With the introduction of a large number of social cars, the demand for this kind of consumption parts of the brake disc is also increasing. The brake disc is a very important part of the brake system, which is related to personal safety, so the internal quality of the brake disc is extremely strict. In particular, the working surface of the brake disc is not allowed to have shrinkage porosity defects, otherwise the stability of the brake system will be affected, noise will be generated during operation, and there will be jitter.
The brake disc casting process is sand casting. Steel, iron and most non-ferrous alloy castings can be obtained by sand casting. Because the molding materials used in sand casting are cheap and easy to obtain, and the mold manufacturing is simple, it can adapt to the single production, batch production and mass production of castings. For a long time, it has been the basic process in casting production. However, in sand casting, there will be typical frequent casting defects such as porosity and porosity, which will be a challenge for the brake disc, a casting with high quality requirements [1-3]. At present, the simulation calculation of casting process has become an effective means to solve casting defects, which is widely used in casting process optimization.
Based on the characteristics of the continuous casting brake disc production line of the enterprise, this paper uses the casting simulation calculation method to analyze the parts and causes of the defects in the casting, form the optimized process suitable for the continuous casting brake disc casting, give full play to the advantages of the continuous casting brake disc production line, and meet the requirements of high quality and efficiency of the enterprise.
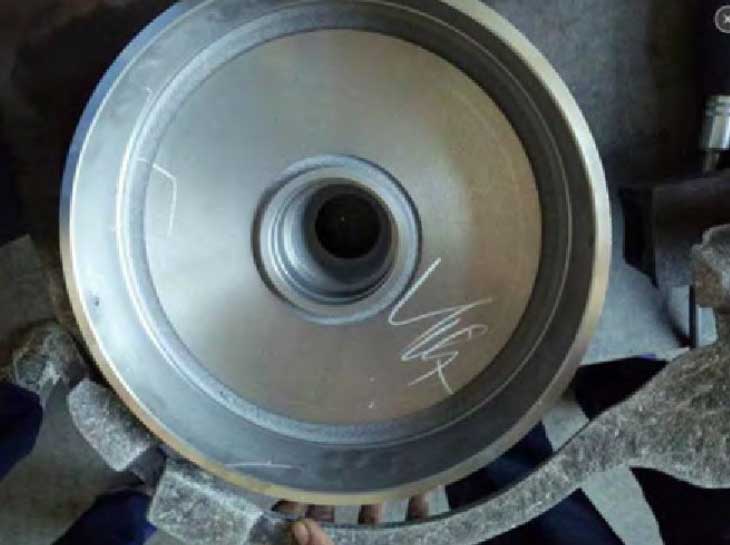
In conclusion, the ProCAST software can be used to simulate the casting pouring process, which can directly observe the filling stability, the sequence of solidification process, and the temperature change of the casting, and realize the prediction of the location of shrinkage cavity and porosity. The conclusions are as follows:
(1) Compared with the simulation results, the main reason for the defects in the working face of the brake disc is the air entrainment during the pouring process;
(2) Through the optimization design of the original pouring system, the defects in the working face are solved. The test results show that the optimization process can meet the product quality requirements.