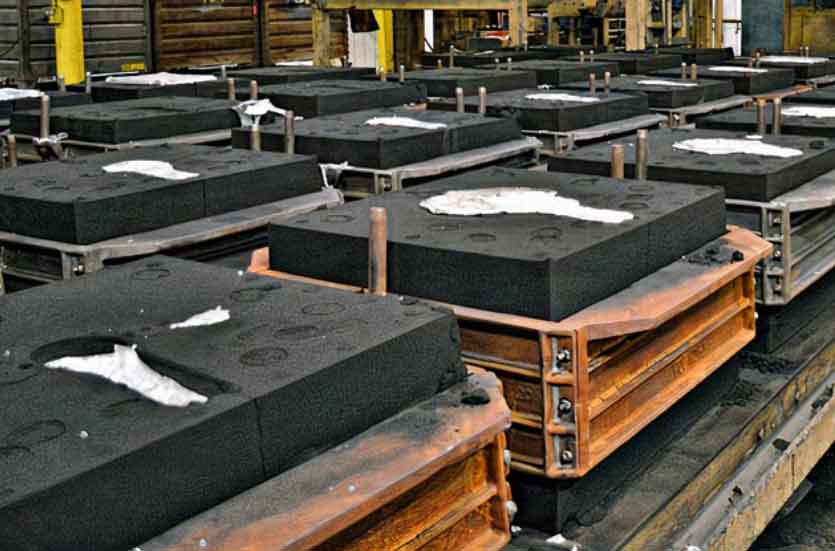
Resin sand casting is known for its versatility and cost-effectiveness, making it a popular choice in the manufacturing industry for a wide range of components. Here are some key reasons why resin sand casting is considered a versatile and cost-effective manufacturing process:
1. Versatility in Component Size and Complexity:
- Resin sand casting can accommodate a broad range of component sizes, from small to large. It is particularly suitable for producing components with complex geometries, internal features, and fine details.
2. Wide Material Compatibility:
- Resin sand casting is compatible with various metals and alloys, including ferrous and non-ferrous materials, allowing manufacturers to produce components with a diverse range of mechanical properties and performance characteristics.
3. Cost-Effective Tooling:
- Resin sand casting typically involves lower tooling costs compared to some other casting methods, such as investment casting or die casting. This makes it an economical option, especially for low to medium production volumes.
4. Rapid Prototyping and Short Lead Times:
- The use of 3D-printed patterns in resin sand casting enables rapid prototyping and short lead times for new component designs. This agility in tooling allows for quick iteration and reduced time-to-market.
5. Superior Surface Finish:
- Resin sand casting provides a better surface finish compared to traditional green sand casting. This minimizes the need for post-casting finishing, saving time and costs during the production process.
6. Customization and Small Batch Production:
- Resin sand casting is well-suited for customized components and small batch production. Its flexibility allows for cost-effective production of low volumes or one-off parts without the need for expensive permanent tooling.
7. Design Flexibility:
- Resin sand casting offers design flexibility, enabling the creation of intricate shapes, thin walls, and complex internal features. This allows engineers to optimize component designs for specific applications.
8. Part Consolidation:
- Resin sand casting enables the production of complex castings that consolidate multiple components into a single piece. This can reduce assembly time and minimize potential weak points in the component.
9. Eco-Friendly Binders:
- Resin sand casting uses organic resin binders that are more environmentally friendly compared to some other binders used in sand casting processes. This aligns with sustainability goals and reduces environmental impact.
10. Simplicity of Process:
- Resin sand casting is relatively straightforward and can be carried out using basic equipment and facilities, making it accessible to a wide range of foundries and manufacturers.
Resin sand casting’s versatility and cost-effectiveness make it a valuable manufacturing process for a variety of industries and applications. Whether for prototyping, low to medium volume production, or the production of complex components, resin sand casting offers an efficient and economically viable solution to meet various manufacturing needs.