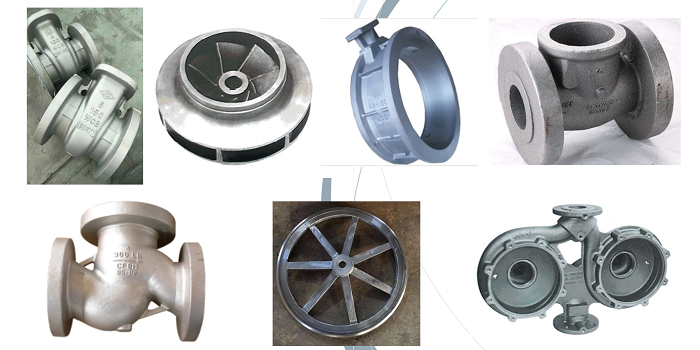
Use of grey cast iron
Gray cast iron plays an important role not only in China’s economic production, but also in the world’s manufacturing industry. It is the most widely used casting metal material in the world’s industrial production. In the whole manufacturing industry, iron castings account for about 45% – 90% of the weight of each production machine.
According to the general survey results of 2014 casting output of modern casting magazine, the global casting output reached 103.6 million tons in 2014. The output of gray iron parts has reached 474.62 million tons. In 2015, the output of gray iron parts in China was negatively increased for the first time due to the impact of the manufacturing environment, but it still reached 20.2 million tons, accounting for 44.3% of China’s casting output.
In 2016, there were 30000 foundries in China, including 56.7% of grey cast iron enterprises, 16.7% of cast steel enterprises and 26.6% of non-ferrous metal enterprises. However, according to the data, in 2016, the export volume of China’s industrial grey cast iron was 316000 tons, with an average price of 833 US dollars / ton, while the import volume was 3200 tons, with an average price of 5174 US dollars / ton. It can be seen from the above that China’s output of gray iron is huge, but due to various problems in production, the quality of gray iron castings in China is poor, and the price is far lower than that of imported gray iron castings, which to a large extent hinders China’s pace of becoming a powerful foundry country.
(1) The number of enterprises is huge, the production is backward, the scale is small, and the production energy consumption is high. At present, although China has the largest foundry in the world, the average productivity of foundry enterprises is only 1483kt / A, which is in the bottom of the top ten countries in total production. The energy consumption per ton of iron castings in China is 500kg-650kg standard coal, while that in developed countries is 300kg-400kg standard coal. In addition, the starting point of China’s foundry mechanization and automation is relatively low. Therefore, with the development of both, the energy consumption of castings will still increase.
(2) The overall quality of castings in China is poor. The defects of segregation and inclusions in castings, especially in large castings, lead to the inconsistency of composition and properties of castings. There is no systematic solution to the problem of shrinkage cavity. In addition, due to the uncontrollable deformation, the machining allowance of casting is larger than that of foreign countries, which increases the cost. All of these lead to the quality of the waiting parts in our country is always inferior to that of the foreign casting powers.
(3) China’s foundry production mode and process design method are backward. Most of the foundries in China, except a few batch casting manufacturers, adopt assembly line modeling, and the rest adopt shock molding machine or manual modeling. In the aspect of process design, China’s foundry enterprises still mainly rely on the experience of technologists, while the use of foundry simulation software is relatively small and mostly for reference, lacking integrity and reliability. Although the overall environmental problems of manufacturing industry bring challenges to China’s foundry industry, with the wave of industrial globalization, it also brings opportunities for China’s foundry industry to embark on the road of prosperity. To improve the external quality of castings, reduce casting defects and improve production efficiency is the way to face the market. Therefore, it is very important to reduce the trial production cost of castings by using the casting simulation software, so as to speed up the product renewal cycle, so as to improve the competitiveness of China’s casting market.
Service performance of grey cast iron
W can be widely used in the manufacturing industry because of its excellent performance.
(1) . excellent casting performance. Most of the grey cast iron used in industry is hypoeutectic cast iron, so it has strong filling ability and can cast more complicated and skillful parts. In addition, there is a graphite precipitation process in the solidification process of gray iron, so there is a feeding process, which reduces the probability of shrinkage porosity and production quality cost to a certain extent.
(2) Excellent wear resistance and shock absorption. Graphite has good lubricity, and the grey cast iron has good adsorption to the lubricating oil, so the wear resistance of the casting is improved. The flake graphite structure of grey cast iron can effectively reduce the generation of vibration, which makes it widely used in machine tool industry.
(3) Good compression resistance and low production cost. The compressive strength of grey cast iron is close to 600-800mpa of steel, but its production cost is far lower than that of cast steel, which is also one of the reasons why it is widely used in machine tool industry.