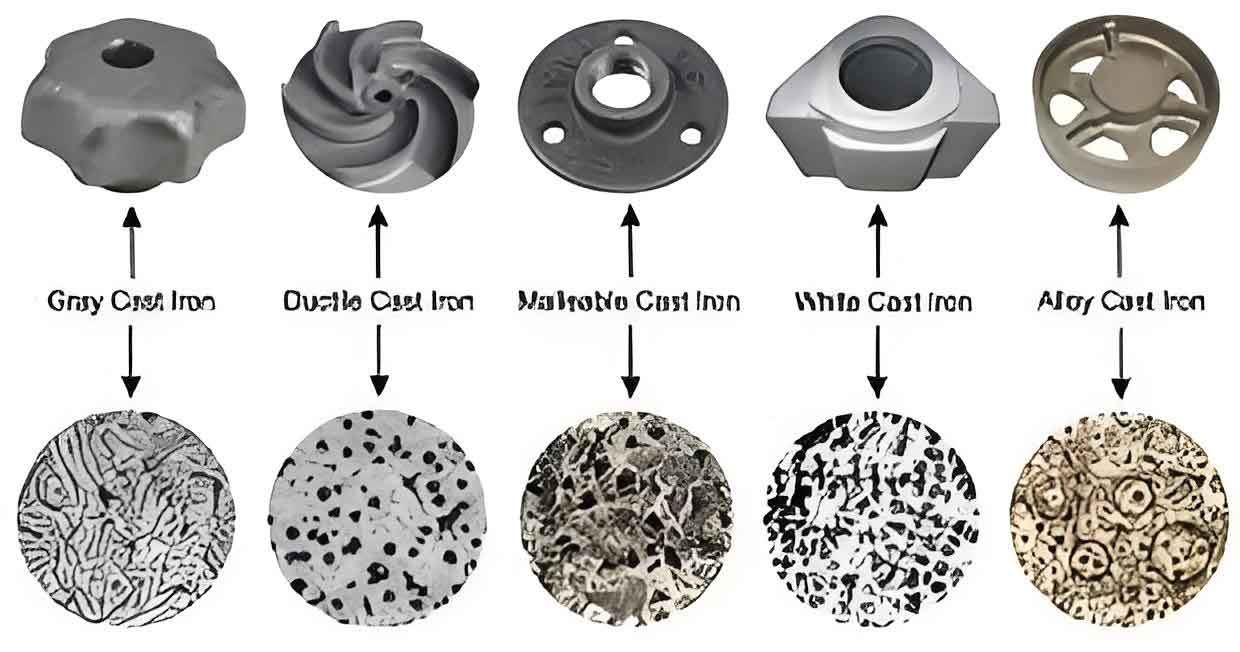
Alloying elements play a crucial role in modifying the properties of cast irons. By adding certain elements in specific quantities, the mechanical, physical, and chemical properties of cast irons can be significantly enhanced. Here’s an overview of how various alloying elements influence the properties of gray, white, ductile, and malleable cast irons.
1. Gray Cast Iron
- Silicon (Si):
- Increases fluidity and graphite formation, improving machinability.
- Typically present in amounts of 1-3%.
- Manganese (Mn):
- Combines with sulfur to form manganese sulfide, reducing the formation of iron sulfide which can cause brittleness.
- Enhances strength and hardness.
- Usually added in the range of 0.5-1%.
- Nickel (Ni):
- Improves toughness, strength, and corrosion resistance.
- Often used in alloyed gray irons for better performance.
- Chromium (Cr):
- Enhances hardness and wear resistance.
- Small amounts (0.5-1%) are added for improved performance in high-stress applications.
- Copper (Cu):
- Increases strength and hardness without significantly reducing ductility.
- Typically added in the range of 0.5-1.5%.
2. White Cast Iron
- Chromium (Cr):
- Significantly improves hardness and wear resistance.
- Amounts range from 1-28%, depending on the application.
- Nickel (Ni):
- Enhances toughness and impact resistance.
- Often added in conjunction with chromium for balanced properties.
- Manganese (Mn):
- Increases hardness and wear resistance.
- Amounts typically range from 0.5-1.5%.
- Molybdenum (Mo):
- Improves strength and toughness at high temperatures.
- Commonly added in small amounts (0.2-1%).
3. Ductile Cast Iron
- Magnesium (Mg):
- Essential for the formation of nodular (spheroidal) graphite.
- Added in small amounts (0.03-0.05%).
- Silicon (Si):
- Promotes the formation of nodular graphite and increases strength.
- Typically present in amounts of 2-3%.
- Nickel (Ni):
- Enhances toughness, strength, and corrosion resistance.
- Commonly used in amounts of 0.5-2%.
- Copper (Cu):
- Increases strength and hardness without significantly affecting ductility.
- Usually added in the range of 0.5-1.5%.
- Chromium (Cr):
- Increases hardness and wear resistance.
- Small amounts (0.5-1%) are added for specific applications.
- Molybdenum (Mo):
- Enhances high-temperature strength and wear resistance.
- Typically added in small amounts (0.2-0.5%).
4. Malleable Cast Iron
- Silicon (Si):
- Promotes the formation of temper carbon.
- Typically present in amounts of 1-1.8%.
- Nickel (Ni):
- Improves toughness, strength, and corrosion resistance.
- Often used in alloyed malleable irons for enhanced properties.
- Copper (Cu):
- Increases strength and hardness without significantly affecting ductility.
- Usually added in the range of 0.5-1.5%.
- Manganese (Mn):
- Combines with sulfur to form manganese sulfide, reducing brittleness.
- Enhances strength and hardness.
- Typically present in amounts of 0.5-1%.
Summary of Alloying Elements and Their Effects
Alloying Element | Gray Cast Iron | White Cast Iron | Ductile Cast Iron | Malleable Cast Iron |
---|---|---|---|---|
Silicon (Si) | Enhances fluidity and machinability | – | Promotes nodular graphite formation | Promotes temper carbon formation |
Manganese (Mn) | Reduces brittleness, enhances strength and hardness | Increases hardness and wear resistance | Increases hardness and wear resistance | Reduces brittleness, enhances strength and hardness |
Nickel (Ni) | Improves toughness, strength, and corrosion resistance | Enhances toughness and impact resistance | Improves toughness, strength, and corrosion resistance | Improves toughness, strength, and corrosion resistance |
Chromium (Cr) | Enhances hardness and wear resistance | Significantly improves hardness and wear resistance | Increases hardness and wear resistance | – |
Copper (Cu) | Increases strength and hardness | – | Increases strength and hardness | Increases strength and hardness |
Magnesium (Mg) | – | – | Essential for nodular graphite formation | – |
Molybdenum (Mo) | – | Improves high-temperature strength and toughness | Enhances high-temperature strength and wear resistance | – |
Alloying elements are carefully selected and added to cast irons to tailor their properties for specific applications, ensuring optimal performance in terms of strength, hardness, ductility, and wear resistance.