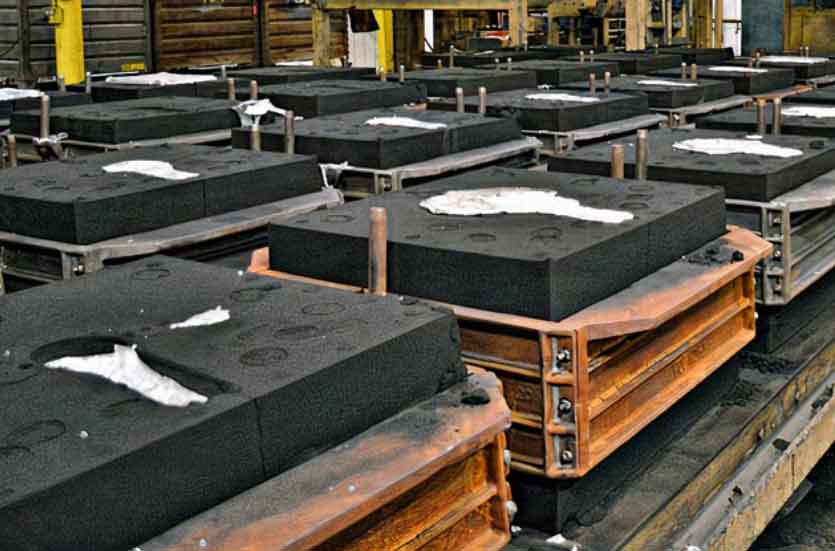
Optimizing resin sand casting for complex shapes and designs requires careful consideration of various factors to ensure successful mold creation and casting processes. Here are some key strategies to achieve the best results when casting intricate and complex shapes using resin sand:
1. Advanced Mold Design:
- Begin with a well-thought-out mold design that accounts for the intricacies of the complex shape. Utilize computer-aided design (CAD) software to model the design accurately, ensuring precise mold cavity dimensions.
2. 3D Printed Patterns and Cores:
- Consider using 3D printing to create patterns and cores, especially for highly detailed and complex shapes. 3D printing allows for rapid prototyping and enables the production of intricate patterns that may be challenging to achieve with traditional pattern-making techniques.
3. Optimal Gating and Riser Design:
- Design an efficient gating and risering system to ensure proper metal flow and feeding during casting. For complex shapes, multiple gates and risers may be required to fill all areas of the mold evenly.
4. Mold Hardening and Curing:
- Ensure proper curing and hardening of the resin sand mold to achieve the desired mold strength and dimensional stability. Precise control over the curing process is critical for maintaining accurate mold dimensions.
5. Selecting the Right Resin Binder:
- Choose a resin binder that offers good flowability and coating properties to reproduce intricate details faithfully. The binder should also provide adequate strength to withstand the metal’s pressure during pouring.
6. Venting and Gas Removal:
- Properly vent the mold to allow gases to escape during metal pouring. This helps prevent defects like gas porosity and ensures the metal fills all areas of the complex shape.
7. Real-Time Process Monitoring:
- Implement sensors and monitoring systems to track mold temperature, humidity, and other process parameters in real-time. This data can help identify potential issues and ensure consistent mold quality.
8. Sand Quality and Control:
- Use high-quality resin-coated sand to achieve uniform mold properties. Implement stringent sand quality control measures to minimize variations in the sand mixture.
9. Tooling and Pattern Inspection:
- Regularly inspect tooling, patterns, and molds to identify any wear, distortion, or damage that could affect casting quality. Prompt maintenance and repair are essential to maintaining precise mold dimensions.
10. Post-Casting Finishing:
- Plan for post-casting finishing and cleaning processes to remove any residual sand and achieve the desired surface finish on the castings.
By carefully implementing these optimization strategies, foundries can successfully produce complex shapes and designs using resin sand casting. The combination of advanced technologies, process control, and attention to detail ensures that the final castings accurately reflect the intricate details and artistic vision of the original design.