and other farm equipment.
- Aerospace and Defense:
- Aircraft components: Engine parts, landing gear components, structural parts.
- Spacecraft components: Rocket engine parts, launch vehicle components, satellite hardware.
- Defense applications: Castings for military vehicles, weapons systems, and equipment.
- Energy and Power Generation:
- Power plant equipment: Turbine blades, generators, heat exchangers, and other components.
- Renewable energy: Wind turbine components, solar power equipment, etc.
- Railway Industry:
- Train components: Brake discs, wheels, couplings, and other parts for railway systems.
- Oil and Gas Industry:
- Equipment for drilling rigs, pipelines, and refining processes.
- Marine and Shipbuilding:
- Marine engine components, propellers, ship fittings, and other marine equipment.
- Consumer Goods:
- Household appliances: Parts for ovens, stoves, washing machines, etc.
- Furniture: Cast metal components for decorative and functional purposes.
- Infrastructure and Construction:
- Manhole covers, streetlights, drainage systems, and other urban infrastructure components.
- Medical Equipment:
- Castings used in medical devices, imaging equipment, and prosthetics.
The versatility and adaptability of metal casting processes in China have allowed the industry to cater to a wide range of applications across various sectors, contributing significantly to the country’s manufacturing capabilities and economic growth.
Chapter 8: The Policies and Regulations Related to China Metal Casting Industry
The China metal casting industry is subject to various policies and regulations that encompass environmental protection, quality standards, safety, and industry development. These regulations are put in place to ensure sustainable growth, product quality, and compliance with environmental standards. Some key policies and regulations related to the China metal casting industry include:
1. Environmental Protection:
- “Law of the People’s Republic of China on the Prevention and Control of Environmental Pollution Caused by Solid Wastes” sets guidelines for the management, disposal, and treatment of waste generated during the casting process.
- “Environmental Impact Assessment Law” mandates that casting facilities undergo environmental impact assessments before construction or expansion.
2. Quality Standards:
- “GB/T” (Guo Biao Tiao) standards issued by the Chinese National Standards Authority cover various aspects of metal casting, including material specifications, testing methods, and product quality requirements.
3. Energy Efficiency and Emissions Reduction:
- “Energy Conservation Law” promotes energy-efficient practices in manufacturing, including metal casting.
- “Emission Standards for Air Pollutants” regulate emissions of pollutants, such as particulate matter and sulfur dioxide, from casting operations.
4. Occupational Health and Safety:
- “Occupational Disease Prevention and Control Law” mandates the protection of workers’ health and safety in casting facilities.
- “Safety Production Law” establishes safety requirements and measures to prevent accidents in metal casting operations.
5. Industry Development:
- China’s “Made in China 2025” initiative promotes the development of advanced manufacturing, including metal casting, through technological innovation and upgrading.
- “Guidelines for the Development of the Foundry Industry” provide strategic guidance for the growth and transformation of the casting industry.
6. Waste Management and Recycling:
- “Circular Economy Promotion Law” encourages the recycling and proper disposal of waste materials generated by casting processes.
- “Law of the People’s Republic of China on the Prevention and Control of Environmental Pollution by Solid Wastes” addresses waste management and recycling.
7. Industry Standardization:
- Industry associations and government bodies work to establish and update industry standards that cover various aspects of metal casting, including materials, processes, and quality.
It’s important to note that regulations and policies may evolve over time, and it’s advisable for businesses in the China metal casting industry to stay informed about the latest developments and comply with the applicable regulations. Adhering to these policies ensures sustainable growth, environmental protection, and the production of high-quality castings that meet both domestic and international standards.