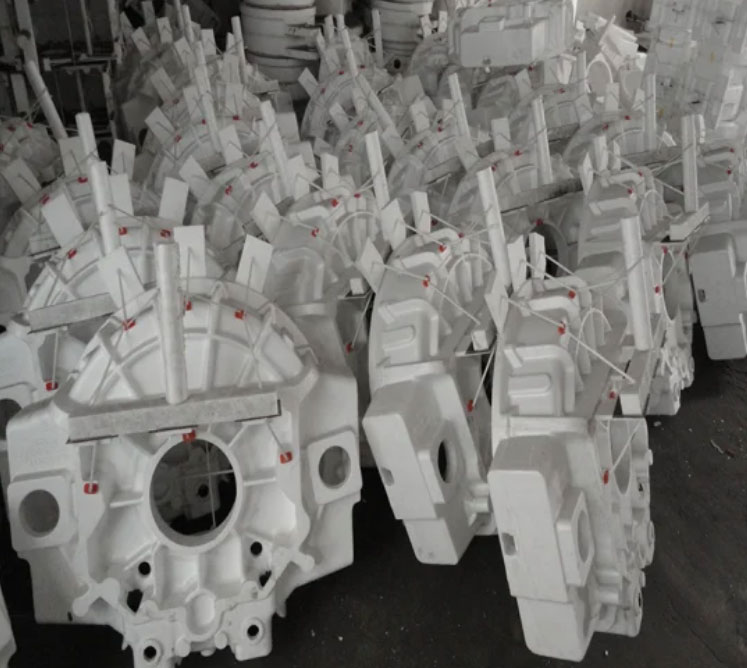
Lost foam casting has indeed revolutionized the metal casting industry since its introduction. This innovative casting method has gained popularity and acceptance across various industries due to its ability to produce intricate and near net shape castings with numerous advantages. Here are some key reasons why lost foam casting has risen to prominence in the metal casting industry:
1. Design Flexibility:
- Lost foam casting offers unparalleled design freedom, allowing engineers and designers to create complex and intricate components with ease. The foam patterns used in lost foam casting can be easily shaped and carved into almost any form, enabling the production of parts with intricate geometries.
2. Near Net Shape Castings:
- Lost foam casting produces near net shape castings, significantly reducing the need for post-casting machining or finishing. This minimizes material waste, machining costs, and overall lead times, making it a cost-effective and time-saving process.
3. Dimensional Accuracy and Consistency:
- Lost foam casting provides high dimensional accuracy and consistency, leading to precise and repeatable castings. This results in improved product quality and reduced scrap rates.
4. Complexity of Assemblies:
- Lost foam casting allows for the integration of multiple components into a single casting, reducing the need for separate parts and assembly processes. This simplifies the overall manufacturing process and enhances the structural integrity of the final product.
5. Smoother Surface Finish:
- Lost foam castings generally have smoother surface finishes, reducing the need for additional surface treatments or finishing operations.
6. Lightweight and Optimized Designs:
- Lost foam casting enables the creation of lightweight and optimized components, making it suitable for industries where weight reduction is crucial, such as aerospace and automotive.
7. Reduction in Tooling Costs:
- Lost foam casting requires relatively simple and cost-effective tools, contributing to cost savings, especially for small to medium production runs.
8. Sustainability and Waste Reduction:
- Lost foam casting promotes sustainability through reduced material waste, energy efficiency, and the ability to recycle or reuse foam patterns.
9. Rapid Prototyping and Iteration:
- The ease of creating foam patterns allows for rapid prototyping and iteration of designs, enabling faster development cycles and reduced time-to-market for new products.
10. Versatility of Materials:
- Lost foam casting can be used with a wide range of materials, making it suitable for diverse industrial applications.
These advantages have made lost foam casting a favored choice in various industries, including automotive, aerospace, industrial machinery, and art. It continues to be a transformative and sought-after technology in the metal casting industry, unlocking new design possibilities and driving efficiency and cost-effectiveness in manufacturing processes. As foundries continue to embrace and refine lost foam casting techniques, the method’s influence in the industry is expected to grow further in the future.