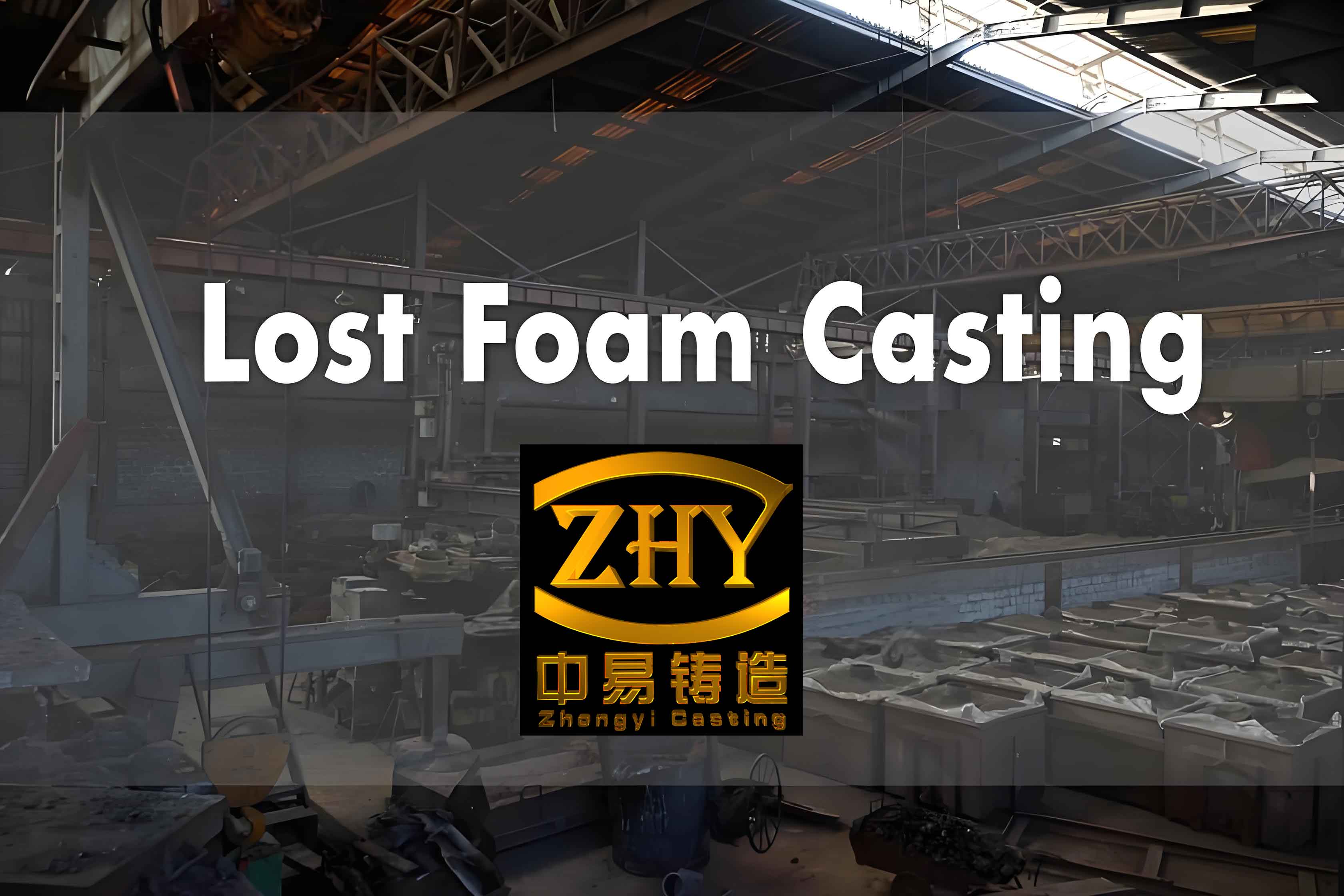
1. Introduction
Lost foam casting, also known as expendable pattern casting, has a history of development since its invention in 1956. It has evolved from small-scale production to large-scale industrial applications. In China, there are numerous factories using this process, but many are still in the stage of understanding and improving the technology. This paper focuses on analyzing common defects in steel castings produced by lost foam casting and proposing corresponding prevention measures.
1.1 Development and Application of Lost Foam Casting
Lost foam casting has seen significant growth in various countries. It has been applied in different production scenarios, from single-piece large-item production to mass-produced small-item assembly line production, and from simple non-machined part production to complex machined part production. In China, although many factories have adopted this process, there is still room for improvement in terms of mastering the technology and reducing defects.
1.2 Importance of Analyzing Defects
Analyzing the defects in lost foam casting of steel castings is crucial for improving product quality, reducing production costs, and enhancing the competitiveness of enterprises. By understanding the causes of defects and implementing effective prevention measures, better-quality steel castings can be produced.
2. Common Defects and Their Causes
2.1 Carbon Pick-up Defect
- Cause: The foam pattern, mainly composed of carbon and hydrogen, decomposes rapidly under high-temperature molten steel. Hydrogen combines with oxygen and is expelled as steam, while free carbon remains and causes surface carburization of the casting. The degree of carbon pick-up varies, being more severe farther from the ingate.
Location | Carbon Pick-up Degree |
Near Ingate | Slight |
Away from Ingate | Severe |
Casting Core | Almost None |
2.2 Porosity Defect
- Caused by Foam Pattern Degradation Products Entrapped in Molten Metal
- Cause: Turbulence during pouring or incomplete gas escape of the pattern during decomposition leads to gas entrapment, forming large and carbon-black-coated pores.
- Caused by Poor Drying of Foam Pattern and Coating
- Cause: Inadequate drying of the foam pattern or coating and excessive foaming agent content result in gas generation during pouring.
- Caused by Excessive Binder in Pattern
- Cause: High gas generation from excessive binder use and slow gasification lead to gas entrapment.
- Caused by Air Entrainment during Pouring
- Cause: An unfilled sprue during pouring entrains air, causing porosity if not expelled.
- Caused by Molten Steel Quality Problems
- Cause: Incomplete deoxidation during steel melting leaves oxygen in the molten steel, forming pores.
2.3 Slag Inclusion Defect
- Cause: Dry sand grains, coatings, and other inclusions enter the casting during pouring. This can be caused by factors such as poor sealing of the sprue, improper packing operations, and inappropriate pouring parameters.
Factor | Influence on Slag Inclusion |
Sprue Sealing | Main Cause if Poor |
Packing Operation | Can Cause if Improper |
Pouring Parameters | Affect Defect Formation |
2.4 Backfire Defect
- Cause: Excessive gas generation from the decomposition of the gas pattern during pouring and insufficient gas expulsion cause a rapid increase in cavity pressure, leading to backfire or ejection of molten metal.
2.5 Negative Pressure Cutting Defect
- Cause: During pouring, if the negative pressure is too high, the coating is too thin or damaged, and the holding pressure time is too long, external air may be sucked into the mold, causing a cutting effect on the molten metal due to the airflow.
3. Prevention Measures for Common Defects
3.1 Prevention Measures for Carbon Pick-up Defect
- Select High-Quality Foam Plastics
- Use foam plastics with low carbon content and high molecular weight. Select raw beads with low gas generation and carbon content and formed foam with low density.
- Choose a Reasonable Pouring Process
- Control pouring temperature and speed, ensure good coating and sand mold permeability, use appropriate mold wall negative pressure, and consider using anti-carburization coatings.
- Utilize the Carbon Pick-up Pattern
- Set a riser at the farthest point from the ingate or at the highest point of the casting to collect carbon-contaminated molten steel.
- Adopt the “Burn First, Pour Later” Method
- Burn the foam plastic in the cavity first to form a cavity and then pour the molten metal.
3.2 Prevention Measures for Porosity Defect
- For Porosity Caused by Foam Pattern Degradation Products
- Improve the process to ensure smooth filling of the molten steel, raise the pouring temperature appropriately, and increase the negative pressure or adjust it according to the situation. Also, improve the permeability of the coating and sand mold.
- For Porosity Caused by Poor Drying of Foam Pattern and Coating
- Fully dry the foam pattern according to the process requirements and ensure the coating is completely dry. Strictly control the amount of foaming agent added.
- For Porosity Caused by Excessive Binder in Pattern
- Use a low-gas-generation model binder and minimize the amount of adhesive used while ensuring proper adhesion.
- For Porosity Caused by Air Entrainment during Pouring
- Design a reasonable pouring system to ensure smooth metal flow during filling and avoid air entrainment. Use a closed pouring system and ensure the sprue is filled. Consider using a hollow sprue mold to reduce gas generation.
- For Porosity Caused by Molten Steel Quality Problems
- Strictly follow the melting process, perform deoxidation treatment before pouring, and purify the molten steel.
3.2 Prevention Measures for Slag Inclusion Defect
- Select a High-Performance Coating
- The coating for steel castings should have high strength, high refractoriness, good thermal shock resistance, good coating adhesion, suspension, and non-flow properties.
- Standardize Packing Operations
- Place the pattern group stably on the bottom sand of the sand box, avoid violent sand addition, and ensure the sprue is sealed. Check for any coating damage before pouring and confirm the absence of floating sand, dust, and debris in the pouring cup.
- Set Reasonable Pouring Parameters
- Select an appropriate pouring head, temperature, and time. Avoid using a large ladle for a small casting. Choose a suitable pouring temperature considering the coating performance.
- Determine the Appropriate Negative Pressure
- For steel castings, a suitable negative pressure is generally -0.030 – -0.045MPa. Avoid excessive negative pressure to prevent sand and slag entrapment.
- Set Slag Blocking, Skimming, and Collecting Risers
- Design the pouring system with slag blocking and skimming functions and set collecting risers on the casting to improve the slag inclusion defect.
- Adopt Molten Steel Purification Technology
- Consider purification during the entire process from steel melting to pouring into the mold.
3.4 Prevention Measures for Backfire Defect
- Control EPS Pattern Density and Drying
- Keep the EPS pattern density between 0.015 – 0.020 g/cm³, ensure the pattern and the coated pattern are dry to reduce moisture and gas generation.
- Select a Permeable Coating and Adjust Thickness
- Use a coating with good permeability and adjust the thickness to 1.0 – 2.0mm to allow gas to escape.
- Control Sand Permeability and Grain Size and Sand Box Design
- Control the permeability and grain size of the dry sand and design a reasonable sand box. Control the negative pressure to ensure proper pattern gasification.
- Control Pouring Temperature and Speed
- Use the heat of the molten steel to ensure pattern gasification and control the pouring speed to avoid excessive gas generation.
- Design a Reasonable Pouring System
- Ensure smooth and balanced filling of the molten metal into the mold to allow gas to escape from the cavity.
3.5 Prevention Measures for Negative Pressure Cutting Defect
- Control Pouring Parameters
- Keep the negative pressure during pouring within -0.020 – -0.035MPa, ensure the coating thickness is 1.0 – 2.0mm, and control the pouring height and the holding pressure time after pouring.
4. Conclusion
Lost foam casting of steel castings has great potential for development. By understanding and addressing the common defects through appropriate prevention measures, high-quality steel castings can be produced. This requires strict control of each process step, from raw material selection to pouring and post-treatment, as well as continuous improvement of technology and operator skills.