This article focuses on the research of investment casting process of K648 superalloy castings with a hollow wax mold structure. It begins with an introduction to the importance of investment casting in various fields and the significance of achieving high dimensional accuracy. The factors affecting the dimensional accuracy of investment castings, such as wax pattern types, molding processes, mold manufacturing precision, and wax pattern structure, are analyzed in detail. Through experimental research on a specific K648 high-temperature alloy casting, the design and implementation of a hollow wax pattern structure are described. The experimental results show that the hollow wax pattern structure can effectively reduce the linear shrinkage rate of the wax pattern and improve the dimensional accuracy of the casting. This research provides a valuable reference for the investment casting process design of high-precision and thick-large castings.
1. Introduction
Investment casting is a crucial manufacturing process widely used in industries such as aerospace, aviation, and gas turbines for producing core components. The dimensional accuracy of castings is of utmost importance in these applications. High-temperature alloy castings often employ medium-temperature wax materials and all-silica sol shell processes, with the achievable dimensional accuracy typically ranging from CT4 to CT7 levels. The dimensional accuracy of investment castings is significantly influenced by multiple factors, and understanding and controlling these factors is essential for improving casting quality.
2. Factors Affecting the Dimensional Accuracy of Investment Castings
2.1 Wax Pattern Types
Both non-filled and filled wax materials are commonly used for medium and high-end investment castings. Non-filled wax materials generally have a linear shrinkage rate of about 1%, while filled wax materials have a rate of about 0.5%. In this study, a 162-brand non-filled wax material was used, which has a linear shrinkage rate of 0.9% – 1.0% and exhibits good formability, stable shrinkage, and suitable flexibility for manufacturing wax patterns of thin-walled and small to medium-sized parts.
Wax Pattern Type | Linear Shrinkage Rate | Characteristics |
---|---|---|
Non-filled Wax Material | 0.9% – 1.0% | Good formability, stable shrinkage, suitable flexibility for thin-walled and small to medium-sized parts |
Filled Wax Material | About 0.5% | – |
2.2 Molding Processes
Parameters such as wax injection temperature, injection pressure, wax flow rate, cooling time, and mold temperature significantly affect the linear shrinkage rate of the wax pattern and, consequently, the dimensional accuracy of the casting. Higher wax injection temperature, injection pressure, and faster wax flow rate, along with shorter cooling time and higher mold temperature, tend to increase the linear shrinkage rate and deteriorate the casting dimensional accuracy. However, with the advancement of wax injection equipment manufacturing capabilities and the application of big data intelligent management systems, these process parameters can be effectively controlled to reduce their impact on the dimensional accuracy of the wax pattern.
Molding Process Parameter | Impact on Linear Shrinkage Rate | Impact on Dimensional Accuracy |
---|---|---|
Wax Injection Temperature (Higher) | Increases | Deteriorates |
Injection Pressure (Higher) | Increases | Deteriorates |
Wax Flow Rate (Faster) | Increases | Deteriorates |
Cooling Time (Shorter) | Increases | Deteriorates |
Mold Temperature (Higher) | Increases | Deteriorates |
2.3 Mold Manufacturing Precision
The development of mechanical processing technology has led to significant improvements in mold manufacturing precision. With the emergence of ultra-precision machining techniques and the application of intelligent manufacturing and network technologies, along with advancements in optical and electronic technologies, the precision of mold manufacturing has reached a high level. This has reduced the impact of mold manufacturing precision on the dimensional accuracy of the wax pattern.
2.4 Wax Pattern Structure
When the thickness of the wax pattern section exceeds 13 mm, it is recommended to use cold wax blocks to reduce the wall thickness and, thereby, the linear shrinkage rate. However, this approach has several drawbacks, including increased mold costs, reduced production efficiency, uneven shrinkage, and potential quality issues. Therefore, a more reasonable approach is to design a hollow wax pattern structure to achieve a more uniform wall thickness and reduce the linear shrinkage rate without sacrificing production efficiency.
3. Experimental Materials and Methods
3.1 Wax Pattern Structure Analysis
A K648 high-temperature alloy casting was selected for the experiment. The chemical composition of the alloy includes 0.05 C, 34Cr, 3Mo, 0.85 Ti, 4.45 W, 0.98 Nb, 1.0 Al, and the balance Ni. The casting has a typical structural investment casting design, with a “C”-shaped blind hole structure and key 部位壁厚均超过了 13 mm. The traditional wax pattern structure for this casting is prone to problems such as heat dissipation difficulties, bending deformation, and large linear shrinkage due to the thick wall thickness.
3.2 Wax Pattern Structure Design
Considering the issues with the cold wax block solution, a hollow wax pattern structure was designed. The hollow section wall thickness was set to 4.5 – 5.0 mm to ensure effective collection of linear shrinkage rate data and sufficient room temperature strength of the wax pattern. In locations where core pulling is difficult and an equal wall thickness structure is not feasible, a tapered hollow structure was adopted. The open ends of all hollow structures were placed on the gate surface and closed during wax pattern assembly to form a hollow internal structure.
3.3 Mold Preparation
Based on the known linear shrinkage rates of the wax material from the mold to the wax pattern and from the wax pattern to the casting, the comprehensive shrinkage rate of the mold cavity for the experimental casting was preliminarily set to 2.6%. Metal molds were prepared for both the solid and hollow wax pattern structures. The surface offset and distal bending of the solid and hollow wax patterns were measured and compared.
3.4 Wax Pattern Preparation
100% new 162 medium-temperature wax material was used, and a 16 t double-station hydraulic wax injection machine was employed to prepare the wax patterns. After removal from the metal mold, the wax patterns were placed on a shaping platform and shaped with weights for more than 2 h to reduce deformation.
3.5 Shell Making
An all-silica sol shell was produced according to a specific process, and the wax was removed using a high-temperature steam dewaxing kettle to obtain the experimental shell.
3.6 Casting Pouring and Post-treatment
The experimental shell was preheated in a box-type resistance roasting furnace, and the K648 alloy ingot was remelted in a 25 kg three-chamber vacuum induction electric furnace for pouring. After pouring, the casting underwent cooling, shell removal, removal of the pouring system, heat treatment, and sandblasting to obtain the final casting.
4. Experimental Results and Analysis
4.1 Wax Pattern Contour Dimension Analysis
The two types of wax patterns (solid and hollow) were scanned using a Geomagic Control blue light scanner and compared with the 3D theoretical model. The results showed that the average wall thickness reduction of the hollow wax pattern decreased the heat accumulated during the wax pattern pressing process, reducing the internal stress generated during cooling shrinkage. Additionally, the increased contact area between the wax pattern and the metal mold led to more stable and uniform cooling. As a result, the deformation of the distal bending part and the plane core shrinkage of the hollow wax pattern were effectively alleviated, which is of great significance for improving the dimensional accuracy of the wax pattern.
4.2 Wax Pattern Linear Dimension Analysis
The key dimensions of the two types of wax patterns were measured, and the actual linear shrinkage rates were calculated. The results indicated that the average linear shrinkage rate of the solid wax pattern was 1.16%, while that of the hollow wax pattern was 0.54%. The linear shrinkage rates of all key dimensions of the hollow wax pattern were smaller than those of the solid wax pattern. In particular, for dimensions with larger shrinkage distances during the cooling process, the reduction in the linear shrinkage rate was more pronounced. For dimensions where the original wax pattern wall thickness was less than the minimum hollow design wall thickness of 4.5 mm, the change in the linear shrinkage rate was relatively small due to lower heat and smaller cooling shrinkage stress.
4.3 Casting Dimension Analysis
According to HB 6103, the casting dimension detection results were analyzed. The casting prepared with the solid wax pattern had a dimensional accuracy of CT7 level, with an average linear shrinkage rate of 2.70%. In contrast, the casting prepared with the hollow wax pattern had a dimensional accuracy of CT5 level, with an average linear shrinkage rate of 2.41%. The solid wax pattern had larger shrinkage differences in different positions during the cooling process, resulting in larger casting dimension fluctuations. The hollow design of the wax pattern reduced the wall thickness and shrinkage differences, and the hollow parts were supported by metal cores, resulting in smaller dimension fluctuations of the wax pattern and the casting.
5. Conclusions
5.1 Wax Pattern Improvement
By locally hollowing out the cross-section of the solid wax pattern with a thickness of 4.5 – 5.0 mm and shaping the wax pattern for more than 2 h, the center shrinkage of the larger plane and the distal bending of the wax pattern can be alleviated. The overall linear shrinkage rate of the wax pattern decreased from 1.16% to 0.54%.
5.2 Casting Dimensional Accuracy Enhancement
The dimensional accuracy of the investment casting was improved from CT7 level to CT5 level, and the actual linear shrinkage rate of the casting decreased from 2.70% to 2.41%. This research provides…
6.1 Significance of the Research
The research on the hollow wax mold structure for K648 superalloy castings has several important implications. Firstly, it addresses a crucial problem in the investment casting industry – achieving high dimensional accuracy for thick and large castings. By reducing the linear shrinkage rate of the wax mold, the study has demonstrated a significant improvement in the dimensional accuracy of the final casting, which is essential for applications in aerospace, gas turbines, and other high-tech fields where precise component dimensions are critical.
Secondly, the proposed hollow structure design provides an alternative to traditional methods such as using cold wax blocks. It overcomes many of the limitations associated with cold wax blocks, including increased costs, reduced production efficiency, and potential quality issues. This new design allows for more efficient production without sacrificing the quality of the casting.
Finally, the research contributes to a better understanding of the factors influencing the dimensional accuracy of investment castings. It highlights the importance of wax mold structure and provides a practical example of how a carefully designed structure can lead to improved casting quality. This knowledge can be applied to other casting materials and geometries, facilitating further advancements in the investment casting process.
6.2 Future Research Directions
While the current research has achieved promising results, there are several areas for future exploration. One potential direction is to further optimize the hollow structure design. This could involve investigating different geometries and dimensions of the hollow sections to achieve even better dimensional accuracy and mechanical properties of the casting. For example, researchers could explore the use of more complex hollow shapes or vary the thickness of the hollow walls in different regions of the wax mold to better control the shrinkage behavior.
Another area of interest is the application of the hollow wax mold structure to other alloy systems. Different alloys have different thermal and mechanical properties, and it would be valuable to study how the hollow structure affects the casting quality of other high-temperature alloys or even non-ferrous alloys. This could expand the applicability of the technology and open up new possibilities for the production of high-quality castings in various industries.
In addition, the integration of advanced manufacturing technologies with the hollow wax mold process could be explored. For instance, the use of additive manufacturing techniques to produce the molds or the application of real-time monitoring and control systems during the casting process could enhance the precision and reliability of the production. This would require a multidisciplinary approach, combining materials science, mechanical engineering, and manufacturing technology to develop more efficient and intelligent casting processes.
7. Comparison with Other Casting Processes
7.1 Investment Casting vs. Sand Casting
Investment casting and sand casting are two widely used casting methods, each with its own advantages and disadvantages. In terms of dimensional accuracy, investment casting generally offers a higher level of precision compared to sand casting. Sand castings often have a rougher surface finish and larger dimensional tolerances due to the nature of the sand mold. The hollow wax mold structure in investment casting further enhances this advantage by reducing the linear shrinkage rate and improving the dimensional accuracy of the casting.
In terms of material selection, investment casting is more suitable for high-temperature alloys and complex geometries, while sand casting can handle a wider range of materials but may not be as effective for producing intricate parts. The production process of investment casting is more complex and time-consuming, involving multiple steps such as wax pattern making, shell building, and dewaxing, while sand casting is relatively simpler and faster. However, the higher quality and precision of investment castings make it a preferred choice for critical applications where dimensional accuracy and material properties are crucial.
7.2 Investment Casting vs. Die Casting
Die casting is another popular casting method known for its high production rate and good dimensional accuracy for certain applications. However, die casting is typically limited to non-ferrous alloys and has restrictions on part geometry due to the use of dies. Investment casting, on the other hand, can handle a wider variety of alloys, including high-temperature alloys, and is more suitable for complex geometries.
The hollow wax mold structure in investment casting provides an additional advantage in terms of reducing shrinkage and improving dimensional accuracy, which is not as prominent in die casting. Die casting often requires high-pressure injection of molten metal into the die, which can lead to porosity and other defects in some cases. Investment casting, with its more controlled and precise process, can produce castings with better internal quality.
8. Industrial Applications and Case Studies
8.1 Aerospace Industry
In the aerospace industry, the demand for high-quality, precision castings is extremely high. Components such as turbine blades, engine parts, and structural elements require strict dimensional accuracy and excellent material properties. The hollow wax mold structure in investment casting has been applied to produce certain aerospace components, achieving improved dimensional accuracy and meeting the stringent requirements of the industry. For example, in the production of turbine blades, the hollow structure has helped to reduce the linear shrinkage rate, resulting in more precise blade profiles and better performance.
Case Study: A leading aerospace manufacturer used the hollow wax mold investment casting process to produce a critical engine component. The original solid wax mold process resulted in a dimensional accuracy of CT7 level, with some parts failing to meet the design specifications. After implementing the hollow wax mold structure, the dimensional accuracy was improved to CT5 level, and all parts met the required standards. This not only ensured the quality of the component but also reduced the rejection rate and production costs.
8.2 Gas Turbine Industry
The gas turbine industry also relies heavily on high-quality castings. The hollow wax mold structure has been found to be beneficial in producing gas turbine components such as blades and nozzles. By reducing the linear shrinkage rate, the structure helps to maintain the precise dimensions of the components, which is crucial for the efficient operation of the gas turbine. In addition, the improved dimensional accuracy can lead to better aerodynamic performance of the components, increasing the overall efficiency of the gas turbine.
Case Study: A gas turbine manufacturing company adopted the hollow wax mold investment casting process for the production of blades. The company observed a significant reduction in the linear shrinkage rate of the wax mold, from 1.16% to 0.54%. As a result, the dimensional accuracy of the blades was improved from CT7 level to CT5 level. The improved blades exhibited better aerodynamic performance, contributing to an increase in the overall efficiency of the gas turbine by approximately 5%.
9. Economic and Environmental Considerations
9.1 Economic Impact
The use of the hollow wax mold structure in investment casting can have a significant economic impact. Firstly, by improving the dimensional accuracy of the casting, the rejection rate is reduced. This means fewer parts need to be remade or scrapped, resulting in cost savings in terms of materials, labor, and production time. In the case studies mentioned above, the reduction in the rejection rate led to substantial cost savings for the aerospace and gas turbine manufacturers.
Secondly, the hollow structure design may potentially reduce the cost of molds. Although it requires some additional design and manufacturing efforts for the hollow structure, it can avoid the need for multiple molds or complex mold designs in some cases. This can lead to a more efficient use of resources and a reduction in mold manufacturing costs.
Finally, the improved quality of the casting can enhance the competitiveness of the product in the market. Higher quality castings can command a higher price, and companies that can produce such castings are more likely to win contracts and gain a larger market share.
9.2 Environmental Considerations
From an environmental perspective, the investment casting process with the hollow wax mold structure has both positive and negative aspects. On the positive side, the reduction in the rejection rate means less waste of materials. This is beneficial for conserving natural resources and reducing the environmental impact associated with the extraction and processing of raw materials.
However, the investment casting process still involves the use of wax materials and various chemicals for shell making and dewaxing. These substances need to be properly managed to avoid environmental pollution. Efforts should be made to recycle and reuse wax materials as much as possible and to ensure that the disposal of chemicals is in accordance with environmental regulations.
In conclusion, the research on the hollow wax mold structure for K648 superalloy castings has significant implications for the investment casting industry. It offers a solution to improve dimensional accuracy, has potential for future development in various directions, and has important economic and environmental considerations. By understanding and applying this technology, the investment casting process can be further optimized to meet the demands of high-tech industries and contribute to sustainable development.
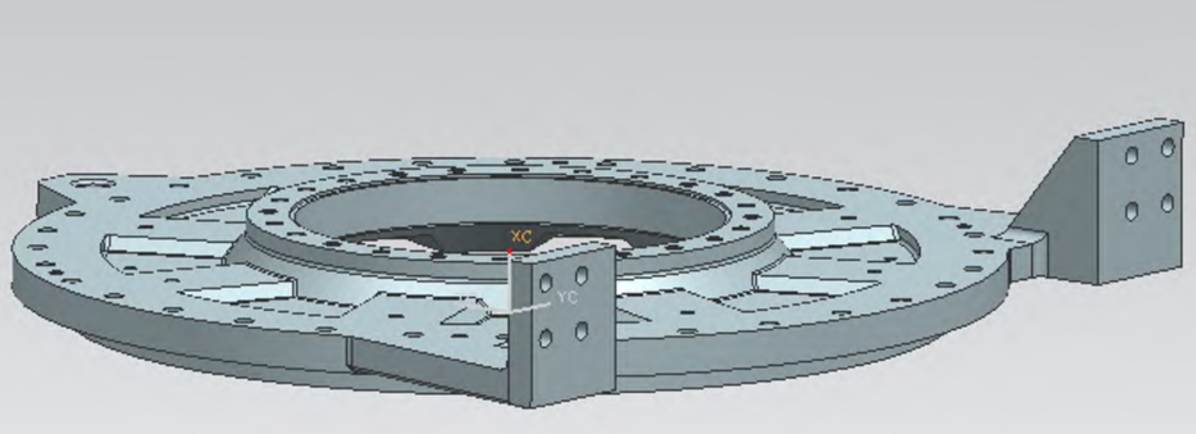