According to the structural characteristics of the product and referring to the results of similar products after production, two process designs were carried out for this end cap in the simulation phase, the small mouth up scheme and the large mouth up scheme, as shown in Figure 1. Firstly, the UG software is used to draw the 3D entity of sand casting, and the pouring system process is drawn according to the hot spot. The sand casting, runner, chill, riser, sand box and subsidy are respectively exported to STL, and then entered into MAGMA software for theoretical process simulation.
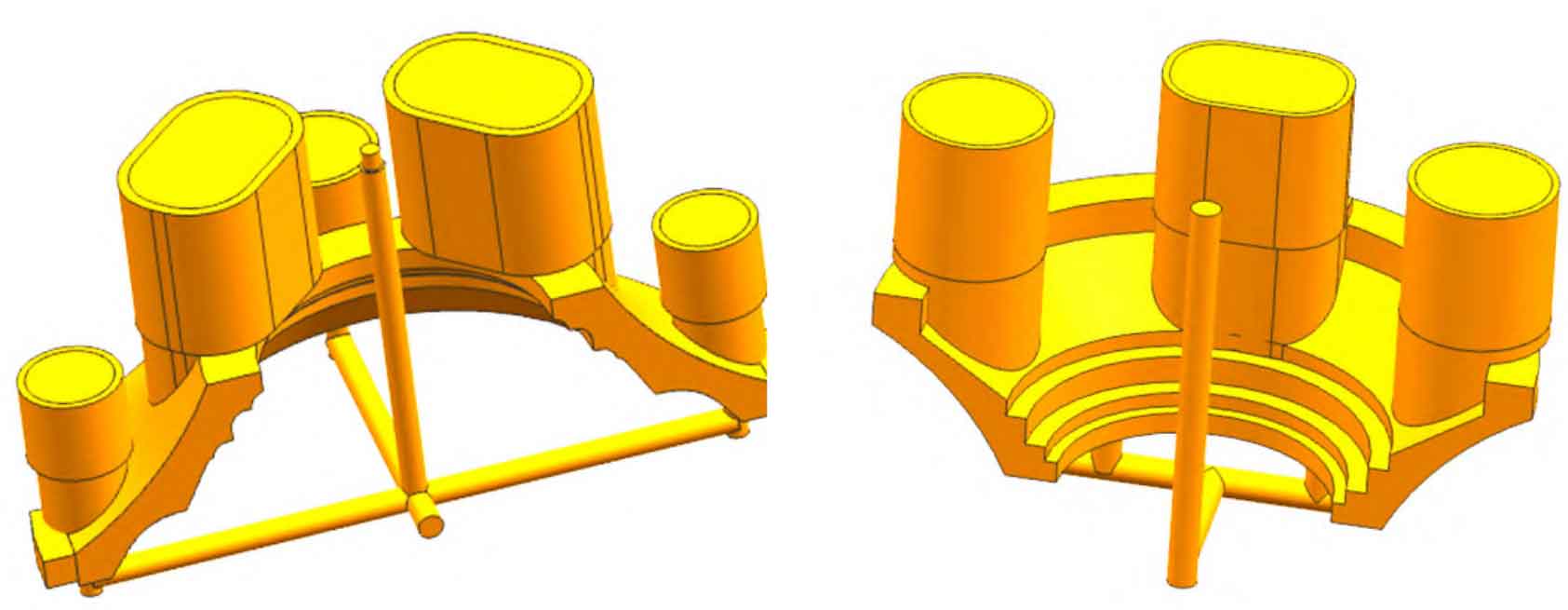
1. Analysis of body solidification simulation results
The treatment before simulation adopts grid division, and some parameters are set as follows: the number of grids is 2000 000, and the nozzle is φ 60 mm, the pouring temperature is 1560 ℃, the pouring speed is 20 s, and the operating parameters adopt the system default values. From the MAGMA solidification results of sand casting body, it can be seen that there are three separate layers of disconnected hot spots in both schemes, as shown in Figure 2.
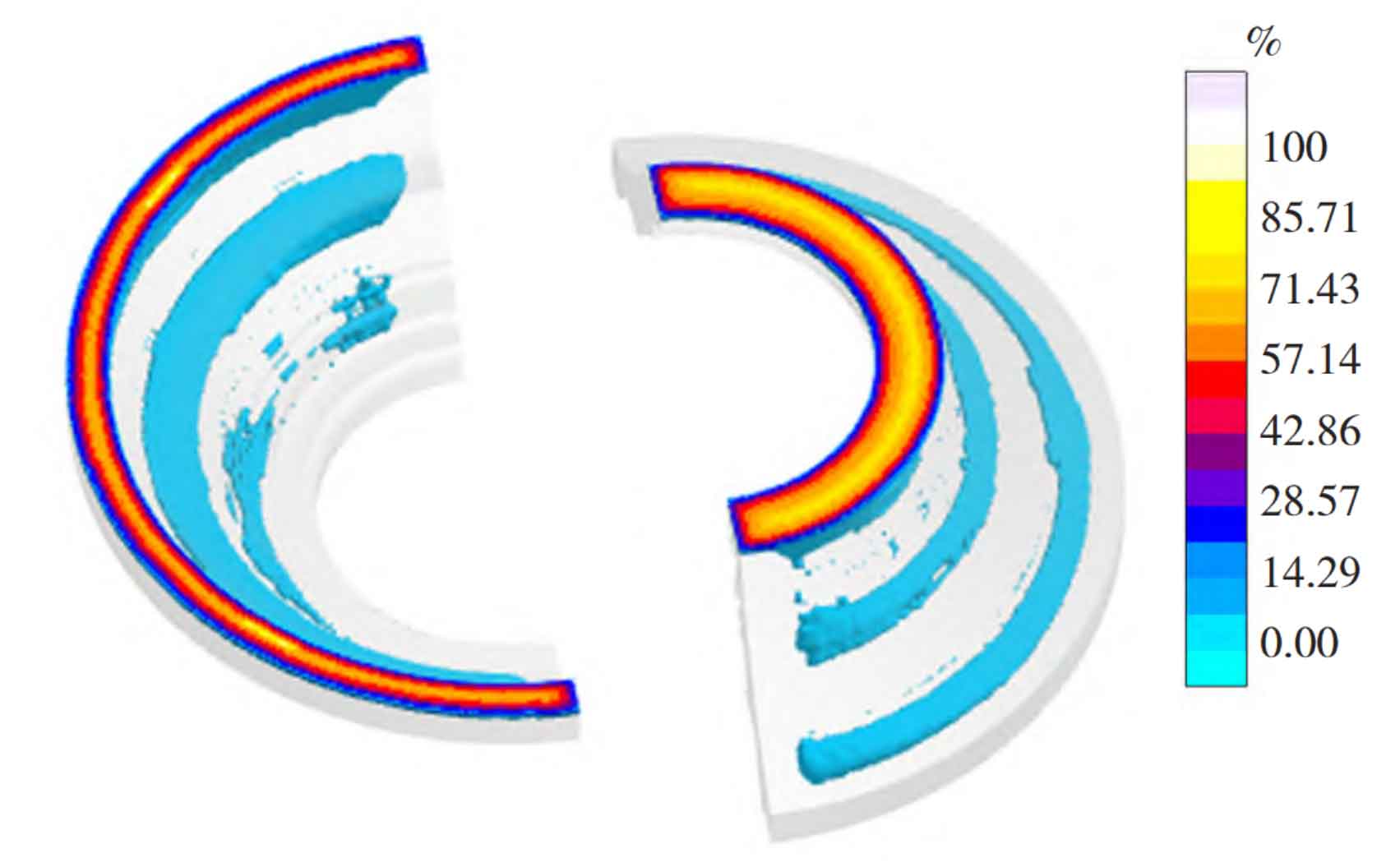
In order to ensure the overall compactness of the sand casting, it is necessary to consider the feeding of the diameter end face direction and the feeding of the middle part of the end cover. The top and bottom are connected by means of a subsidy. According to the bottom layer of the hot spot, a conformal subsidy placed at the inner cavity of the sand casting is drawn to form a gradient from top to bottom to meet the feeding of the sand casting and facilitate the sequential solidification of the sand casting.
2. Solidification simulation analysis of slag inclusion and gas gathering results
For the process scheme with the small mouth facing up, one 520 mm riser is used at the top × 350 mm × 450 mm oval heat insulation exposed riser, 2 nos φ 400 mm × 450 mm cylindrical heating and insulation open riser is used for feeding sand castings.
For the process plan with the big mouth facing up, 3 are used at the bottom of the riser φ 225 mm × 300 mm cylindrical heating insulation concealed riser and two 520 mm at the top × 350 mm × 450 mm oval heat insulation exposed riser, 2 nos φ 350 mm × 450 mm cylindrical heating and thermal insulation open riser is used for feeding sand castings.
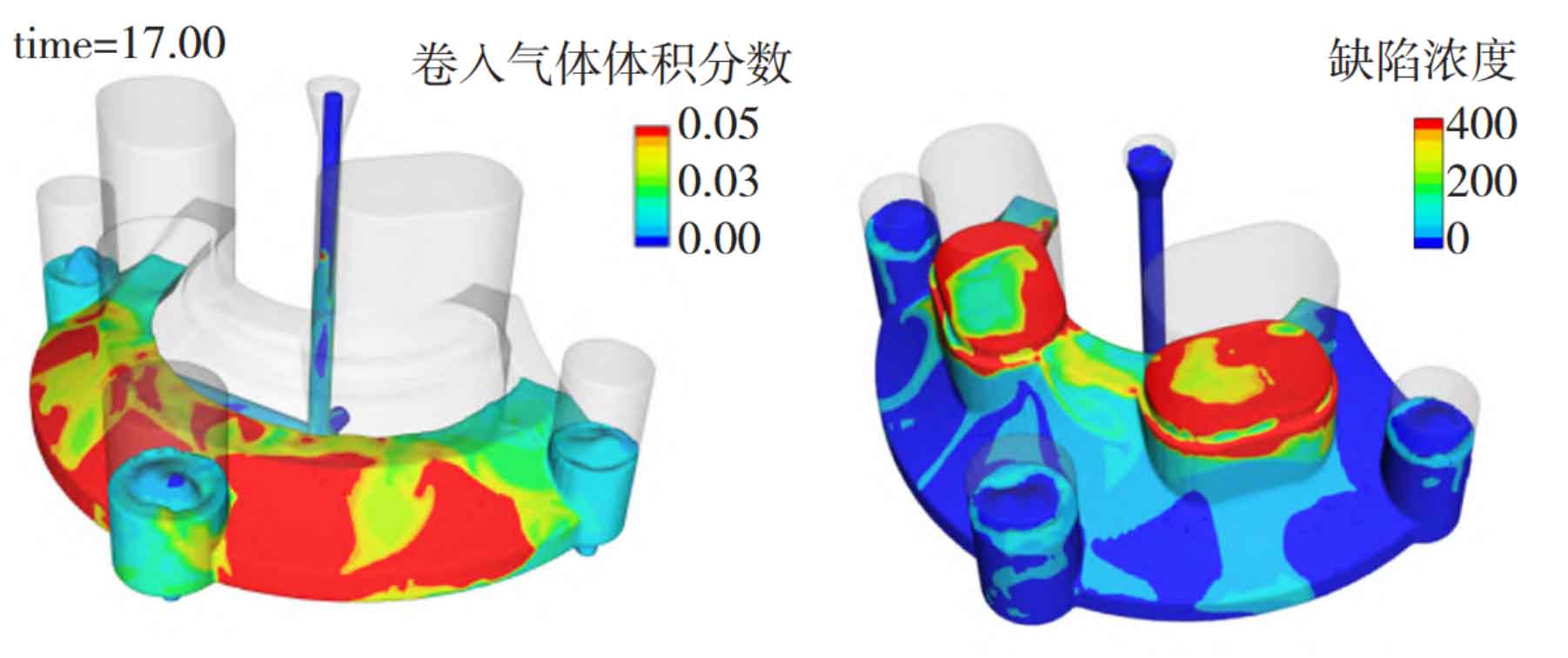
The simulation results are shown in Fig. 3 and Fig. 4. The simulation results show that compared with the big head up scheme, the small head up scheme will form slag inclusions to varying degrees on the surface when filling to about 16s. According to the product quality requirements, the small mouth up method can collect the slag inclusion defects into the riser, and the effect of slag collection and gas collection at the riser is obvious. Therefore, the process scheme is based on the small mouth up production.
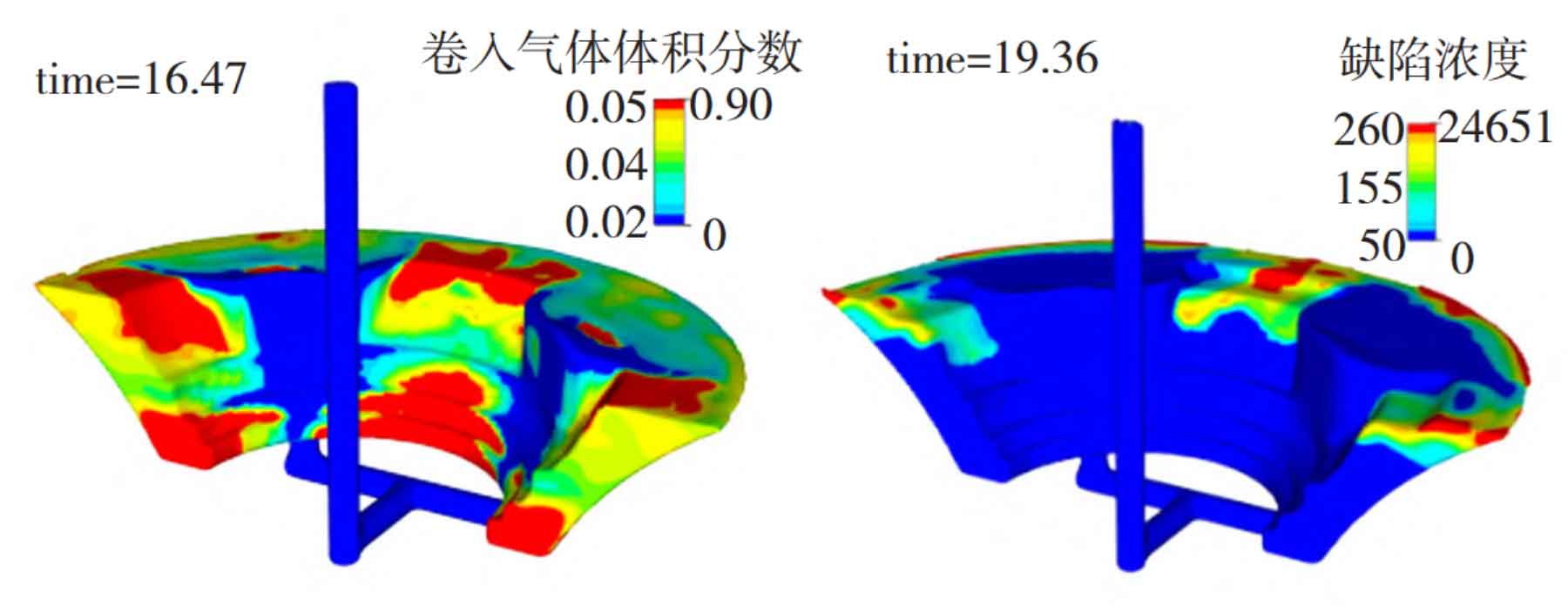