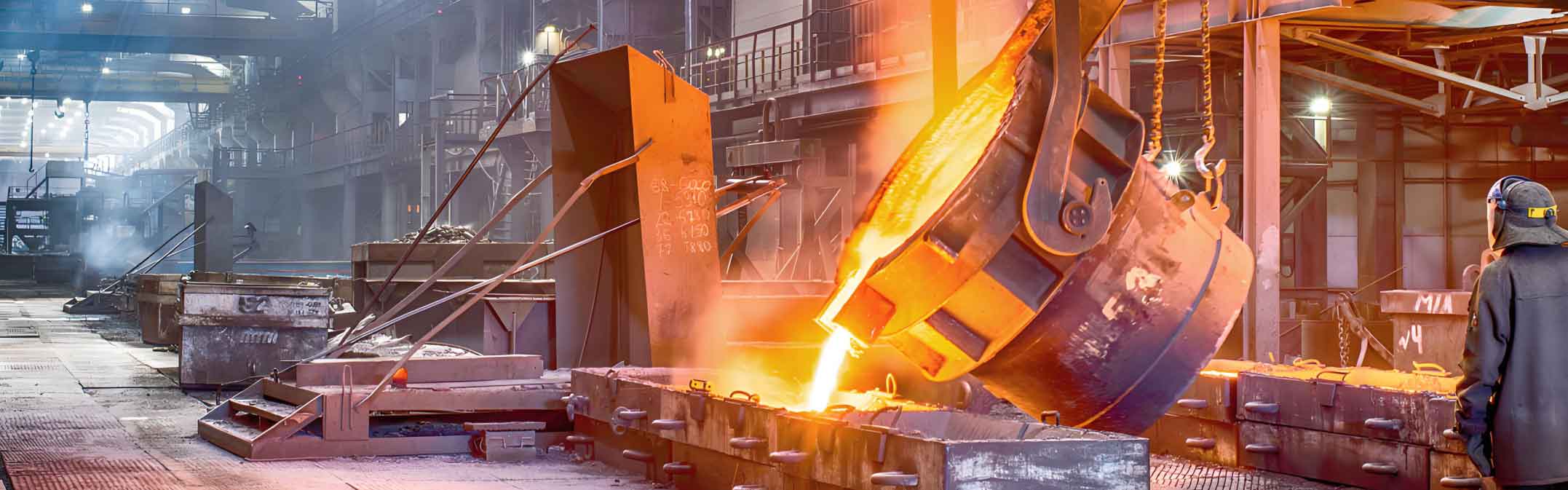
Sand casting is a versatile and widely used process for creating metal components with complex geometries. One of the critical aspects of sand casting is the design of the gating and risering systems. These systems control the flow of molten metal into the mold and ensure proper feeding during solidification, significantly impacting the quality, efficiency, and integrity of the final casting. Optimizing these systems is essential for minimizing defects, improving mechanical properties, and enhancing overall casting performance. This article explores the principles, strategies, and advancements in optimizing gating and risering systems in sand casting.
Introduction to Sand Casting
Sand casting involves creating a mold from a sand mixture and pouring molten metal into the cavity formed by a pattern. The gating system directs the flow of molten metal into the mold, while the risering system compensates for shrinkage during solidification. Proper design and optimization of these systems are crucial for achieving high-quality castings.
Importance of Gating and Risering Systems
- Control of Metal Flow: Ensures smooth and turbulence-free flow of molten metal into the mold.
- Defect Minimization: Reduces common casting defects such as porosity, inclusions, and misruns.
- Feeding and Solidification: Ensures adequate feeding of molten metal to compensate for shrinkage during solidification.
- Dimensional Accuracy: Maintains the dimensional accuracy and structural integrity of the casting.
Principles of Gating System Design
The gating system controls the flow of molten metal from the ladle to the mold cavity. An optimized gating system ensures a smooth and controlled flow, minimizing turbulence and preventing defects.
Components of a Gating System
- Pouring Basin: A reservoir that receives molten metal from the ladle and directs it into the sprue.
- Sprue: A vertical channel that carries molten metal from the pouring basin to the runner.
- Runner: A horizontal channel that distributes molten metal to the gates.
- Gates: Openings that allow molten metal to flow from the runner into the mold cavity.
Design Considerations
- Flow Rate: The gating system should ensure a consistent flow rate to prevent turbulence and gas entrapment.
- Pressure Balance: Proper design should maintain a balance between the metal pressure and the mold’s ability to withstand it.
- Thermal Control: The system should manage the temperature of the molten metal to ensure optimal fluidity and solidification.
Strategies for Optimizing Gating Systems
Use of Choke
A choke is a restriction in the gating system that controls the flow rate and pressure of molten metal.
- Purpose: Controls the speed and volume of molten metal entering the mold.
- Placement: Typically placed in the runner or gate to regulate flow.
Tapered Sprue Design
A tapered sprue helps maintain a consistent flow rate and reduces turbulence.
- Design: The sprue tapers from a wider top to a narrower bottom, ensuring smooth flow.
- Benefits: Reduces turbulence, prevents gas entrapment, and improves metal distribution.
Fillets and Radii
Incorporating fillets and radii at sharp corners and junctions reduces turbulence and stress concentrations.
- Design: Smooth transitions at corners and junctions.
- Benefits: Reduces turbulence, minimizes defects, and improves structural integrity.
Strategy | Purpose | Benefits |
---|---|---|
Use of Choke | Controls flow rate and pressure | Prevents turbulence and gas entrapment |
Tapered Sprue Design | Maintains consistent flow rate | Reduces turbulence, improves metal distribution |
Fillets and Radii | Smooth transitions at corners and junctions | Reduces turbulence, minimizes defects |
Principles of Risering System Design
The risering system compensates for the shrinkage that occurs as the molten metal solidifies. Proper riser design ensures that the casting remains defect-free and maintains its dimensional integrity.
Components of a Risering System
- Risers: Reservoirs of molten metal that feed the casting during solidification.
- Riser Necks: Narrow sections that connect the riser to the mold cavity, controlling the flow of molten metal.
Design Considerations
- Riser Placement: Strategic placement of risers to ensure even feeding and solidification.
- Riser Size: Adequate size to provide sufficient feed metal and compensate for shrinkage.
- Thermal Control: Managing the temperature differential between the riser and the casting to ensure proper feeding.
Strategies for Optimizing Risering Systems
Use of Insulating Sleeves
Insulating sleeves placed around risers reduce heat loss and extend the solidification time.
- Materials: Ceramic fiber, refractory coatings.
- Benefits: Maintains molten state longer, ensures adequate feeding, reduces shrinkage defects.
Hot Topping
Hot topping involves adding a thermally insulating material to the top of the riser to prevent premature solidification.
- Materials: Exothermic compounds, insulating powders.
- Benefits: Prolongs solidification, ensures complete feeding, minimizes shrinkage porosity.
Directional Solidification
Designing the mold and risering system to promote directional solidification ensures that the casting solidifies from the extremities towards the riser.
- Design: Placement of chills and risers to control solidification direction.
- Benefits: Ensures complete feeding, reduces shrinkage defects, improves structural integrity.
Strategy | Purpose | Benefits |
---|---|---|
Use of Insulating Sleeves | Reduces heat loss, extends solidification time | Ensures adequate feeding, reduces shrinkage defects |
Hot Topping | Prevents premature solidification | Prolongs solidification, minimizes shrinkage porosity |
Directional Solidification | Promotes solidification from extremities towards riser | Ensures complete feeding, improves structural integrity |
Advanced Technologies and Tools for Optimization
Recent advancements in technology have provided new tools and methods for optimizing gating and risering systems in sand casting, leading to improved accuracy and efficiency.
Computer-Aided Design (CAD) and Simulation
CAD and simulation software allow engineers to design and test gating and risering systems virtually, identifying potential issues before actual production.
- Flow Simulation: Analyzes the flow of molten metal to ensure smooth and controlled filling.
- Solidification Simulation: Predicts solidification patterns to optimize riser placement and size.
- Stress Analysis: Identifies potential stress points and optimizes design to reduce defects.
Tool | Function | Benefits |
---|---|---|
Flow Simulation | Analyzes molten metal flow | Ensures smooth and controlled filling |
Solidification Simulation | Predicts solidification patterns | Optimizes riser placement and size |
Stress Analysis | Identifies potential stress points | Reduces defects, improves structural integrity |
Real-Time Monitoring
Real-time monitoring systems use sensors and data acquisition tools to track the casting process, allowing for immediate adjustments to optimize gating and risering systems.
- Temperature Sensors: Monitor the temperature of molten metal and mold during casting.
- Pressure Sensors: Track the pressure within the gating system to ensure proper flow.
- Data Analysis: Provides real-time data for immediate adjustments and optimization.
Monitoring System | Function | Benefits |
---|---|---|
Temperature Sensors | Monitor temperature during casting | Ensures proper temperature control, reduces defects |
Pressure Sensors | Track pressure within gating system | Ensures proper flow, minimizes turbulence |
Data Analysis | Provides real-time data | Allows immediate adjustments, optimizes casting process |
Applications in Grey Cast Iron Casting
Optimizing gating and risering systems is particularly important in the casting of grey cast iron, where mechanical properties and defect minimization are critical.
Automotive Industry
- Engine Blocks: Ensures proper filling and feeding, reducing porosity and improving strength.
- Brake Discs: Enhances dimensional accuracy and surface finish, ensuring reliable performance.
Heavy Machinery
- Gear Housings: Improves structural integrity and reduces defects, enhancing performance and durability.
- Pump Housings: Ensures complete filling and feeding, minimizing defects and improving efficiency.
Aerospace Industry
- Turbine Components: Ensures high-quality castings with superior mechanical properties and minimal defects.
- Structural Parts: Enhances reliability and safety in critical aerospace applications.
Industry | Applications |
---|---|
Automotive | Engine blocks, brake discs |
Heavy Machinery | Gear housings, pump housings |
Aerospace | Turbine components, structural parts |
Conclusion
Optimizing gating and risering systems in sand casting is essential for producing high-quality grey cast iron components. By understanding the principles of these systems and employing advanced strategies and technologies, manufacturers can minimize defects, improve mechanical properties, and enhance the overall quality and efficiency of the casting process. Techniques such as the use of chokes, tapered sprue design, insulating sleeves, hot topping, and directional solidification, combined with tools like CAD, simulation, and real-time monitoring, provide comprehensive solutions for optimizing gating and risering systems. These advancements ensure that sand castings meet the stringent requirements of modern engineering and manufacturing, delivering reliable and high-performance components for various industries.
Optimization Strategy | Purpose | Benefits |
---|---|---|
Use of Choke | Controls flow rate and pressure | Prevents turbulence and gas entrapment |
Tapered Sprue Design | Maintains consistent flow rate | Reduces turbulence, improves metal distribution |
Fillets and Radii | Smooth transitions at corners and junctions | Reduces turbulence, minimizes defects |
Use of Insulating Sleeves | Reduces heat loss, extends solidification time | Ensures adequate feeding, reduces shrinkage defects |
Hot Topping | Prevents premature solidification | Prolongs solidification, minimizes shrinkage porosity |
Directional Solidification | Promotes solidification from extremities towards riser | Ensures complete feeding, improves structural integrity |
Flow Simulation | Analyzes molten metal flow | Ensures smooth and controlled filling |
Solidification Simulation | Predicts solidification patterns | Optimizes riser placement and size |
Stress Analysis | Identifies potential stress points | Reduces defects, improves structural integrity |
Temperature Sensors | Monitor temperature during casting | Ensures proper temperature control, reduces defects |
Pressure Sensors | Track pressure within gating system | Ensures proper flow, minimizes turbulence |
Data Analysis | Provides real-time data | Allows immediate adjustments, optimizes casting process |
By adopting these strategies, manufacturers can achieve superior sand castings, ensuring the reliability and performance of their products in demanding applications.