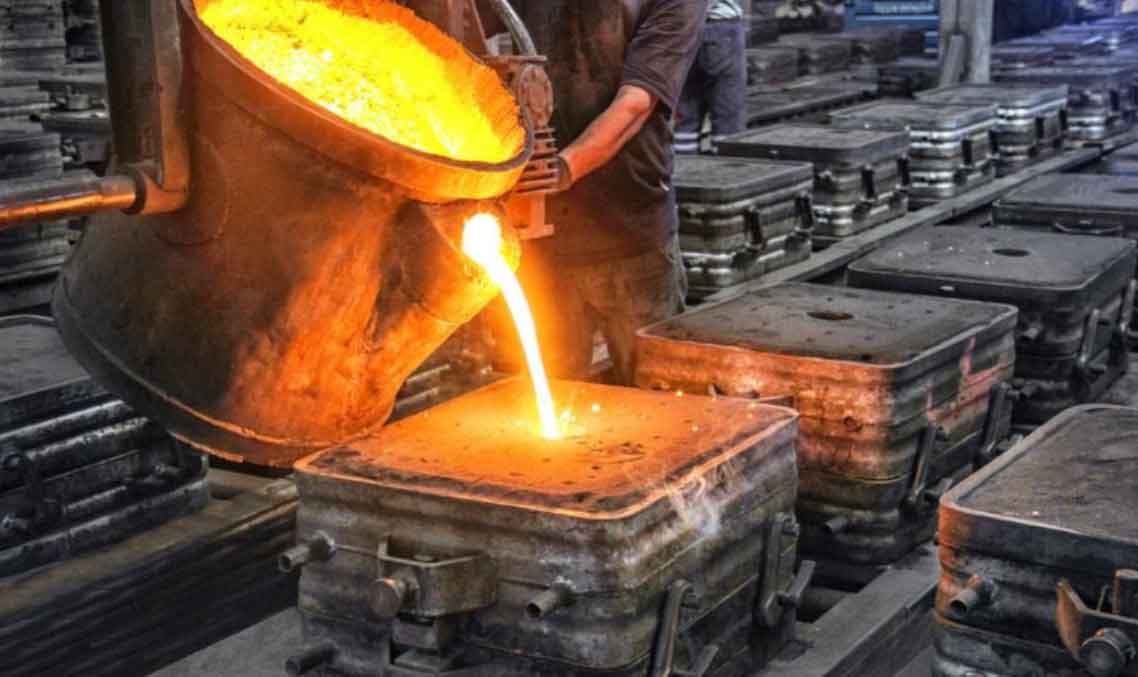
Sand casting manufacturers are pioneering new techniques by integrating advanced technologies such as 3D printing into their traditional processes. One significant advancement is the adoption of sand 3D printing, which allows for the direct creation of molds and cores from digital models without the need for traditional pattern-making. This innovation not only speeds up the production process but also enhances design flexibility, allowing for the creation of complex shapes and internal features that were previously difficult or impossible to achieve with conventional methods.
Additionally, the automotive industry is significantly benefiting from these advancements. Companies like Tesla and General Motors are using large-scale sand 3D printing for gigacasting— a process that involves casting large, single-piece components for vehicles. This method is crucial in manufacturing electric vehicles as it simplifies the assembly process, reduces production costs, and improves vehicle structure’s integrity and quality. The use of 3D printed sand molds is pivotal for rapid prototyping and production, aligning with the broader manufacturing strategies aimed at efficiency and cost reduction.
These innovations in sand casting manufacturers are not only revolutionizing product development by reducing time and costs but are also enhancing the capabilities of casting to meet modern engineering demands. This marks a significant shift towards more sustainable and efficient manufacturing practices in the industry.
In addition to sand 3D printing, sand casting manufacturers are exploring other innovative techniques to enhance their processes. Investment casting, also known as lost wax casting, has been augmented by 3D printing to improve both efficiency and design flexibility. By 3D printing the wax models, manufacturers can bypass the need for hard tooling at the beginning of the casting process, thus speeding up production timelines and enabling greater design intricacies without additional costs. This method is particularly beneficial for producing low-volume, high-complexity components across various industries, including aerospace and medical sectors.
Moreover, the integration of these new technologies not only supports more rapid product development cycles but also allows for better customization and adaptation to specific requirements. The ability to quickly produce and iterate prototype models using 3D printing aids significantly in product refinement, helping designers and engineers to fine-tune their products more effectively before committing to large-scale production.
These advancements underscore a broader trend within manufacturing towards greater automation and digitization. Sand casting manufacturers who adopt these technologies can expect not only to improve their product offerings but also to position themselves more competitively in a market that increasingly values speed, precision, and innovation. As these technologies continue to evolve, they will likely set new standards for quality and efficiency in sand casting and beyond.
Continuing the exploration of new techniques in sand casting manufacturers, the industry is also moving towards more sustainable practices. Environmental considerations are becoming a priority, with innovations focusing on reducing waste and improving energy efficiency. For instance, the use of recycled materials in the sand casting manufacturers and the adoption of more energy-efficient furnaces are steps towards greener manufacturing processes.
Technological integration extends beyond 3D printing; digital modeling and simulation software are increasingly used to predict casting outcomes, optimize material usage, and minimize defects. These tools allow for precise control over the casting manufacturers, reducing material waste and improving the quality of the final product.
The evolution of Industry 4.0 technologies, such as the Internet of Things (IoT) and artificial intelligence (AI), is also making its way into sand casting manufacturers. These technologies enable better monitoring and control of the casting environment, predictive maintenance of equipment, and optimization of production schedules based on real-time data. This leads to increased productivity, higher quality products, and reduced downtime.
As these technological and sustainable innovations continue to develop, they reshape the sand casting manufacturers, driving it towards a more efficient, precise, and environmentally friendly future. These advancements not only benefit the manufacturers but also enhance the overall competitiveness of the industries they serve, from automotive to aerospace, by delivering superior products in a more cost-effective and sustainable manner.
The drive toward even more innovative and sustainable techniques in sand casting manufacturers is poised to leverage the emerging potential of machine learning and big data analytics. These technologies are being integrated to further refine production processes, enhance quality control, and predict potential defects before they occur. By analyzing vast datasets collected during the casting processes, predictive models can be developed to improve the consistency and reliability of cast products.
Furthermore, there is a push to develop more adaptive and flexible manufacturing systems within sand casting manufacturers. This includes the utilization of robotic automation to handle and process molds, which can improve precision and reduce labor costs. Robots can also operate in environments that are hazardous to human workers, such as high-temperature areas or those with airborne particulates, thereby increasing safety.
Lastly, the circular economy is becoming a significant aspect of the future of sand casting manufacturers. This involves not only using recycled materials but also designing products and processes that are inherently more recyclable at the end of their life. Efforts to make molds reusable or easier to recycle can significantly decrease environmental impacts and material costs.
As these technologies mature, the sand casting manufacturers will likely see a continued evolution towards a more digitized, automated, and sustainable approach. This transformation will enable sand casting manufacturers to meet the increasing demands of modern industries more effectively while also adhering to stricter environmental regulations and sustainability goals.
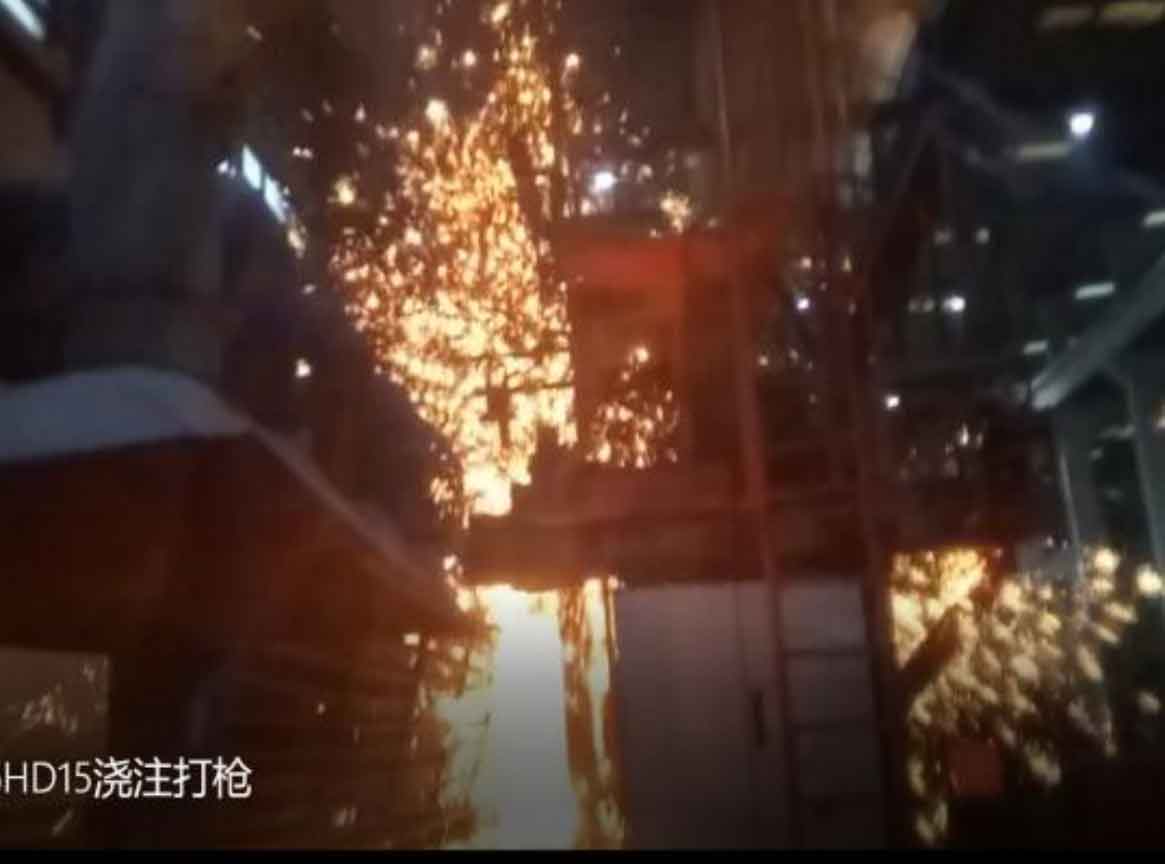
As the sand casting manufacturers continues to evolve, there is an increasing focus on integrating more advanced digital tools and ecological practices. These developments are not only transforming the way products are made but also how the industry addresses global challenges like resource scarcity and environmental degradation.
Advancements in Material Science: One significant area of research is in the development of new materials and binders that are more environmentally friendly and that perform better under stress. Innovations in bio-based binders, which are derived from renewable resources, are particularly promising. These materials not only help reduce the industry’s carbon footprint but also offer improved recycling capabilities.
Customization through Digital Integration: The digital transformation of sand casting extends to enhanced customization capabilities. With advanced CAD software and simulation tools, manufacturers can now create highly customized products tailored to specific client needs with greater accuracy and much less material waste. This capability is crucial in industries such as healthcare and aerospace, where bespoke components are often required.
Training and Development: To fully capitalize on these technological advancements, there is also a growing emphasis on skills development within the workforce. Training programs focused on digital literacy, robotics, and environmental management are becoming more prevalent. These programs are essential for equipping workers with the skills necessary to operate advanced machinery and software, ensuring that the workforce can adapt to and embrace new technologies.
Global Collaboration and Knowledge Sharing: Finally, there is a trend towards greater collaboration across the industry and with academic institutions to foster innovation. Through partnerships and joint ventures, companies are pooling resources and knowledge to tackle common challenges and push the boundaries of what can be achieved in sand casting manufacturers.
As the industry embraces these changes, it continues to set new benchmarks for efficiency, quality, and sustainability. The ongoing integration of cutting-edge technologies and sustainable practices is not only enhancing the capabilities of sand casting manufacturers but also ensuring its relevance and viability in the future economy.
The continuous advancement in sand casting manufacturers signals a transformative era that will likely reshape the manufacturing landscape globally. The future of sand casting hinges not only on technological innovation but also on sustainable development and global collaboration.
Sustainability and Green Manufacturing: The push towards sustainable practices is leading to the exploration of greener materials and processes that minimize environmental impact. Innovations such as using reclaimed sand or developing less energy-intensive casting processes are examples of how the industry is adapting to environmental concerns.
Enhanced Quality Control through AI: The application of artificial intelligence (AI) in sand casting manufacturers set to revolutionize quality control. AI can analyze data from the casting process in real-time to predict and rectify potential defects, enhancing product reliability and reducing waste.
Virtual and Augmented Reality: The use of virtual reality (VR) and augmented reality (AR) in training and production processes represents a significant leap forward. These technologies can simulate casting processes for training purposes without the need for physical resources, and they can also guide workers through complex tasks in real-time during actual production.
Blockchain for Supply Chain Transparency: Blockchain technology could also play a role in enhancing transparency and traceability throughout the casting supply chain. By securely recording transactions and tracking materials, blockchain could help ensure compliance with environmental standards and facilitate more efficient resource management.
Global Standards and Regulations: As the industry evolves, so too will the need for standardized global regulations that ensure safety, quality, and environmental protection. Developing these standards collaboratively at the international level will be crucial to the industry’s future, especially as markets and supply chains become increasingly interconnected.
These emerging trends highlight the dynamic nature of the sand casting manufacturers as it embraces innovation while addressing both economic and environmental challenges. As this sector continues to evolve, it will undoubtedly contribute to shaping a more efficient, sustainable, and technologically advanced manufacturing environment.