The coated sand casting process is a national promoted technology project, which has significant energy-saving, material saving, reduced production costs, and improved product quality. It has been widely used in the production of castings in industries such as automobiles, motorcycles, and construction machinery, and has achieved good economic and social benefits. ZHY Casting hopes to apply the coated sand casting process to more exported casting products by introducing the coated sand casting process test of the front suspension connection frame castings for export. Our company uses the coated sand casting process to produce export castings. After years of verification, this process has been fully mature; The coated sand casting technology produces products with a surface roughness of Ra6.3-3.2um and a dimensional accuracy of CT6-9 level. The casting surface is smooth, beautiful, and has high accuracy. Its characteristics include:
(1) Coated sand is a mixture of powdered resin and molding sand, which is finer and has stronger adhesion than oil sand. It is not easy to sand off, and the casting contour is clear, the surface is smooth, and the size is accurate.
(2) The laminating sand process can save a large amount of resin sand; The sand iron ratio of castings is 1.3:1 to 1; The utilization rate of sand is high; The production environment and working conditions have been greatly improved.
(3) The temperature, chemical composition, internal structure, and mechanical properties of molten iron melted in a medium frequency induction furnace are relatively stable.
1. Technical requirements and indicators for castings
The casting of the export front suspension connection frame is a safety connector on heavy-duty vehicles; The material is QT450-10; The contour size of the casting blank is 720 × 490 × 340mm, with a main wall thickness of 6mm. The quality of the casting blank is 63 kg, with high dimensional accuracy requirements and a dimensional accuracy error of 0.50mm; The surface roughness is required to be between 6.3 and 12.5 μ M; There must be no defects such as pores, sand inclusions, shrinkage, porosity, cold insulation, wrinkling, etc. inside. The casting of the export front suspension connection frame has high requirements in the following aspects:; 1. Surface quality of castings; 2. Dimensional accuracy; 3. Material.
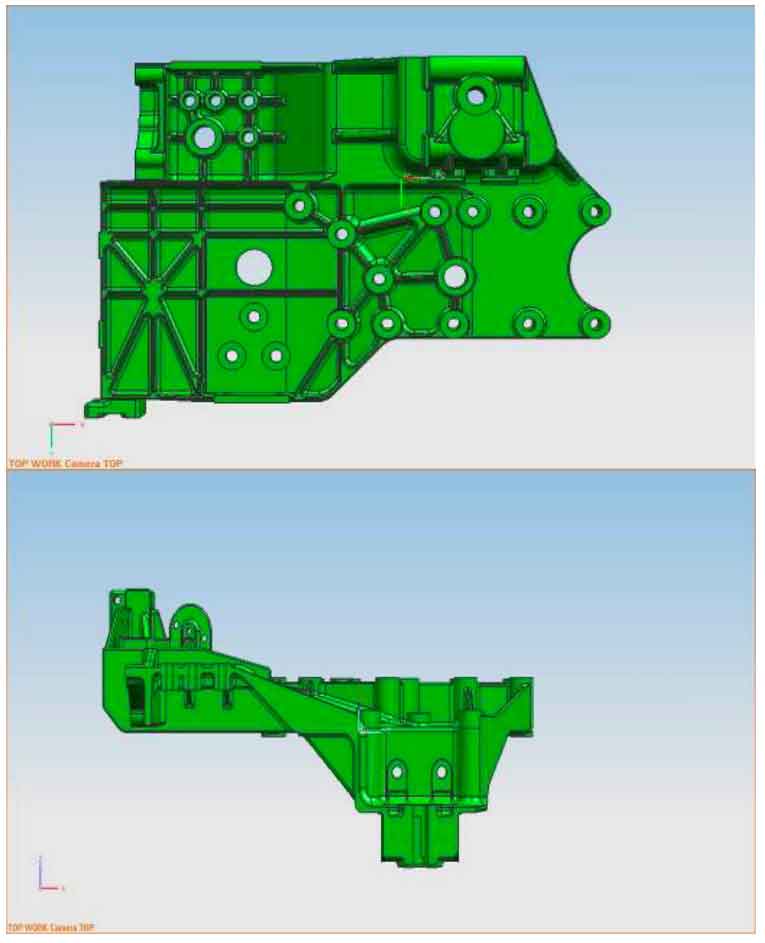
2. Coating sand casting process and fixture design
The coated sand casting process is to cover a certain thickness of coated sand layer on the inner cavity of the formed metal mold to form the shell of the mold. After repeated process experiments and production verification, the thickness of the coated sand layer was reasonably matched to complete the filling, solidification, and cooling processes of the casting under ideal conditions, eliminating most of the factors that cause casting defects; At the same time, it also creates better cooling conditions for the solidification of castings, greatly improving the surface and internal quality of castings. Due to the fact that the coated sand layer is thinner than that of ordinary resin sand casting, high-quality coated sand can be used as the sand for casting, ensuring the dimensional accuracy, surface roughness, and mold strength of the castings.
2.1 Design of Coating Sand Casting Process
The wall thickness of the export front suspension connection frame casting is uneven, and when designing the coating sand casting process, special consideration should be given to the solidification method of the casting – balanced solidification. The design scheme of the coated sand casting process is one type per piece, with horizontal parting and horizontal pouring, and the important surface of the casting is placed in the lower mold; To ensure the dimensional accuracy of castings, all cavity sand cores are equipped with built-in sand cores. The pouring system adopts a semi enclosed structure, with a cross-sectional ratio of F straight: F horizontal: F inner=1.2; 1.6:1 and cast without a riser. In the design of the pouring system, a larger cross-sectional area of the runner is selected to allow the slag inclusions in the molten iron to have sufficient upward floating height, which plays a good role in blocking slag and can also meet the necessary liquid shrinkage needs of the casting; The pouring position of the inner gate is at the thin-walled part of the casting, and the thickest part of the casting wall is far from the inner gate to ensure simultaneous solidification of the casting, and necessary cold iron is placed in the thicker parts of the casting; Fully ensure simultaneous solidification of castings. After the molten iron enters the mold, it cannot directly flush the core and cause turbulence. In addition, due to the relatively large size of the castings and the thin wall thickness, the cooling effect of the molten iron is significant. The length of the inner runner should be as short as possible to prevent defects such as wrinkles and cold shuts on the surface of ductile iron castings caused by the cooling of the molten iron.
2.2 Fixture Design
The technical and quality requirements for the export front suspension connection frame casting are relatively high; The production difficulty is high, and the sand used for the casting process of coated sand is thermosetting phenolic resin coated sand. The design of the coated sand casting fixture mainly includes metal molds, molding plates, and sand shooting devices. Control the preheating temperature of the metal mold at 220-250 ℃; The size of the export front suspension connection frame casting is relatively large, with a casting quality of 63 kg; The heat storage capacity of the metal mold is low, and in the design of the molding plate, it is particularly important to heat the heating capacity of the template to ensure the instant solidification of the coated sand. In addition, the high precision requirement of the casting makes the selection of casting scale crucial in mold design. Based on the obstruction of casting solidification, we choose different scales for different parts, with a scale of 0.9 to 1.2 to%. The metal mold material is HT200, and the deformation of the metal mold is less during mass production; The built-in core of the casting has a certain height. The metal mold production adopts a combination type, which not only ensures the process requirements but also reduces the manufacturing cost of the metal mold. To ensure the quality of the sand coating during the film sand molding and smooth exhaust during casting, special attention is paid to the design of the exhaust system in the design of the metal mold and mold plate. The metal mold and mold plate adopt a combined exhaust method of gap exhaust, exhaust groove exhaust, and air needle exhaust. The closure of the sandblasting hole adopts a stacking method, which is very convenient for production and maintenance.
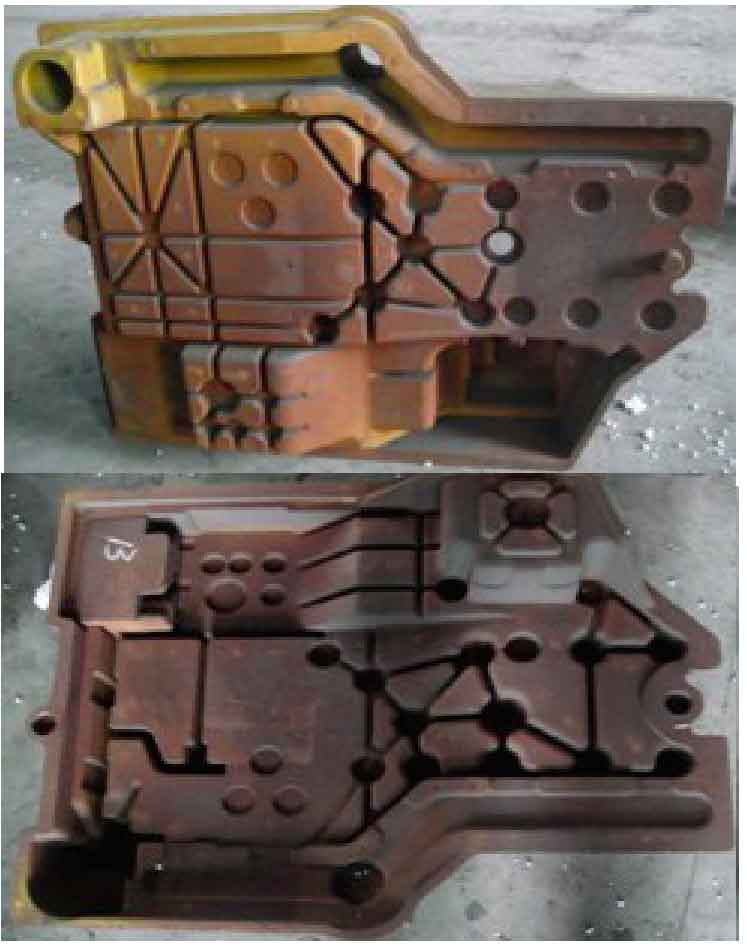
3. Production trial production
Two single station core shooting machines (with a one-time sand shooting volume of 40 kg) were selected for the trial production of export front suspension connection frame castings; Prepare upper and lower coated sand shells separately; High production efficiency. At the same time, the technical requirements for workers in production are relatively low.
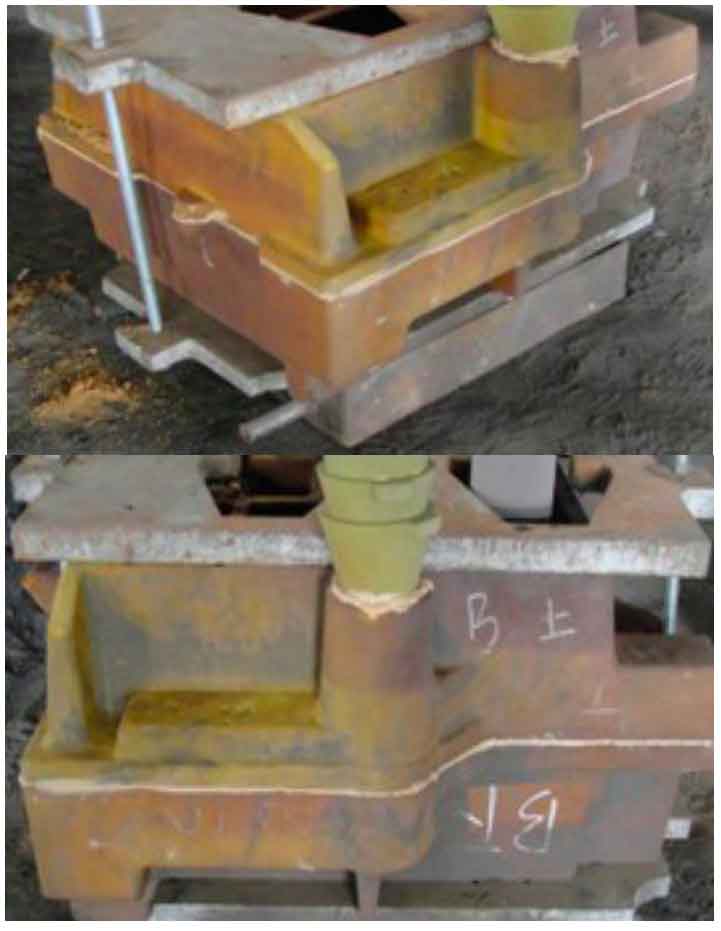
To ensure the surface quality of the castings, finer grained coated sand (50/100 mesh) is selected. The performance of the coated sand is: gas generation rate: ≥ 15ml/g; Resin content: 2-2.5%. The melting equipment is a 1.0t medium frequency induction furnace. Jigang pig iron is selected as the pig iron, QRMg8RE3 is used as the spheroidizing agent, and 75 silicon iron is used as the inoculant. The casting is a ferrite matrix casting with a large contour size and thin wall thickness. In order to prevent the occurrence of carbides in the casting, a higher tapping temperature of 1530-1550 ℃ should be adopted for the iron spheroidization and inoculation treatment of the casting, and the pouring temperature should be controlled between 1360-1390 ℃; A lower silicon content in the molten iron is achieved through multiple pregnancies. The chemical composition of the casting is C: 3.8-3.95%; Si: 2.7-2.9%; Mn: ≤ 0.3%; P ≤ 0.06%; S < 0.02%; M g: 0.03-0 05%; Re: 0.02-0.045%. The yield rate of castings is about 80%, and the scrap rate of castings is 4 ≤%. Compared with the resin sand casting process, it saves about 35% of production costs and has significant economic benefits. The appearance, internal quality, and dimensional accuracy of the castings meet the export requirements.
4. Summary
Through the production practice of coated sand casting technology for export front suspension connecting frame castings, thin-walled large contours, high precision, and high-quality export castings are produced. The coated sand casting technology has strong technical and economic advantages; It can significantly improve the internal and external quality of exported castings, reduce the production cost of coated sand casting process, and further enhance the comprehensive competitiveness of enterprises in producing exported castings.