Porosity casting defect has always been the most common defect in sand casting gray iron castings. It refers to the smooth holes of different sizes on the internal surface or near the surface of the casting, and the hole wall often has oxidation color. Due to the different gas sources and forming conditions, the shapes and distributions in castings are also different. They are mainly classified as invasive pores, precipitation pores and subcutaneous pores.
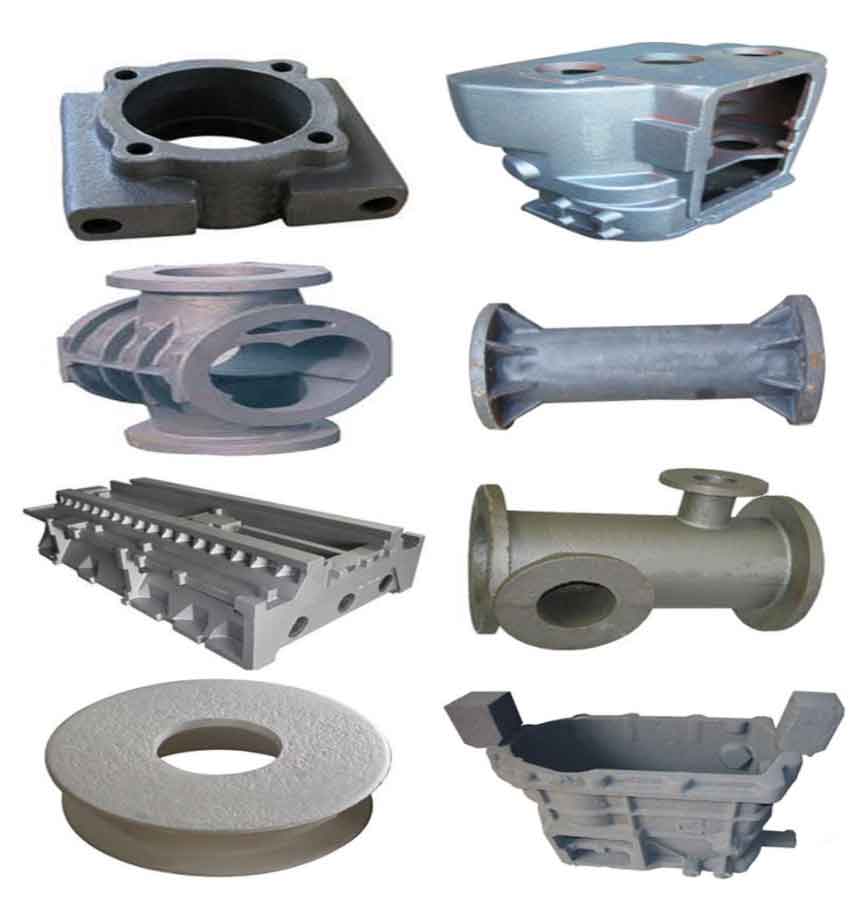
a) Invasive stomata
Such Blowholes in castings are large in size, mostly ellipsoidal or spherical in shape, and often distributed on the outer surface of castings or at the bottom of blowholes. The main reason for their formation is that the gas in the mold is not eliminated from the molten iron. This is the main type of porosity casting defects in gray cast iron cylinder block produced by sand casting. Figure 1 (a) shows the air hole outside the oil passage of the cylinder block, and figure 1 (b) shows the air hole on the upper part of the water jacket of the cylinder block (as shown by the arrow).
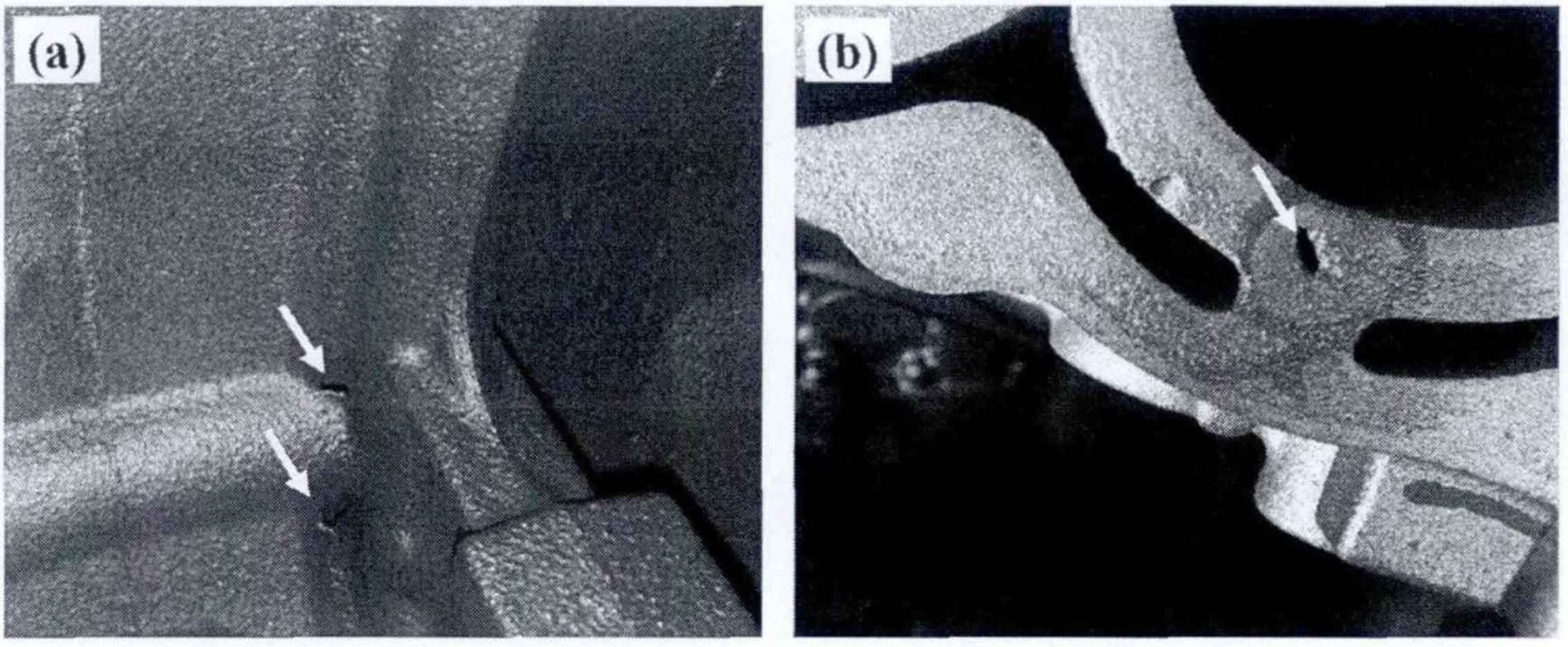
b) Precipitated pore
The distribution of such porosity casting defects is relatively dispersed, mostly on the casting surface, with different shapes and large sizes. In the solidification process of molten iron, the absorbed gas is not completely discharged through the exhaust system, which will precipitate more dispersed pores on the surface of the casting. For such pores, it is necessary to strictly control the temperature of molten iron and the moisture of sand mold and sand core to reduce the formation of such pores.
C) Reactive stomata (subcutaneous stomata)
The pores produced by the gas released due to the chemical reaction between the molten iron and the mold or inside the molten iron will produce a large amount of water vapor under the action of high temperature. The water in the mold will be evaporated and the crystalline water in the clay will be decomposed. Fe, C, Mn and A1 in the gray cast iron react with it to form a large amount of H2, CO and C02, It is called reactive pore. This kind of air hole is regular in shape and often occurs at 2-3mm below the surface layer of the casting. Its size is slightly smaller and its quantity is relatively large. After the subsequent processing of gray iron castings, the porosity casting defects will be clearly exposed, which is also called subcutaneous porosity. Figure 2 (a) shows the subcutaneous air hole at the lower end face of the cylinder block, and Figure 2 (b) shows the subcutaneous air hole at the drill hole of the water pump section (as shown by the arrow).
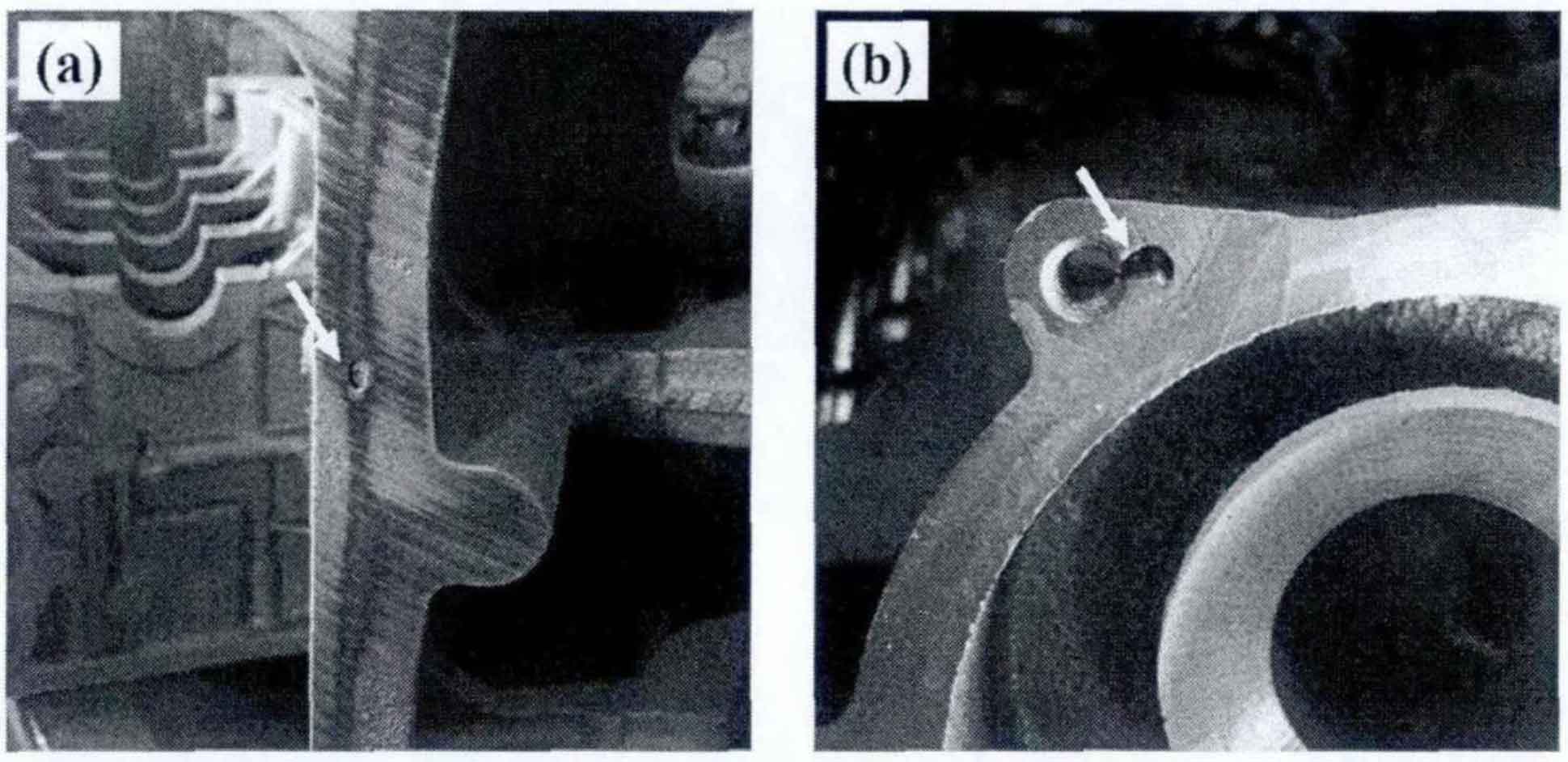