Chapter 1: Dimensional Accuracy of Sand Casting Parts
The importance of dimensional accuracy in sand casting parts. Dimensional accuracy is a critical factor in the successful production of sand castings. Here’s a bit more information to help you understand this topic:
- Design Tolerances: Design drawings typically include specified dimensions and tolerances for each feature of the sand casting part. Tolerances define the allowable variation from the nominal dimension. These tolerances account for the inherent variations that can occur during the casting process.
- Measuring Dimensional Accuracy: To evaluate the dimensional accuracy of sand casting parts, measurements are taken using precision tools such as calipers, micrometers, coordinate measuring machines (CMM), and optical measurement systems. These measurements are then compared to the specified dimensions on the design drawings.
- Shrinkage and Contraction: During the cooling and solidification of molten metal within the mold, the material undergoes shrinkage and contraction. This can lead to slight dimensional changes in the final casting. Foundries take this into account when designing the mold and pattern.
- Pattern and Mold Design: The design of the pattern (the replica of the final part) and the mold (the cavity into which the molten metal is poured) affects the dimensional accuracy. Proper consideration of factors like pattern allowances and mold materials helps control the final dimensions.
- Mold Shift and Distortion: Handling and transport of molds, as well as the cooling and solidification of the metal, can introduce shifts and distortions that impact dimensional accuracy. Proper handling and cooling processes are crucial to minimize these effects.
- Casting Process Parameters: Variables such as pouring temperature, cooling rate, and the type of metal being cast can influence dimensional accuracy. Precise control of these variables helps achieve the desired dimensions.
- Post-Casting Processes: Machining and finishing processes might be required to achieve the final dimensions and surface finish. These processes should be carefully planned to avoid over-removal of material, which could compromise the part’s integrity.
- Quality Control: Quality control measures, including regular inspections and audits, ensure that the cast parts meet the required dimensional accuracy. Statistical methods like process capability analysis can help monitor and improve the casting process.
- Non-Destructive Testing (NDT): In some cases, non-destructive testing techniques such as laser scanning or 3D imaging are used to verify the dimensional accuracy of complex or critical parts.
- Documentation and Communication: Clear communication between the design team, foundry, and quality control personnel is crucial to ensure that everyone understands the required dimensions and tolerances. Documentation of measurements and any deviations is essential for traceability and continuous improvement.
Overall, achieving the desired dimensional accuracy in sand casting parts requires a combination of meticulous design, precise manufacturing processes, effective quality control, and collaboration between different teams involved in the production process.
Chapter 2: Appearance Quality of Sand Casting Parts
The appearance quality of sand casting parts is crucial for their overall functionality and aesthetics. Let’s break down the important factors you mentioned:
- Surface Flatness: This refers to the degree to which the surface of the casting is even and uniform. Irregularities in surface flatness can lead to problems during assembly or when the part needs to fit with other components. It can also affect the overall stability and performance of the final product.
- Surface Finish: Surface finish pertains to the texture or smoothness of the casting’s surface. Achieving the desired surface finish involves controlling factors such as the type of sand used, molding techniques, and post-casting treatments. A smooth surface finish not only enhances the part’s visual appeal but also affects its functionality and how it interacts with other components.
- Defects (Pores, Inclusions, Cracks, etc.): Defects like pores (tiny voids), inclusions (foreign materials trapped in the casting), and cracks can severely compromise the structural integrity of the sand casting. These defects can lead to weakened parts that are prone to failure under stress or over time. Ensuring that the casting process is properly controlled and monitored helps in minimizing these defects.
- Visual Appearance: The overall visual appearance of the sand casting part is important for both functional and aesthetic reasons. If the part is intended to be visible in the final product, any defects or rough surfaces can give an unprofessional or low-quality impression to customers or end-users.
To achieve high-quality sand casting parts, several steps can be taken:
- Proper Design: Ensuring that the part’s design is suitable for the sand casting process can help minimize the risk of defects and ensure a smoother finish. Rounded edges, gradual transitions, and appropriate draft angles are some considerations.
- Meticulous Molding and Pouring: The molding process needs to be carefully controlled to avoid introducing defects. The quality of the mold material and the pouring technique play significant roles.
- Metal Quality: The quality of the metal being used for casting is crucial. Proper melting and alloying processes should be followed to reduce the chances of inclusions and other impurities.
- Heat Treatment: Depending on the application, heat treatment processes can be applied to reduce internal stresses, improve mechanical properties, and enhance surface finish.
- Quality Control and Inspection: Regular inspection during and after the casting process is essential. This can involve visual inspection, non-destructive testing (e.g., X-rays, ultrasonic testing), and dimensional checks.
- Post-Casting Finishing: Sometimes, additional processes like grinding, polishing, or coating might be necessary to achieve the desired surface finish.
By taking these factors into consideration and maintaining strict quality control measures throughout the sand casting process, manufacturers can produce sand casting parts that not only meet functional requirements but also exhibit excellent appearance quality.
Chapter 3: Material Properties of Sand Casting Parts
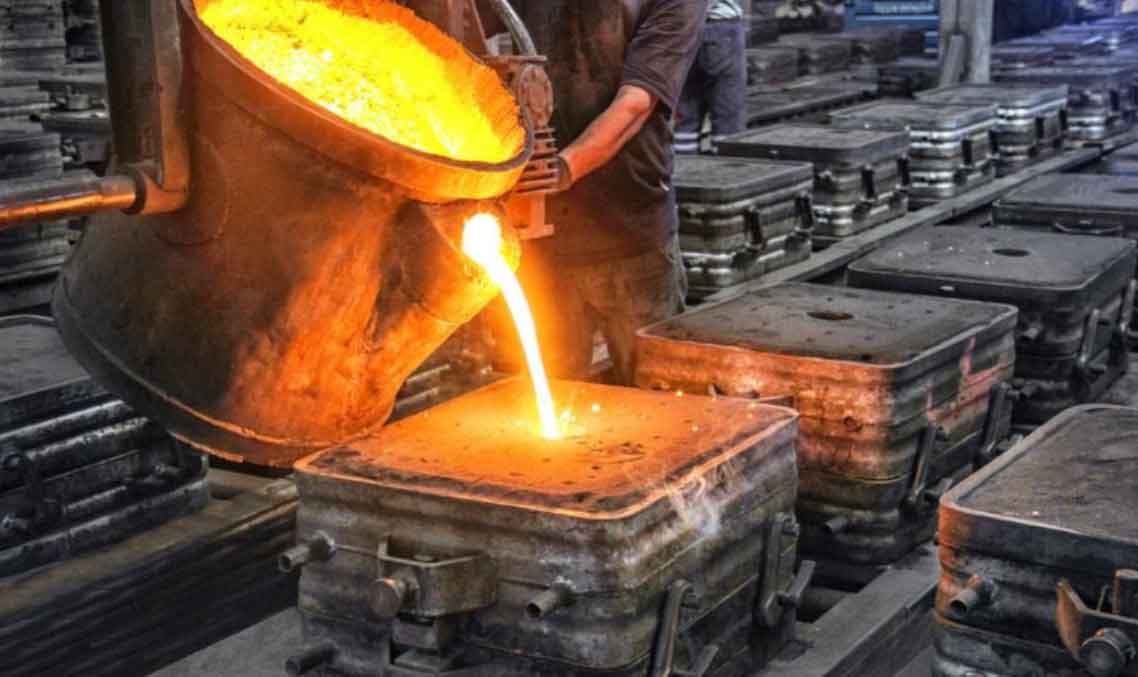
Conducting material testing on sand casting parts is crucial to ensure their quality and suitability for their intended applications. Here’s some more information on the tests you mentioned:
- Metallographic Analysis: Metallography involves studying the microstructure of a material under a microscope. For sand casting parts, it helps to assess factors like grain size, porosity, inclusion content, and the overall distribution of phases within the material. This analysis is particularly important in identifying defects like porosity or inclusions that might weaken the part.
- Hardness Testing: Hardness testing measures the resistance of a material to indentation or deformation. It provides insights into the material’s strength and wear resistance. Different types of hardness tests, like Brinell, Rockwell, or Vickers, can be performed based on the specific requirements and the geometry of the part. Hardness testing can help identify variations in material properties that might affect the part’s performance.
- Tensile Testing: Tensile testing assesses a material’s mechanical properties under tension. A sample of the material is subjected to gradually increasing tensile forces until it eventually breaks. This test provides important information like the material’s yield strength, ultimate tensile strength, elongation, and modulus of elasticity. Tensile testing helps determine if the material meets required mechanical specifications and whether it will perform reliably under different loads.
- Impact Testing: Impact testing evaluates a material’s ability to absorb energy under high rates of loading. This is especially important for parts that might experience sudden impacts or dynamic loading conditions. The Charpy or Izod test is commonly used to measure the impact toughness of a material.
- Chemical Analysis: A chemical analysis is often conducted to verify that the composition of the material conforms to the specified requirements. This ensures that the desired material properties are achieved and consistent.
- Non-Destructive Testing (NDT): Techniques like X-ray, ultrasonic, or dye penetrant testing can be used to detect internal defects or irregularities without damaging the part.
Unqualified material properties, such as inadequate strength, poor ductility, or high levels of porosity, can indeed lead to various problems during the use of sand casting parts. These issues might include premature failure, reduced lifespan, or compromised safety. To prevent such problems, manufacturers rely on rigorous testing procedures to ensure that the materials used in sand casting meet the necessary standards and specifications.
Chapter 4: Internal Quality of Sand Casting Parts
Cross-sectional inspection is a common method used to evaluate the internal quality of sand casting parts or any type of metal components. This process involves cutting a sample from the casting, preparing it for microscopy, and then examining it under a metallographic microscope to assess the internal structure and identify any defects.
Here’s a more detailed breakdown of the process:
- Sample Preparation: A portion of the sand casting part is cut, typically using a cutting machine or saw, to create a cross-sectional sample. The sample should be representative of the part’s overall structure and geometry.
- Mounting: The cut sample is embedded in a resin or epoxy material to create a block that can be easily handled and polished. This helps in maintaining the integrity of the sample during subsequent steps.
- Grinding and Polishing: The mounted sample is ground and polished to achieve a smooth, flat surface. This step removes any surface irregularities, scratches, or deformities introduced during cutting and mounting. Proper polishing is essential to ensure accurate microscopic observations.
- Etching: The polished sample may undergo chemical etching to reveal the microstructure more clearly. Etching involves applying a chemical solution that selectively reacts with the different phases of the metal, making the internal structures more visible under a microscope.
- Microscopic Examination: The prepared and etched sample is observed under a metallographic microscope. This type of microscope is specifically designed for examining the microstructure of materials at high magnification. It allows you to see the arrangement of grains, presence of defects (like inclusions, porosity, cracks), and the overall quality of the casting.
- Analysis and Interpretation: The microstructure observed under the microscope can provide insights into the casting process and any potential defects or irregularities. This information can be used to evaluate the material’s properties, the effectiveness of the casting process, and the overall quality of the part.
- Documentation: The observations and findings are usually documented, including photographs taken through the microscope. These records serve as valuable references for quality control, process improvement, and troubleshooting.
Cross-sectional inspection is crucial for ensuring the integrity and quality of critical components, especially those that are subject to high loads, pressure, or other demanding conditions. By analyzing the internal microstructure, you can identify potential weaknesses or defects that might not be apparent from external visual inspection alone.
Chapter 5: Acoustic Testing of Sand Casting Parts

Acoustic testing methods, including ultrasonic testing, are commonly used in the manufacturing and quality control of sand casting parts, especially for large or complex components. Ultrasonic testing is a non-destructive testing technique that uses high-frequency sound waves to detect internal defects such as voids, pores, cracks, and other imperfections within the material.
Here’s how ultrasonic testing generally works for sand casting parts:
- Principle: Ultrasonic waves are introduced into the material being tested. These waves travel through the material until they encounter a boundary between different materials or a defect within the material. When the waves encounter such a boundary or defect, some of the energy is reflected back to the transducer, which converts it into an electrical signal.
- Transducer: A transducer is used to generate ultrasonic waves and also to receive the reflected waves. It’s a crucial component of the testing setup.
- Coupling Medium: To ensure proper transmission of the ultrasonic waves between the transducer and the part being tested, a coupling medium is often used. This medium helps eliminate air gaps and provides a good acoustic interface.
- Defect Detection: The time taken for the ultrasonic waves to travel through the material and back to the transducer is measured. Any delay or change in the time of flight indicates the presence of a defect or a boundary within the material.
- Analysis: The received signals are analyzed to determine the size, location, and nature of defects within the material. Skilled technicians or specialized software interpret the data to make informed decisions about the part’s quality.
- Advantages: Ultrasonic testing is non-destructive, meaning it doesn’t damage the part being tested. It can detect both surface and subsurface defects, making it suitable for finding internal defects like pores, voids, and cracks in sand casting parts.
- Limitations: The accuracy of ultrasonic testing can be affected by factors such as the size and shape of the part, the type of material being tested, the orientation of defects, and the expertise of the operator. Additionally, access to all areas of the part can be challenging, especially in complex geometries.
Ultrasonic testing is just one of the many techniques available for inspecting sand casting parts. Other methods like radiographic testing, dye penetrant testing, magnetic particle testing, and visual inspection are also used depending on the nature of the part and the specific requirements of the application. The choice of testing method often depends on factors like the size of the part, the material being used, the type of defects expected, and the level of sensitivity needed for the inspection.
Chapter 6: Chemical Composition of Sand Casting Parts
Analyzing the chemical composition of sand casting parts is crucial to ensure that they meet the design requirements and possess the desired mechanical properties. The composition can vary based on the specific material being used, but I’ll provide you with a general overview of the steps involved in conducting a chemical composition analysis for sand casting parts.
- Sample Preparation: Obtain a representative sample from the sand casting part. This sample should be taken from a location that accurately represents the entire part’s composition.
- Material Identification: Identify the material that the sand casting part is made of. Common materials used in sand casting include various types of metals and alloys, such as aluminum, iron, steel, brass, bronze, etc.
- Laboratory Analysis: Take the prepared sample to a laboratory equipped with spectroscopy or other analytical equipment suitable for chemical composition analysis. There are several methods you can use:a. Spectroscopy: Optical emission spectroscopy (OES) or inductively coupled plasma (ICP) spectroscopy can be used to analyze the composition of metals and alloys. These methods use the characteristic wavelengths of emitted light or plasma to identify and quantify elements present in the sample.b. X-ray Fluorescence (XRF): XRF is a non-destructive method that analyzes the fluorescent X-rays emitted by a material when exposed to high-energy X-rays. It can provide information about the elemental composition of the material.c. Energy Dispersive X-ray Spectroscopy (EDS): EDS is often used in conjunction with scanning electron microscopy (SEM). It provides information about the elemental composition of small areas on the sample’s surface.
- Data Interpretation: After the analysis is performed, you will receive a report that outlines the elemental composition of the sand casting part. Compare the results with the design requirements and specifications to ensure they meet the desired composition.
- Verification and Adjustments: If the composition is not within the acceptable range, further adjustments can be made to the casting process, or the alloy composition can be modified to achieve the desired properties. This might involve adding specific alloying elements or adjusting the ratios of existing elements.
Remember that the specific procedures and methods can vary based on the material being analyzed and the available equipment. It’s essential to follow established testing standards and guidelines to ensure accurate and reliable results. If you’re not experienced in performing these analyses, it’s recommended to involve professionals or experts who have the necessary expertise and equipment.
Chapter 7: Functional Testing of Sand Casting Parts
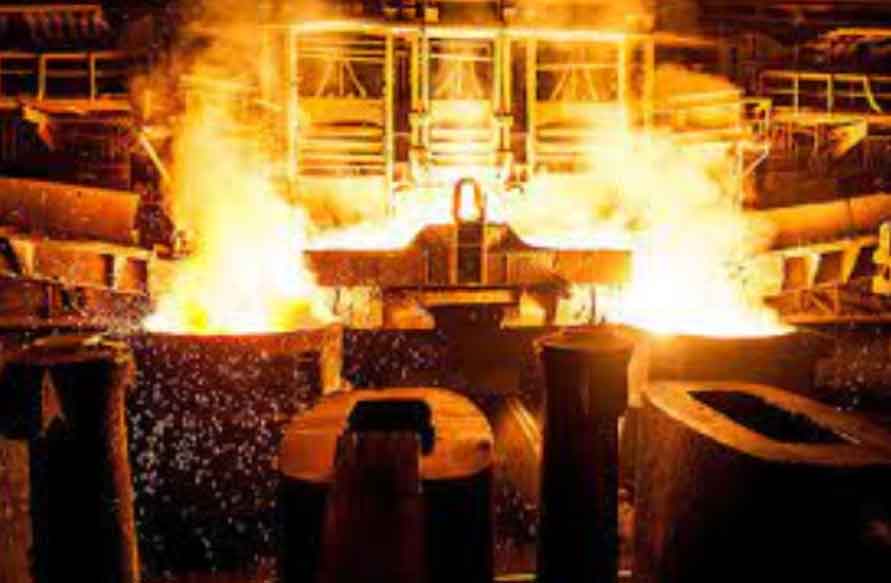
Functional testing of sand casting parts is a crucial step in the manufacturing process to ensure that the cast parts perform as intended in their specific applications. Sand casting is a common method for producing metal parts and components, but variations in the casting process, material properties, and other factors can affect the final product’s functionality. Here are some key considerations for conducting functional testing of sand casting parts:
1. Defining Functional Requirements: Before conducting any testing, it’s important to clearly define the functional requirements of the part. This involves understanding how the part will be used, the stresses and loads it will experience, and any specific performance criteria it must meet.
2. Non-Destructive Testing (NDT): Non-destructive testing methods, such as X-ray, ultrasonic testing, and dye penetrant testing, can be used to identify internal defects, cracks, voids, and other issues that might not be visible on the surface. NDT helps ensure that the part’s internal structure is sound.
3. Dimensional Inspection: The dimensions of the sand casting part must match the specifications outlined in the design. This includes measurements of critical features, tolerances, and overall part geometry. Coordinate measuring machines (CMMs) and other precision measurement tools can be used for this purpose.
4. Mechanical Testing: Mechanical tests assess the mechanical properties of the casting, including tensile strength, hardness, impact resistance, and fatigue resistance. These tests help determine whether the part can withstand the expected loads and stresses during its operational life.
5. Functional Performance Testing: This type of testing involves subjecting the sand casting part to conditions that mimic its real-world operating environment. For example, if the part is meant to be used in a high-temperature environment, it should be tested under similar temperatures to ensure it retains its structural integrity.
6. Fit and Assembly Testing: If the casting part needs to be assembled with other components, fit and assembly testing ensures that the part integrates seamlessly and correctly with the rest of the assembly. This includes checking for proper mating, alignment, and clearance.
7. Corrosion and Wear Testing: Depending on the application, the part might be exposed to corrosive substances or wear over time. Testing for corrosion resistance and wear resistance can be essential to ensure the part’s longevity.
8. Environmental Testing: Environmental conditions, such as humidity, temperature variations, and exposure to chemicals, can impact the performance of the sand casting part. Testing under these conditions can identify any potential weaknesses or vulnerabilities.
9. Lifecycle Testing: This involves subjecting the part to a series of simulated usage cycles to assess its durability and reliability over time. This type of testing helps predict how the part will perform throughout its expected lifespan.
10. Failure Analysis: In case a functional test reveals issues or failures, thorough analysis should be conducted to understand the root causes. This information can help improve the casting process and prevent similar issues in the future.
11. Documentation: Comprehensive documentation of all testing processes, results, and any issues discovered is essential for traceability and quality control purposes.
Functional testing of sand casting parts is essential to ensure their proper performance in real-world applications. The specific tests conducted will vary depending on the part’s intended use and the requirements it must meet. By conducting thorough functional testing, manufacturers can identify and address potential problems, ensure consistent quality, and deliver reliable products to their customers.
Chapter 8: Wear and Corrosion Resistance of Sand Casting Parts
The wear and corrosion resistance of sand casting parts is crucial, especially for components that will be exposed to harsh environments. Wear and corrosion can significantly affect the performance and lifespan of such parts. Here’s an overview of how these tests are conducted and their importance:
- Wear Resistance Testing: Wear resistance testing involves simulating the conditions under which the part will experience friction, abrasion, or erosion. Some common methods to assess wear resistance include:
- Abrasion Testing: Abrasion tests involve subjecting the part to abrasive materials under controlled conditions. Taber Abrasion Test and ASTM G65 are examples of standardized tests for abrasion resistance.
- Sliding Wear Testing: Sliding wear tests simulate the movement between two surfaces in contact. Pin-on-Disk and Block-on-Ring tests are commonly used to measure sliding wear resistance.
- Impact Wear Testing: For components subjected to impact wear, impact testing machines can be employed. Charpy and Izod tests are often used to evaluate the impact resistance of materials.
- Corrosion Resistance Testing: Corrosion resistance testing evaluates a part’s ability to withstand chemical reactions with its environment. Different methods are used based on the type of corrosion the part is expected to face:
- Salt Spray Test (ASTM B117): This test simulates a corrosive coastal environment by exposing the part to a salt mist. It’s useful for assessing the general corrosion resistance of materials.
- Potentiostatic and Galvanostatic Tests: These electrochemical methods evaluate the corrosion behavior of metals by measuring their polarization curves, corrosion potential, and corrosion current density.
- Crevice Corrosion and Pitting Tests: These tests focus on localized corrosion. ASTM G48 is commonly used to evaluate crevice corrosion, while ASTM G150 assesses pitting corrosion resistance.
- Importance of Testing: Evaluating wear and corrosion resistance is essential for several reasons:
- Performance Reliability: Parts operating in harsh environments need to maintain their functionality over time. Testing ensures that they won’t fail prematurely due to wear or corrosion.
- Cost Savings: Identifying suitable materials through testing can help avoid expensive failures and replacements, saving time and resources in the long run.
- Safety: Components that degrade due to wear or corrosion can pose safety risks, especially in critical applications like aerospace or automotive sectors.
- Regulatory Compliance: Certain industries require parts to meet specific wear and corrosion resistance standards for regulatory reasons.
Remember that the choice of testing method and conditions should closely mimic the real-world environment the parts will face. Additionally, material selection, design modifications, and protective coatings can be influenced by the results of these tests to enhance wear and corrosion resistance.