Resin sand casting can be a highly effective casting process, but like any manufacturing method, it comes with its own set of challenges. To achieve high-quality results and overcome potential issues, consider the following tips:
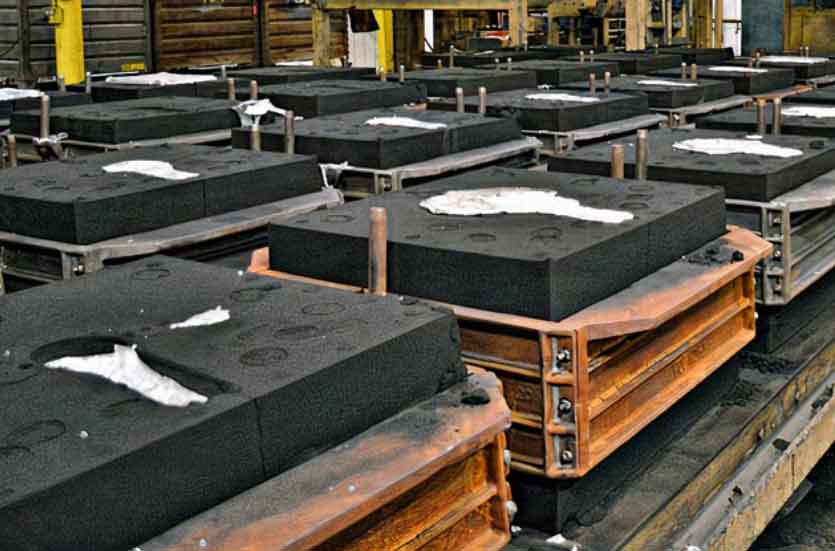
- Select the Right Resin Binder: Choose the appropriate resin binder (furan or urethane) based on your specific casting requirements. Consider factors such as mold strength, curing time, and temperature sensitivity.
- Consistent Sand Mixing: Ensure uniform sand mixing with the resin binder to achieve consistent mold quality. Use proper equipment and techniques to achieve an even distribution of the binder throughout the sand.
- Accurate Curing Conditions: Maintain consistent and controlled curing conditions, such as temperature and humidity, to avoid variations in mold strength and reduce the risk of defects.
- Proper Venting and Gating: Design the mold with proper venting channels and gating systems to allow for the escape of gases and smooth metal flow during pouring.
- Pattern Design Considerations: Pay attention to pattern design, especially for complex shapes, to prevent undercuts and ensure ease of pattern removal from the mold.
- Mold Handling: Handle the molds carefully during assembly and pouring to avoid damage or mold shift that could affect the final casting’s accuracy.
- Monitor Sand Quality: Regularly inspect and monitor the quality of sand used in the process to ensure optimal properties and reduce the risk of defects.
- Quality Control and Inspection: Implement a robust quality control process to inspect the molds and castings at various stages, identifying and addressing any issues promptly.
- Correct Metal Pouring Technique: Use proper pouring techniques to ensure even metal flow and minimize the risk of turbulence or air entrapment.
- Cooling and Solidification: Allow the casting to cool and solidify properly before removing it from the mold to avoid deformation or cracking.
- Post-Casting Finishing: Plan for any necessary post-casting finishing processes, such as trimming, grinding, or surface treatment, to achieve the desired final product quality.
- Training and Skill Development: Ensure that the personnel involved in the resin sand casting process are adequately trained and possess the necessary skills to handle the complexities of the method.
- Continuous Improvement: Regularly review the casting process and identify areas for improvement. Implement changes and best practices to enhance efficiency and quality.
By following these tips, manufacturers can overcome challenges in resin sand casting and achieve high-quality results consistently. Effective mold preparation, proper handling, and stringent quality control are essential for successful resin sand casting operations. With attention to detail and continuous improvement, resin sand casting can offer a cost-effective and reliable method for producing complex castings across various industries.