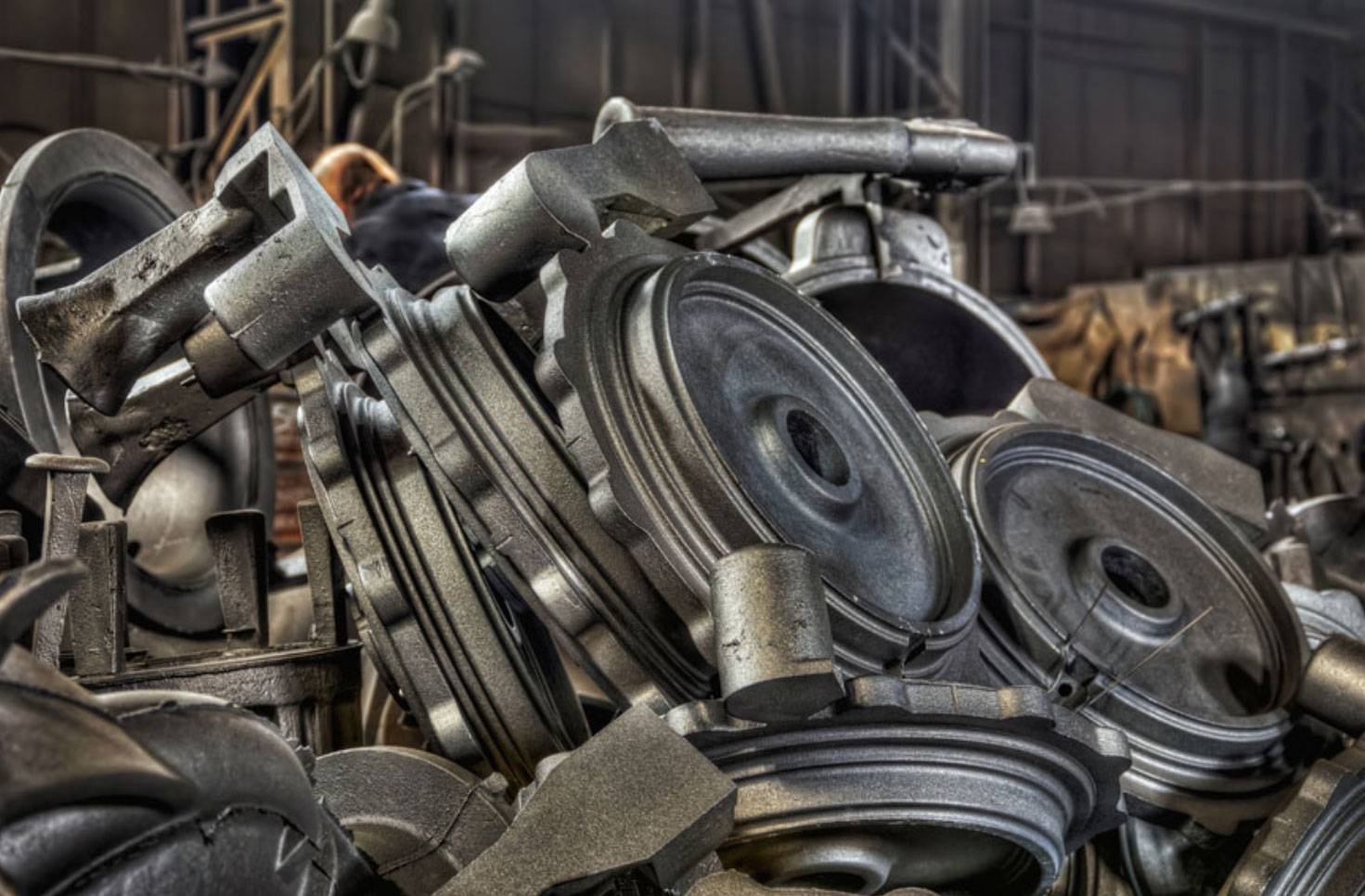
Quality control in ductile iron casting is pivotal for ensuring that the final products meet the required specifications and perform reliably in their intended applications. Optimizing the process for superior results involves several key strategies and technologies. Here’s an overview:
1. Raw Material Quality Assurance
- Material Selection: Using high-quality raw materials, including iron and alloying elements.
- Regular Testing: Conducting chemical composition analysis to ensure the raw materials meet specified standards.
2. Process Control and Monitoring
- Melting Control: Precise control of melting temperatures and times to ensure uniformity and desired chemical composition.
- Mold Quality: Ensuring the molds are of high quality and free from defects that could affect the casting.
- Real-Time Monitoring: Utilizing sensors and control systems to monitor critical process parameters in real time.
3. Nodulization and Inoculation Optimization
- Nodulization Control: Accurate addition and distribution of nodulizing agents (like magnesium) to produce the desired spheroidal graphite structure.
- Inoculant Effectiveness: Regularly testing the effectiveness of inoculants and adjusting their composition and quantity for optimal results.
4. Casting Techniques and Cooling Rates
- Pouring Techniques: Controlled pouring to reduce turbulence and minimize the inclusion of impurities or formation of defects.
- Cooling Control: Managing the cooling rates to influence the microstructure and mechanical properties of the cast iron.
5. Post-Casting Operations
- Heat Treatment: Applying appropriate heat treatment processes to achieve desired mechanical properties.
- Machining and Finishing: Ensuring precision in machining and finishing operations for dimensional accuracy and surface quality.
6. Non-Destructive Testing (NDT)
- X-Ray Inspection: For detecting internal defects such as voids or inclusions.
- Ultrasonic Testing: To assess the integrity and homogeneity of the castings.
- Magnetic Particle Inspection: For detecting surface and near-surface defects.
7. Destructive Testing
- Tensile and Hardness Tests: To measure mechanical properties like strength, ductility, and hardness.
- Microstructure Analysis: Examining the microstructure to verify proper graphite shape and matrix distribution.
8. Statistical Process Control (SPC)
- Data Analysis: Using SPC tools to analyze data from manufacturing processes for trend identification and process optimization.
- Continuous Improvement: Implementing a continuous improvement mindset, using data-driven approaches to refine processes.
9. Compliance with Standards
- International Standards: Adhering to international standards such as ASTM, ISO, or specific industry standards.
- Certifications: Obtaining and maintaining relevant certifications like ISO 9001 for quality management systems.
10. Training and Skills Development
- Employee Training: Regular training of personnel on the latest casting techniques and quality control methods.
- Skill Development: Encouraging a culture of skill development and knowledge sharing among the workforce.
11. Supplier Quality Management
- Vendor Audits: Conducting regular audits of suppliers to ensure they meet quality standards.
- Collaborative Approach: Working closely with suppliers to address quality issues and improve material quality.
12. Customer Feedback Integration
- Feedback Analysis: Regularly collecting and analyzing customer feedback for insights into product performance and areas for improvement.
- Responsive Action: Quickly addressing any issues identified through customer feedback.
Implementing and continuously improving these quality control measures ensures that ductile iron cast products meet the highest standards of quality and reliability, thus maintaining customer satisfaction and trust.