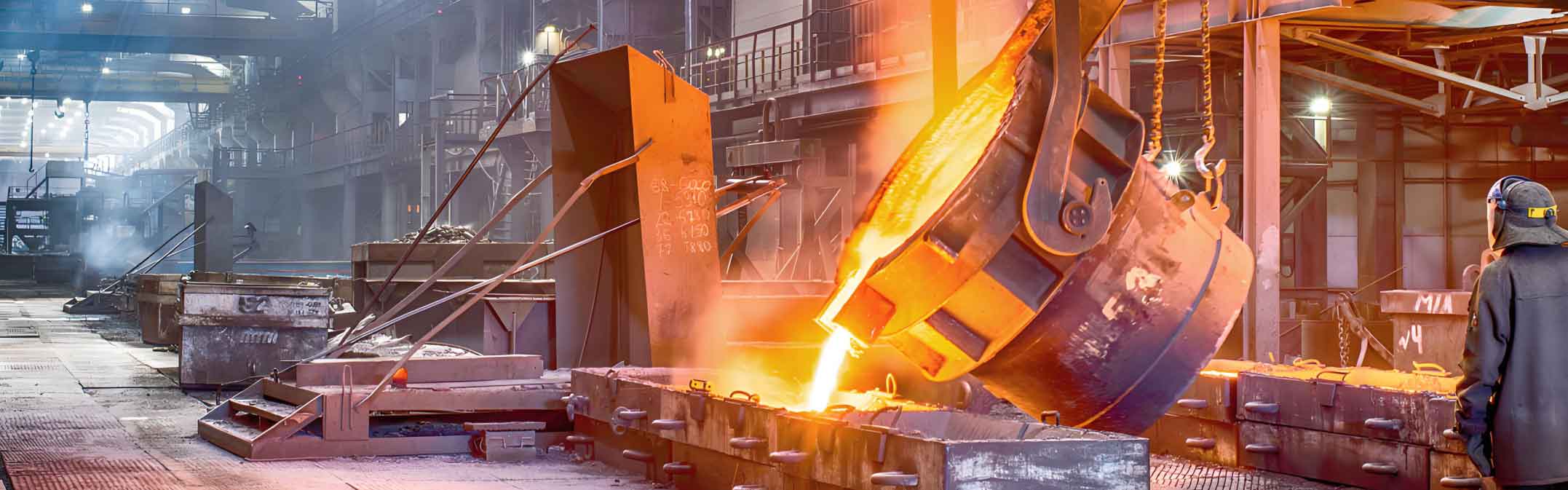
Introduction
Lost foam casting is sophisticated metal casting technique that is widely appreciated for its ability to produce complex and precise components. However, achieving optimal results requires careful design and process optimization. The integration of simulation software in the design and optimization of lost foam casting processes has revolutionized the foundry industry, enabling more efficient, accurate, and cost-effective production. This article explores the various ways simulation software enhances lost foam casting, highlighting key benefits, applications, and best practices.
Benefits of Simulation Software in Lost Foam Casting
Simulation software provides numerous benefits in the design and optimization of lost foam casting processes, enhancing the quality and efficiency of production.
Table 1: Key Benefits of Simulation Software in Lost Foam Casting
Benefit | Description |
---|---|
Enhanced Design Accuracy | Enables precise modeling of complex geometries and intricate details in foam patterns. |
Process Optimization | Facilitates the optimization of process parameters, such as pouring temperature and cooling rates. |
Defect Prediction | Identifies potential defects, such as porosity and inclusions, before actual casting. |
Cost Reduction | Reduces material waste and the need for extensive trial and error in process development. |
Time Efficiency | Accelerates the design-to-production cycle by streamlining the development process. |
List 1: Core Benefits of Simulation Software Integration
- Improved Design Accuracy: Simulation software allows for detailed modeling of foam patterns, ensuring high accuracy and consistency in the final cast parts.
- Optimized Process Parameters: By simulating various process parameters, foundries can optimize conditions such as metal flow, pouring temperature, and cooling rates, leading to higher quality castings.
- Early Defect Detection: Simulation software can predict and visualize potential casting defects, enabling engineers to address issues before actual production, thus saving time and resources.
- Material and Cost Savings: The ability to simulate and test various scenarios reduces material waste and lowers overall production costs by minimizing the need for physical trials.
- Accelerated Production Timeline: Simulation tools streamline the design and optimization process, shortening the time required to move from design to production.
Applications of Simulation Software in Lost Foam Casting
Table 2: Applications of Simulation Software in Lost Foam Casting
Application | Description |
---|---|
Pattern Design | Modeling and optimizing foam patterns for complex geometries and precise dimensions. |
Mold Filling Simulation | Visualizing and optimizing the flow of molten metal into the mold cavity. |
Solidification Analysis | Analyzing cooling rates and solidification patterns to prevent shrinkage and warping. |
Thermal Management | Managing and optimizing thermal conditions during the casting process. |
Defect Analysis | Predicting and addressing potential defects, such as porosity, inclusions, and cold shuts. |
Pattern Design
Simulation software enables the precise design of foam patterns, accounting for complex geometries and intricate details. This ensures that the final cast parts meet exact specifications and reduces the need for post-casting machining.
Mold Filling Simulation
By simulating the flow of molten metal into the mold cavity, engineers can optimize the gating system and pouring techniques to ensure complete cavity filling. This helps in preventing defects such as misruns and cold shuts.
Solidification Analysis
Solidification analysis helps in understanding and controlling the cooling rates and solidification patterns within the mold. This is crucial for preventing defects like shrinkage and warping, which can compromise the structural integrity of the cast parts.
Thermal Management
Effective thermal management is essential for maintaining optimal casting conditions. Simulation software allows for the modeling and control of thermal conditions, ensuring consistent and high-quality castings.
Defect Analysis
Simulation tools can predict potential defects and visualize their occurrence within the casting process. This enables engineers to implement corrective measures in the design phase, thereby reducing the occurrence of defects in the final product.
Best Practices for Integrating Simulation Software
To maximize the benefits of simulation software in lost foam casting, it is important to follow best practices for its integration and use.
List 2: Best Practices for Simulation Software Integration
- Comprehensive Training: Ensure that all relevant personnel are thoroughly trained in the use of simulation software and its applications in lost foam casting.
- Iterative Testing and Validation: Use an iterative approach to testing and validation, continuously refining designs and processes based on simulation results.
- Collaboration and Communication: Foster collaboration and communication between design engineers, foundry technicians, and simulation experts to ensure seamless integration and optimization.
- Continuous Improvement: Utilize simulation software as part of a continuous improvement process, regularly updating models and parameters based on real-world data and feedback.
- Data-Driven Decision Making: Base decisions on comprehensive data and insights provided by simulation software, ensuring that changes and optimizations are well-informed and effective.
Case Studies and Real-World Applications
Case Study 1: Automotive Engine Blocks
In the production of automotive engine blocks, simulation software has been instrumental in optimizing the design and casting process. By simulating the flow of molten metal and solidification patterns, manufacturers have been able to reduce defects, improve dimensional accuracy, and decrease production costs.
Case Study 2: Aerospace Components
Aerospace components, such as turbine blades and structural parts, require high precision and integrity. Simulation software has enabled manufacturers to design intricate foam patterns, optimize thermal management, and predict potential defects, resulting in superior quality cast parts.
Case Study 3: Industrial Machinery Parts
Manufacturers of industrial machinery parts, such as pump housings and gearboxes, have utilized simulation software to streamline the casting process. By optimizing pattern design and process parameters, they have achieved significant improvements in efficiency and cost savings.
Conclusion
The integration of simulation software in the design and optimization of lost foam casting processes offers substantial benefits in terms of accuracy, efficiency, and cost-effectiveness. By enabling precise modeling, optimizing process parameters, predicting defects, and reducing material waste, simulation software has become an invaluable tool for foundries aiming to enhance their operations and product quality.
Table 3: Summary of Benefits and Best Practices
Benefit | Best Practice |
---|---|
Enhanced Design Accuracy | Comprehensive training in simulation software and iterative testing. |
Process Optimization | Collaborative approach between engineers and foundry technicians. |
Defect Prediction | Data-driven decision making based on simulation insights. |
Cost Reduction | Continuous improvement and regular updates based on real-world data. |
Time Efficiency | Seamless integration and communication across all stages of design and production. |
By adopting best practices and leveraging the full potential of simulation software, foundries can achieve remarkable improvements in the mass production of complex parts using lost foam casting, driving innovation and competitiveness in the industry.