Quality control is a critical aspect of the casting process to ensure that casting parts meet the required performance and reliability standards. Here are key considerations for effective quality control in casting parts:
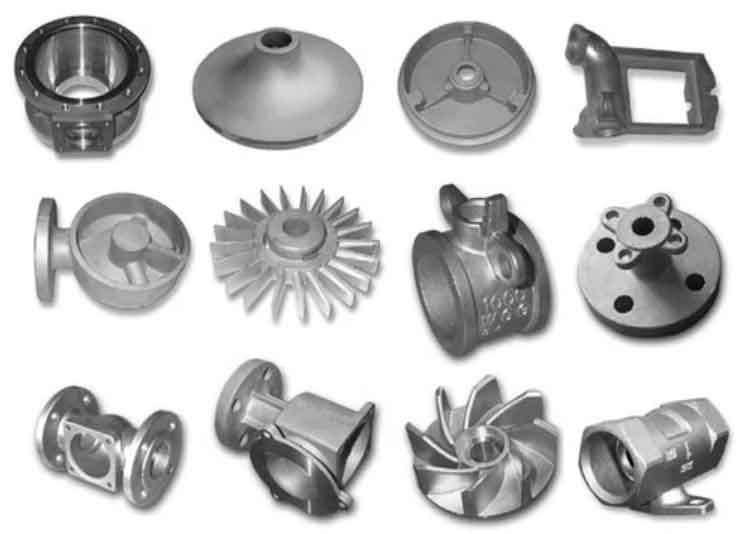
- Design for Manufacturability (DFM): The casting design should be optimized for manufacturability, taking into account factors such as material selection, mold design, gating system, and part geometry. DFM principles help minimize potential defects and improve the overall quality of the casting.
- Material Inspection: Raw materials used in casting, such as alloys and sand, should undergo thorough inspection to ensure they meet the required specifications. This includes checking chemical composition, mechanical properties, and adherence to relevant industry standards.
- Mold and Core Inspection: The molds and cores used in the casting process should be inspected for dimensional accuracy, surface finish, and integrity. This includes checking for any defects or damage that may affect the final product.
- Process Monitoring: Real-time monitoring of critical process parameters, such as temperature, pressure, and cooling rates, is essential to ensure consistency and repeatability in the casting process. This helps identify any deviations or abnormalities that may affect the quality of the casting parts.
- Non-Destructive Testing (NDT): NDT techniques, such as visual inspection, ultrasonic testing, radiographic testing, and magnetic particle inspection, are employed to detect internal and surface defects in casting parts without causing damage. NDT helps identify discontinuities, porosity, cracks, and other defects that may compromise the integrity of the parts.
- Dimensional Inspection: Accurate dimensional inspection is crucial to verify that casting parts meet the required tolerances and specifications. This can be done through techniques such as coordinate measuring machines (CMM), optical measurement systems, and digital scanning. The use of 3D metrology tools allows for precise measurement and comparison against the intended design.
- Mechanical Testing: Mechanical testing, such as tensile testing, hardness testing, impact testing, and fatigue testing, is performed to evaluate the mechanical properties and performance of casting parts. This ensures that the parts can withstand the expected loads and environmental conditions.
- Surface Finish Inspection: The surface finish of casting parts is inspected for any imperfections, such as burrs, roughness, or unwanted features. This is important for aesthetic purposes, as well as to ensure proper functionality and compatibility with mating components.
- Documentation and Traceability: Comprehensive documentation and traceability throughout the casting process are essential for quality control. This includes maintaining records of material certifications, inspection reports, process parameters, and any corrective actions taken. Traceability ensures accountability and facilitates identification of any issues that may arise during or after production.
- Continuous Improvement: Implementing a culture of continuous improvement helps identify areas for enhancement and optimization in the casting process. Regular analysis of quality control data, customer feedback, and internal audits can lead to process refinements and quality enhancements over time.
Effective quality control measures, combined with adherence to industry standards and best practices, ensure that casting parts meet the required specifications, performance criteria, and reliability expectations. By implementing robust quality control processes, manufacturers can deliver high-quality casting parts that meet customer requirements and contribute to the overall success of the product or system they are a part of.