In recent years, with environmental requirements and concerns for worker health, the number of enterprises using alkaline phenolic resin self hardening sand technology to produce steel castings has increased rapidly. Compared with other types of resin self hardening sand, ester cured alkaline phenolic resin sand has lower gas generation and does not contain phosphorus, nitrogen, etc. The tendency of phenolic resin sand castings to produce pores is relatively small. However, due to various reasons and poor production process control, there are still porosity defects in the production of phenolic resin sand castings, resulting in a large number of phenolic resin sand castings being scrapped, causing great losses to the enterprise. Therefore, this article focuses on the problem of air holes and inclusions in the half shaft sleeve of a certain automobile, and finds solutions to avoid further scrapping of phenolic resin sand castings.
1. Analysis of the structure and casting process of phenolic resin sand castings
The layout of the casting riser for a certain automotive connector is shown in Figure 1. The phenolic resin sand mold casting is made of ZG35 steel, and its chemical composition (mass fraction,%) is 0.30C, 0.50Si, 0.90Mn, Cr0.5. The phenolic resin sand mold casting is a rotary casting with a simple structure and adopts a side injection pouring system. Inner gate entrances are set at the positions of the 1st and 2nd risers, with a straight gate diameter of 70mm.
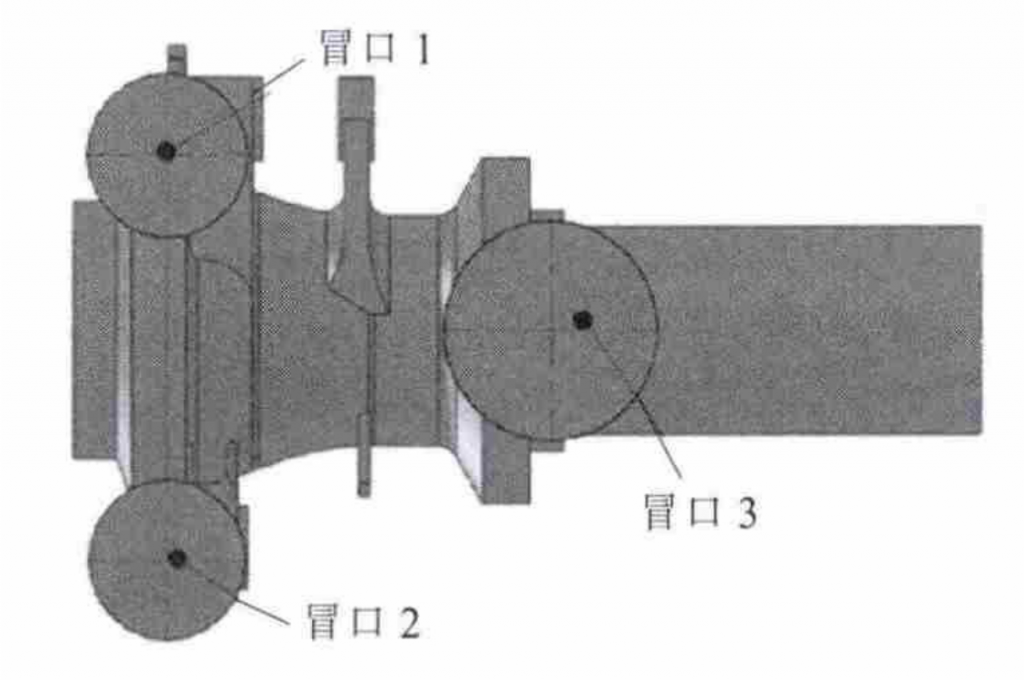
Set up risers in the hot section and thick parts. The size of the 1st and 2nd risers is approximately 150 mm x 300 mm, while the size of the 3rd riser is approximately 200 mm x 300 mm, both of which are exposed risers. The mass with a riser is 402 kg, and after removing the riser, it is 232 kg. The production rate of the process is 232/402=57%. The molding sand used is alkaline phenolic resin sand. New sand accounts for about 30% of the molding sand, recycled sand accounts for 70%, phenolic resin is added at 2% of the sand content, and curing agent ester is added at 25% of the resin content. After drying the sand mold and sand core, apply alcohol based coating on the surface 3-4 times. The smelting equipment is a 2000 kg acidic lining medium frequency induction furnace. The melting temperature of molten steel is 1560-1580 ℃, and the pouring temperature is 1540-1560 ℃.
2. Analysis of pore formation
Anatomical penetration was performed on phenolic resin sand castings, and the inspection results are shown in Figure 2. The main positions of pores in phenolic resin sand castings are distributed in the upper part of the phenolic resin sand castings in the middle of the three risers, far away from the risers, and near the upper part of the sand core. The majority of pores are invasive pores, and there are no significant cracks. In addition, inclusions appeared near the inner gate (Figure 2 (b)). Analyzing gas sources mainly includes:
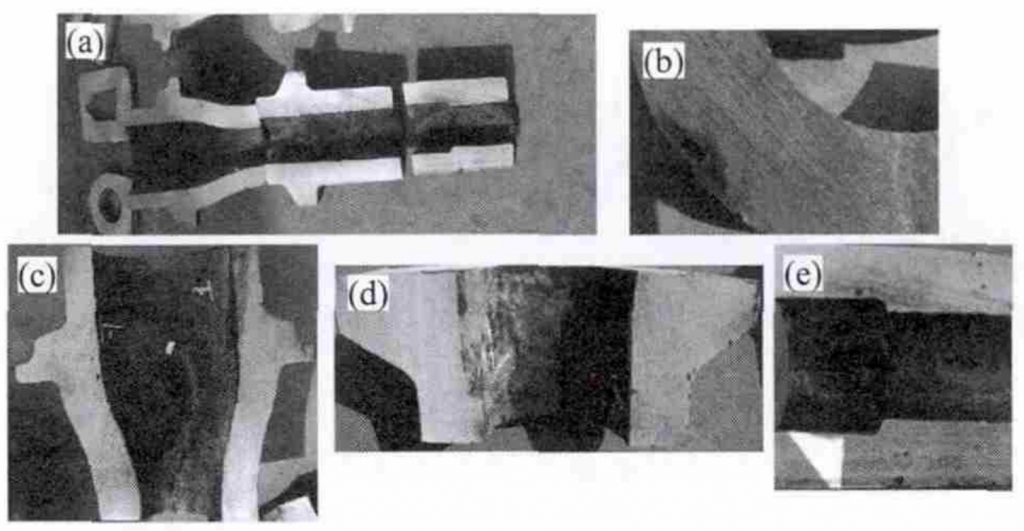
① Invading pores. Derived from moisture in sand molds, sand cores, and risers. Before the surface of phenolic resin sand castings solidifies into a shell, the gas generated by the heating of sand molds, sand cores, and other molding materials invades the molten metal to form bubbles and form pores, which are spherical or pear shaped.
② Reaction pores. Gas is generated by the chemical reaction between metal liquid and sand molds, sand cores, inclusions, and compounds dissolved in them, which is distributed under the surface of phenolic resin sand castings. In addition, poor deoxidation of the steel during smelting (Figure 2 (b)) leads to the formation of bubbles. If they cannot float up, they are also prone to form during the solidification period of the steel.
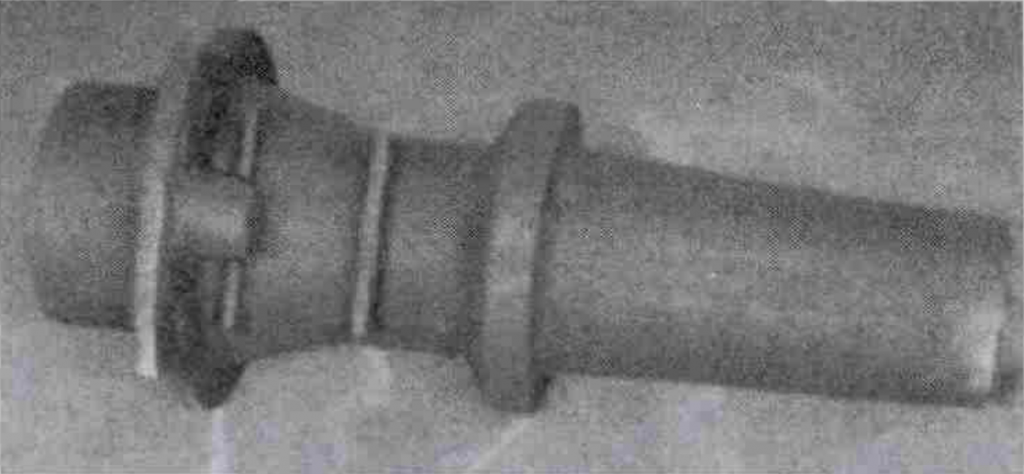
③ Precipitation pores. Gas is generated in the steel liquid due to factors such as moisture and rust in the furnace material.
Based on the above analysis, improve the casting process.
3. Process improvement
3.1 Melting and pouring process
During the smelting process, it is advisable not to use undeveloped or rusted scrap steel and pig iron as much as possible. The steel liquid should be fully deoxidized to reduce inclusions. In addition, the reduction period time should be appropriately controlled. If the reduction period time is too long, due to the loose reduction slag, hydrogen, nitrogen and other gases are easy to invade, and it is also easy to increase the gas content of the steel liquid.
3.2 Improvement of phenolic resin sand casting process
(1) Phenolic resin sand mold casting process for gating and riser. Change the original pouring channel and adopt an open bottom pouring system to ensure smooth filling. In addition, in order to prevent excessive contact between high-temperature steel liquid and sand mold during the initial pouring stage, and to avoid the formation of invading pores, various pipe fittings made of refractory materials should be used as much as possible in the pouring system. The riser should also use specially made dry insulation riser sleeves made of refractory materials as much as possible.
(2) Phenolic resin sand casting molding process. Select qualified shaping materials. Pierce air holes in the upper mold away from the riser and between the risers. A triangular foam plate is placed between the risers to enhance the permeability of the sand mold. It is necessary to sandblast the external cold iron to remove rust and oil stains. After cleaning, a protective layer should be applied to its working surface and stored in a dry place. In order to reduce the gas generation of the sand core, the pre made core is not allowed to be placed directly on the ground. It is best to dry the sand core before pouring, and a hollow core bone should be used. A smooth exhaust channel must be set at the core head to allow the gas in the sand core to be quickly discharged from the mold.
4.Conclusion
The porosity of steel castings produced by self hardening alkaline phenolic resin sand is mainly invasive porosity. Reasonably set sand mold and sand core vent holes, adopt hollow sand cores, place triangular foam plates between risers, and adopt various pipe fittings made of refractory materials in the gating system to enhance the permeability of sand mold and prevent air holes. After improving the process, sound and high-quality phenolic resin sand castings can be poured (Figure 3).