The following figure shows the stress field distribution of bimetal casting liner at different times during solidification. Due to the difference in mechanical properties of the two materials, the color cloud diagram shows that the interface bonding area between carbon steel layer and high chromium cast iron layer is the area with high stress. During the whole solidification process of bimetal casting liner, the internal stress increases with time at the beginning, but after about 40s, the material yields, and the internal stress decreases with time. At 90s, the areas with large residual stress are mainly in the inner arc and near the bimetal bonding interface, The results show that the stress concentration at the interface should be paid attention to during solidification, and appropriate heat treatment process should be adopted to eliminate the residual stress and prevent the material from cracking at the joint surface.
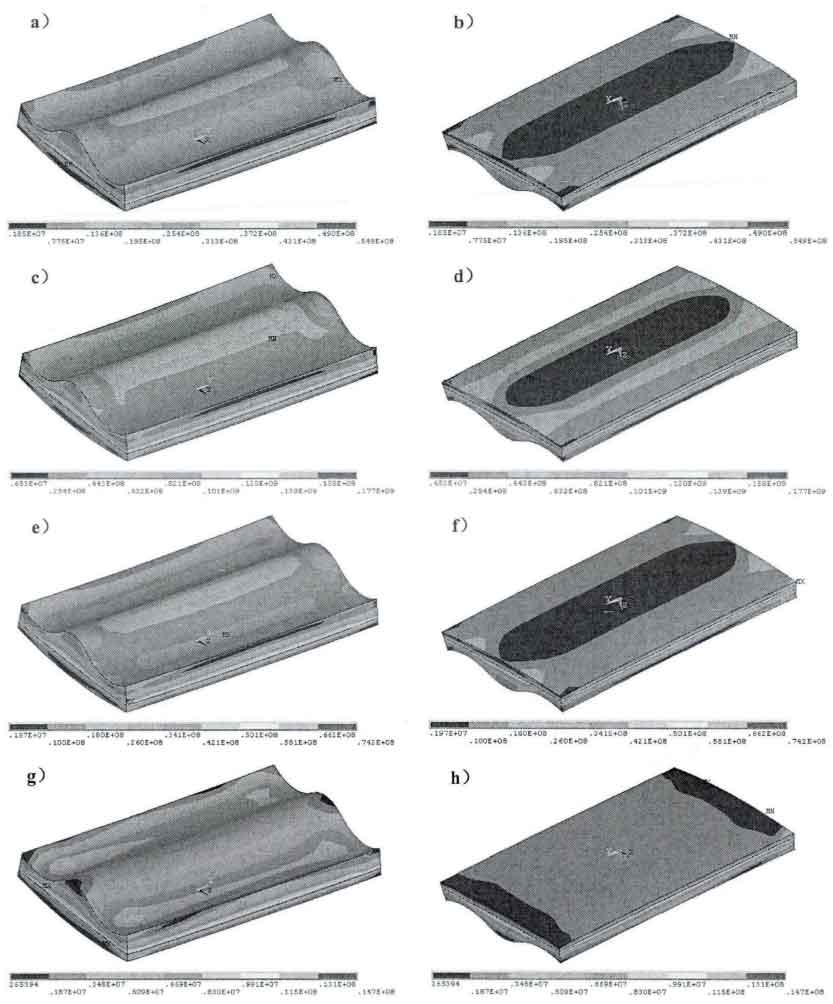
The following figure shows the cloud diagram of strain field distribution of bimetallic casting lining plate at 87s of solidification process, which is consistent with the analysis results of stress field. The bimetallic side plate has the maximum deformation in the bonding interface area and corner area. The black dashed box in the figure shows the geometric outline of the original casting lining plate of the casting mold. It is found by comparison that in order to ensure the dimensional accuracy of the casting lining plate to be installed smoothly in the ball mill, it can be considered to reduce the design radius of the circular arc surface of the carbon steel layer of the casting lining plate. When the casting lining plate solidifies and shrinks, it will automatically increase the radius to compensate for the deformation to adapt to the installation circular arc surface in the ball mill.
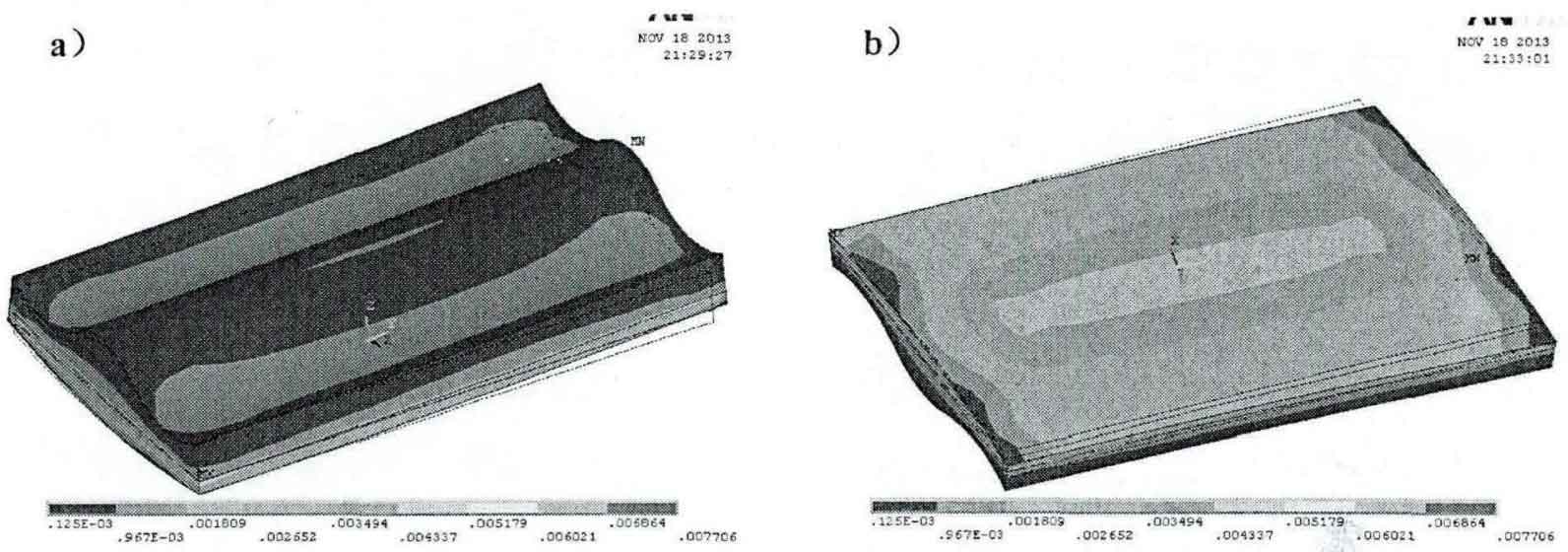