1.Optimize the sprue
The vertical sprue is changed to a “2” shape sprue, that is, a bend is set on the sprue, the sprue is set to a “2” shape bend at 1/3 of the top to bottom, and three ingates are designed, as shown in Figure 1, to reduce the impact of sand casting and make the sprue full as soon as possible.
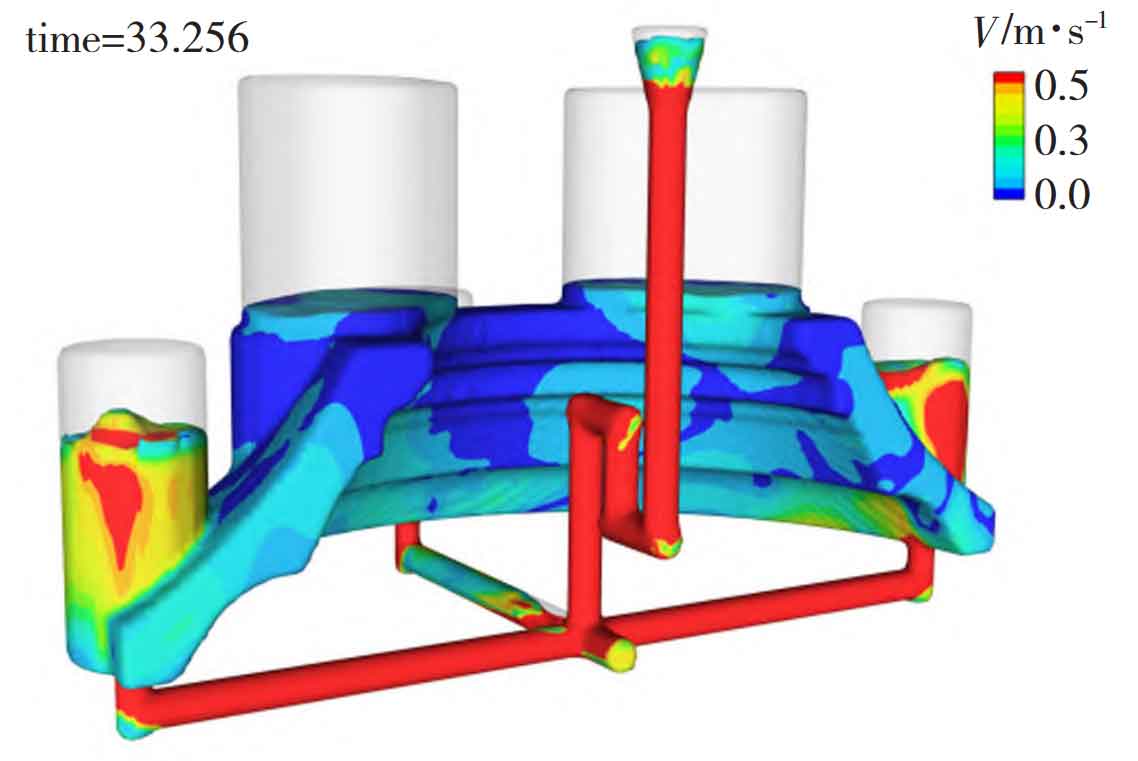
The simulation after modifying the sprue shows that the optimization of the sprue is effective, but the middle ingate is still not full at 33s, indicating that the design of the three ingates is unreasonable. The main reason is that the metal liquid does not flow at the ideal constant speed and flow rate.
2.Optimize the sprue again
Two 90 ° turns are set at the sprue, and two inner gates are designed, as shown in Figure 2. The simulation shows that the sand casting gating system is fully filled in about 5s.
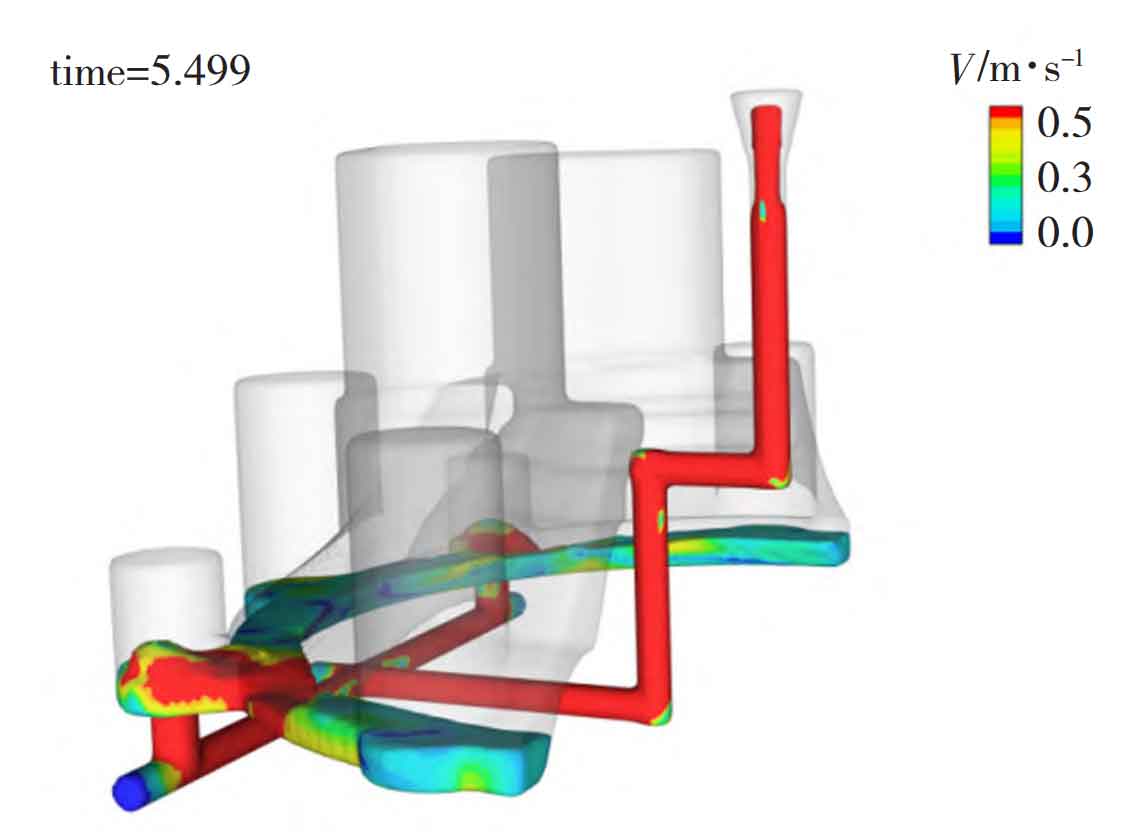
From the simulation results, it can be seen that two ingates are set, and the gating system proportion of sand casting is F internal: F horizontal: F vertical=2 ∶ 2 ∶ 1; The inner gate area shall ensure that the liquid metal flow rate at the inner gate is not greater than 0.5 m/s From the simulation results of mold filling, it can be seen that during the rising process of liquid level, there is no phenomenon of steel night splash and vortex, which greatly reduces the oxidation degree of steel night, indicating that the design of sand casting gating system is basically reasonable.
3.Analysis of simulated entrainment results
The simulation results of entrainment after the improvement of the sand casting gating system show that the sand casting gating system will be filled as soon as possible after the optimization of the sand casting gating system. From the filling results of 35s (Fig. 3) and 50s (Fig. 4), it can be seen that the entrainment is significantly reduced. The modified gating system of sand mold casting is helpful to reduce the porosity defect of castings.