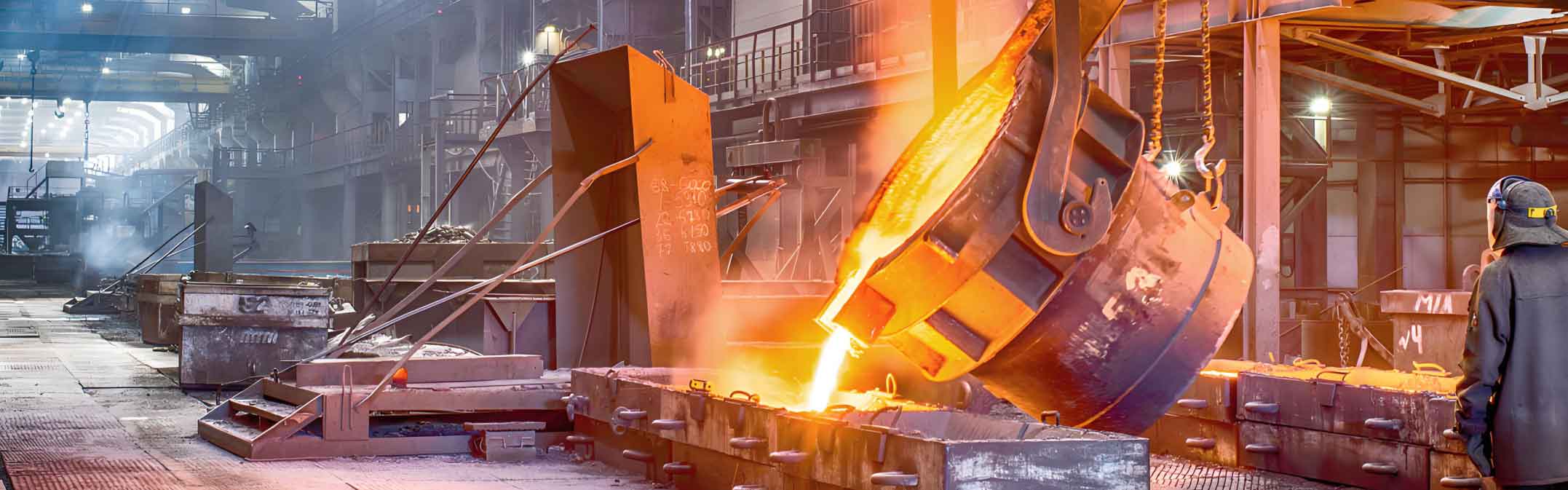
Introduction
Quality control is a critical aspect of sand casting, ensuring that the final products meet specified standards and requirements. Effective quality control practices help minimize defects, reduce waste, and improve overall process efficiency. This article delves into the essential components of quality control in sand casting, the methodologies used, and the benefits of maintaining high-quality standards in the production process.
Overview of Sand Casting
Sand casting involves creating a mold from a mixture of sand and a binding agent, into which molten metal is poured to form the desired shape. The fundamental steps in the sand casting process include:
- Pattern Making: Creating a pattern that resembles the final product.
- Mold Making: Placing the pattern in a flask and packing it with sand to form a mold.
- Core Making: Producing cores for hollow sections within the casting.
- Pouring: Pouring molten metal into the mold cavity.
- Cooling and Shakeout: Allowing the metal to solidify before breaking the mold to retrieve the casting.
- Finishing: Cleaning and finishing the casting to achieve the desired specifications.
Importance of Quality Control in Sand Casting
Quality control in sand casting is crucial for several reasons:
- Consistency: Ensures consistent quality across all castings.
- Defect Reduction: Identifies and mitigates potential defects.
- Customer Satisfaction: Produces parts that meet or exceed customer expectations.
- Cost Efficiency: Reduces waste and rework, leading to cost savings.
- Regulatory Compliance: Ensures products meet industry standards and regulations.
Key Components of Quality Control
1. Material Quality Control
Ensuring the quality of materials used in sand casting is fundamental. This includes:
- Sand Quality: Selecting high-purity sand with uniform grain size.
- Binder Quality: Using appropriate binders to achieve the desired mold strength and permeability.
- Metal Quality: Using high-quality metals free from impurities and contaminants.
2. Process Control
Maintaining control over the casting process is essential for producing high-quality parts. Key aspects include:
- Temperature Control: Monitoring and controlling the temperature of molten metal to prevent defects.
- Pouring Technique: Ensuring proper pouring speed and technique to avoid turbulence and air entrapment.
- Cooling Rate: Controlling the cooling rate to prevent thermal stresses and cracking.
3. Mold and Core Quality
The quality of molds and cores significantly impacts the final casting quality. Ensuring proper mold and core design and manufacturing includes:
- Dimensional Accuracy: Ensuring molds and cores are made to precise dimensions.
- Surface Finish: Achieving a smooth surface finish to reduce post-casting finishing work.
- Strength and Permeability: Balancing mold strength and permeability to prevent defects.
4. Inspection and Testing
Regular inspection and testing throughout the casting process help identify and address potential issues early. Techniques include:
- Visual Inspection: Checking for surface defects and irregularities.
- Dimensional Inspection: Using tools such as calipers and coordinate measuring machines (CMM) to verify dimensions.
- Non-Destructive Testing (NDT): Methods like X-ray, ultrasonic, and dye penetrant testing to detect internal and surface defects.
Common Defects in Sand Casting and Their Causes
Defect | Description | Causes |
---|---|---|
Porosity | Small voids or holes in the casting | Trapped gases, improper venting |
Shrinkage | Cavities or depressions | Metal contraction during solidification |
Inclusions | Foreign materials embedded in casting | Contaminated sand, poor melt cleanliness |
Cracks | Fractures in the casting | Thermal stresses, improper cooling |
Misruns | Incomplete filling of mold cavity | Low pouring temperature, insufficient fluidity |
Methods for Quality Control in Sand Casting
1. Statistical Process Control (SPC)
SPC involves using statistical methods to monitor and control the casting process. This includes:
- Control Charts: Monitoring key process parameters to detect variations.
- Process Capability Analysis: Assessing the ability of the process to produce within specified limits.
2. Six Sigma
Six Sigma methodologies aim to reduce defects and improve process efficiency. This involves:
- DMAIC Framework: Define, Measure, Analyze, Improve, Control to systematically improve processes.
- Root Cause Analysis: Identifying and addressing the root causes of defects.
3. Lean Manufacturing
Lean manufacturing focuses on eliminating waste and optimizing efficiency. Key principles include:
- Value Stream Mapping: Identifying and eliminating non-value-added activities.
- Continuous Improvement (Kaizen): Encouraging small, incremental improvements.
4. Advanced Inspection Techniques
Utilizing advanced inspection techniques helps ensure high-quality castings. Examples include:
- 3D Scanning: Capturing detailed geometries of castings for comparison with digital models.
- Computed Tomography (CT) Scanning: Providing detailed internal images to detect defects.
Implementing a Quality Control System
Steps to Implement a Quality Control System:
- Define Quality Standards: Establish clear quality standards and specifications for castings.
- Develop SOPs: Create standard operating procedures for each step of the casting process.
- Training and Education: Train employees on quality control practices and the importance of quality.
- Inspection Protocols: Develop inspection protocols and schedules for regular quality checks.
- Continuous Monitoring: Continuously monitor process parameters and product quality.
- Feedback Loop: Implement a feedback loop for continuous improvement based on inspection results.
Tools and Technologies for Quality Control
- Control Charts: Used in SPC to monitor process stability.
- Coordinate Measuring Machines (CMM): For precise dimensional inspection.
- X-ray and Ultrasonic Testing: Non-destructive testing methods for defect detection.
- 3D Scanners: For detailed inspection and comparison with CAD models.
Benefits of Effective Quality Control
Advantages:
- Higher Product Quality: Consistent and defect-free castings.
- Cost Savings: Reduced waste, rework, and scrap rates.
- Improved Customer Satisfaction: Reliable products that meet customer specifications.
- Regulatory Compliance: Adherence to industry standards and regulations.
- Enhanced Reputation: Building a reputation for quality and reliability in the market.
Challenges in Quality Control
While quality control in sand casting offers numerous benefits, it also presents certain challenges:
- Initial Costs: Implementing advanced quality control systems and training can be costly.
- Complexity: Managing and integrating various quality control processes can be complex.
- Resistance to Change: Employees may resist changes to established processes and practices.
- Continuous Improvement: Maintaining a culture of continuous improvement requires ongoing effort and commitment.
Conclusion
Quality control in sand casting is essential for producing high-quality, reliable castings that meet industry standards and customer expectations. By implementing robust quality control practices, manufacturers can reduce defects, improve yield, and achieve cost savings. Advanced inspection techniques, process control methods, and a commitment to continuous improvement are key to maintaining high-quality standards in sand casting. Embracing these strategies will ultimately lead to better products, increased customer satisfaction, and a stronger market reputation.
Future Trends
The future of quality control in sand casting will likely involve increased use of artificial intelligence and machine learning for predictive analytics and defect detection. Additionally, advancements in materials science will enable the development of new sand and binder formulations that further enhance quality. Sustainability will also play a crucial role, with a focus on eco-friendly processes and materials to minimize environmental impact.