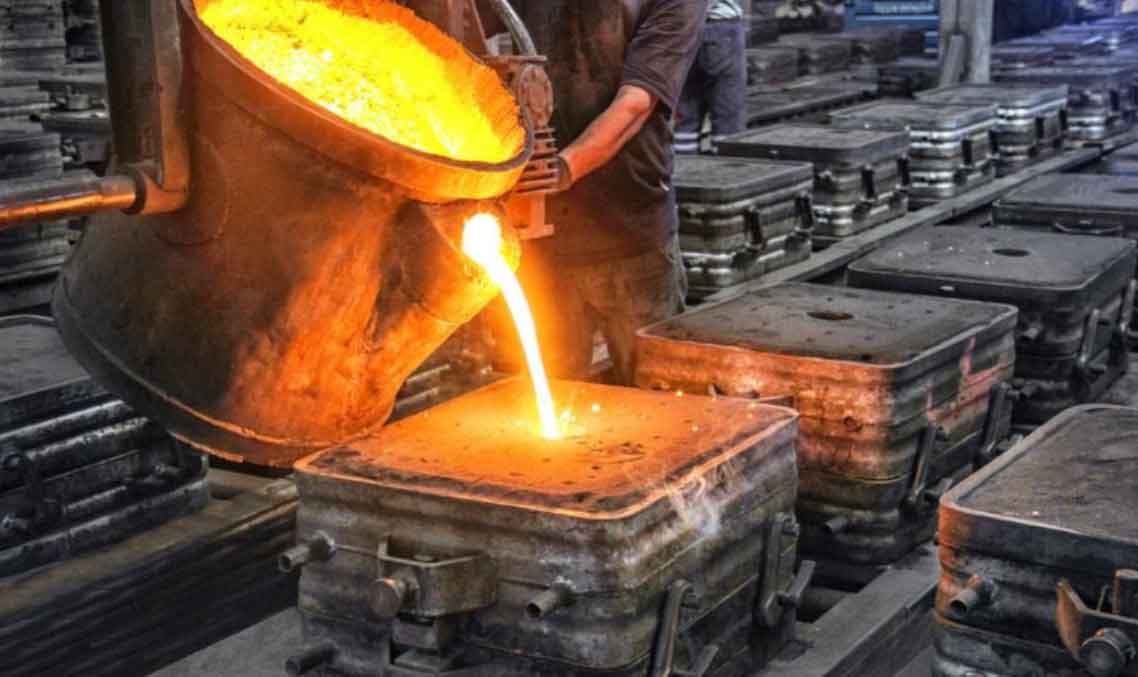
As the sand casting manufacturing industry continues to evolve, several emerging materials and techniques are pushing the boundaries of what can be achieved with this traditional casting method. These innovations are aimed at enhancing casting performance, expanding design possibilities, and improving sustainability. Here are some of the notable emerging materials and techniques in sand casting manufacturing:
1. Advanced Alloys:
- Sand casting manufacturers are increasingly working with advanced alloys, including high-strength aluminum alloys, nickel-based superalloys, and titanium alloys. These materials offer superior mechanical properties, corrosion resistance, and temperature resistance, making them suitable for demanding applications in aerospace, automotive, and other industries.
2. Hybrid Casting Techniques:
- Manufacturers are exploring hybrid casting techniques that combine sand casting with other casting methods like investment casting or die casting. This approach allows for more complex geometries and can reduce the need for extensive machining.
3. Additive Manufacturing for Patterns:
- The use of additive manufacturing (3D printing) for pattern production is gaining traction in sand casting. 3D-printed patterns offer greater design flexibility, rapid prototyping, and reduced lead times for pattern development.
4. Eco-Friendly Binders and Additives:
- Manufacturers are adopting eco-friendly binders and additives in sand casting to reduce emissions and improve sustainability. Water-based binders and organic additives are examples of greener alternatives to traditional resins.
5. Computational Modeling and Simulation:
- Advanced computational modeling and simulation tools are becoming integral to the sand casting process. Casting simulation software helps optimize gating and riser designs, predict defects, and improve casting quality.
6. Lightweight and Metal Matrix Composites:
- Sand casting is being used to produce lightweight metal matrix composites (MMCs) that combine high-strength reinforcement materials (e.g., carbon fibers) with metal matrices. MMCs offer excellent strength-to-weight ratios, making them attractive for aerospace and automotive applications.
7. Ceramic Sand Molds:
- Manufacturers are experimenting with ceramic-based sand molds, which can withstand higher temperatures and offer improved dimensional accuracy compared to traditional sand molds.
8. Vacuum Assisted Casting:
- Vacuum-assisted casting is a technique where vacuum pressure is applied during the casting process to improve the filling of intricate mold cavities and reduce porosity in the castings.
9. Microcasting and Nanocasting:
- Microcasting and nanocasting techniques involve producing tiny and intricate castings on a micro or nanoscale. These techniques find applications in microelectromechanical systems (MEMS), biomedical devices, and electronics.
10. Low Pressure Sand Casting:
- Low-pressure sand casting is a method that involves applying low-pressure gas to the molten metal in the mold. This results in improved metal density, reduced porosity, and enhanced casting integrity.
As sand casting manufacturers embrace these emerging materials and techniques, they unlock new opportunities for creating complex components, improving performance, and reducing environmental impact. These advancements enable the sand casting industry to remain competitive and relevant in the face of evolving market demands and technological innovations.