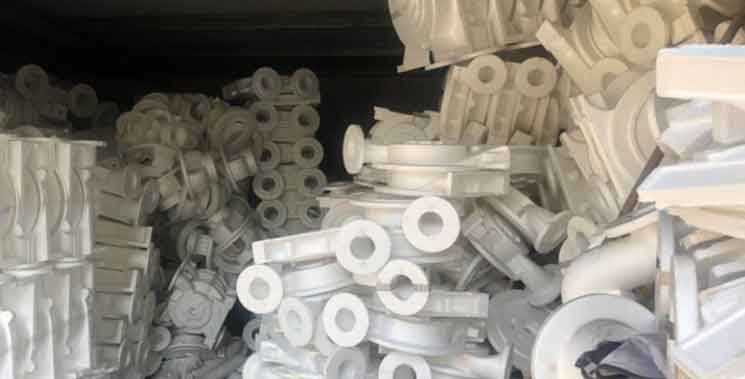
To optimize performance in lost foam casting, several techniques and best practices can be employed. By implementing these strategies, manufacturers can enhance the quality, dimensional accuracy, and efficiency of the casting process. Here are some key techniques and best practices for optimizing performance in lost foam casting:
1. Pattern Design and Engineering:
The design of the foam pattern plays a crucial role in the success of the lost foam casting process. It is essential to ensure that the pattern is robust, dimensionally accurate, and capable of withstanding the casting process without deformation. Employing proper engineering practices, such as selecting the appropriate foam density, wall thickness, and incorporating gating and risering systems, will contribute to a successful casting outcome.
2. Foam Pattern Coating:
Coating the foam pattern with a refractory material is essential to create a smooth and uniform surface on the mold cavity. This coating enhances the surface finish of the final casting and prevents the foam from degrading during the pouring of the molten metal. It is important to select an appropriate coating material and apply it uniformly to achieve consistent results.
3. Proper Venting and Gas Removal:
Effective venting is crucial in lost foam casting to allow for the escape of gases generated during the pouring of the molten metal. Inadequate venting can lead to defects such as porosity or blowholes. Proper venting design and placement help ensure the successful removal of gases and minimize the risk of defects in the final casting.
4. Mold Preheating:
Preheating the mold prior to pouring molten metal is a best practice in lost foam casting. Mold preheating helps to reduce thermal shock, improve metal flow, and minimize the risk of defects such as cold shuts or incomplete fills. Proper control of mold preheating temperature and duration is essential to achieve optimal results.
5. Pouring Technique and Metal Quality:
Paying attention to the pouring technique and the quality of the molten metal is crucial for successful lost foam casting. Proper pouring techniques, including controlling the pouring speed and direction, help ensure a smooth and uniform flow of metal into the mold cavity. High-quality molten metal with appropriate metallurgical properties, such as alloy composition and cleanliness, is essential for achieving desired casting properties and reducing the risk of defects.
6. Solidification and Cooling Control:
Controlling the solidification and cooling of the casting is vital to achieve dimensional accuracy and minimize the risk of shrinkage or distortion. Employing proper cooling techniques, such as the use of chills or cooling fins, can help control the solidification rate and promote uniform cooling. This ensures consistent and predictable casting results.
7. Quality Control and Inspection:
Implementing a robust quality control process is essential to monitor and inspect the castings throughout the production cycle. Regular inspections, including visual inspection, non-destructive testing, and dimensional measurements, help identify any defects or deviations from the desired specifications. This allows for timely corrective actions and ensures consistent quality.
8. Continuous Process Improvement:
Continuous process improvement is key to optimizing performance in lost foam casting. Regularly evaluating the process, analyzing data, and identifying areas for improvement contribute to refining the process parameters, reducing defects, and enhancing overall efficiency. Embracing new technologies and materials, as well as incorporating feedback from customers and operators, enables ongoing optimization and keeps the process up-to-date with industry advancements.
By applying these techniques and best practices, manufacturers can optimize the performance of the lost foam casting process. This results in high-quality, dimensionally accurate castings with minimal defects, improved efficiency, and increased customer satisfaction.