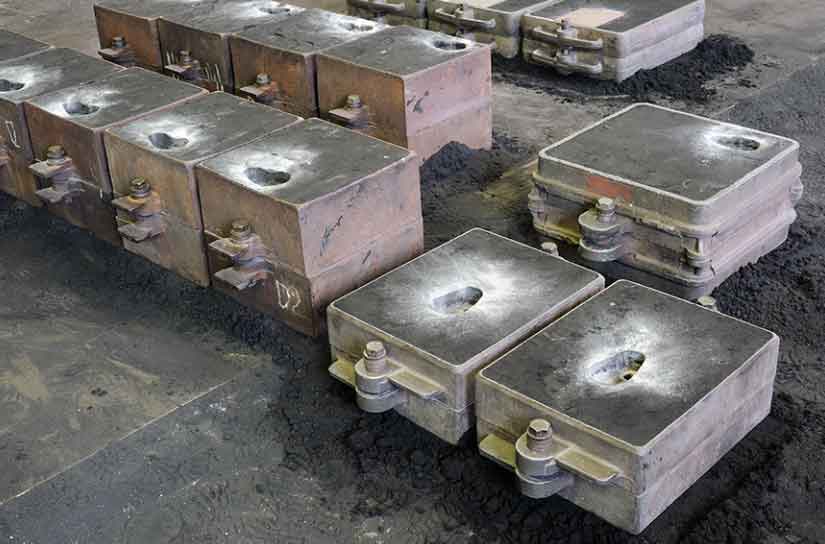
Resin sand casting is a versatile and widely used casting technique that involves the use of resin-bonded sand molds to create complex metal parts. This method offers several advantages such as precision and efficiency in the casting process. Let’s explore these aspects further.
Precision:
Resin sand casting allows for the production of highly precise and intricate parts. The mold is created by mixing resin with high-quality sand, which forms a strong and durable mold cavity. The mold can accurately capture all the details of the pattern, resulting in precise dimensional accuracy and surface finish of the final cast part. This makes resin sand casting suitable for applications that require tight tolerances and complex geometries.
Efficiency:
Resin sand casting offers various efficiency advantages in the casting process:
a. Cost-effective tooling: Compared to other casting methods like investment casting or die casting, resin sand casting has relatively low tooling costs. The molds are constructed using reusable patterns and can be easily modified or repaired, reducing the overall production expenses.
b. Quick production turnaround: Resin sand casting enables rapid production cycles due to its shorter setup and preparation time. The sand molds can be prepared and assembled quickly, allowing for faster production rates and shorter lead times compared to other casting methods.
c. High production yield: Resin sand casting offers high production yield rates with minimal material waste. The molds are typically designed to accommodate multiple cavities, allowing for the simultaneous production of multiple parts in a single casting operation. This increases the overall efficiency and productivity of the process.
d. Versatility and flexibility: Resin sand casting can be used for a wide range of metals, including ferrous and non-ferrous alloys. This versatility allows manufacturers to produce parts with varying mechanical properties and characteristics according to their specific requirements. Additionally, resin sand casting is suitable for both low and high volume production, making it a flexible option for different production scales.
To further enhance the precision and efficiency of resin sand casting, manufacturers often employ advanced techniques such as computer-aided design (CAD) and simulation software to optimize mold designs, identify potential defects, and simulate the casting process before actual production. These tools help to reduce errors, improve process control, and achieve higher overall quality.
It’s worth noting that while resin sand casting offers precision and efficiency benefits, it may not be the most suitable method for every casting application. Factors such as part size, complexity, material selection, and required quantities should be considered when choosing the appropriate casting technique. Consulting with experienced casting professionals or engineers can provide valuable insights and recommendations tailored to specific project requirements.