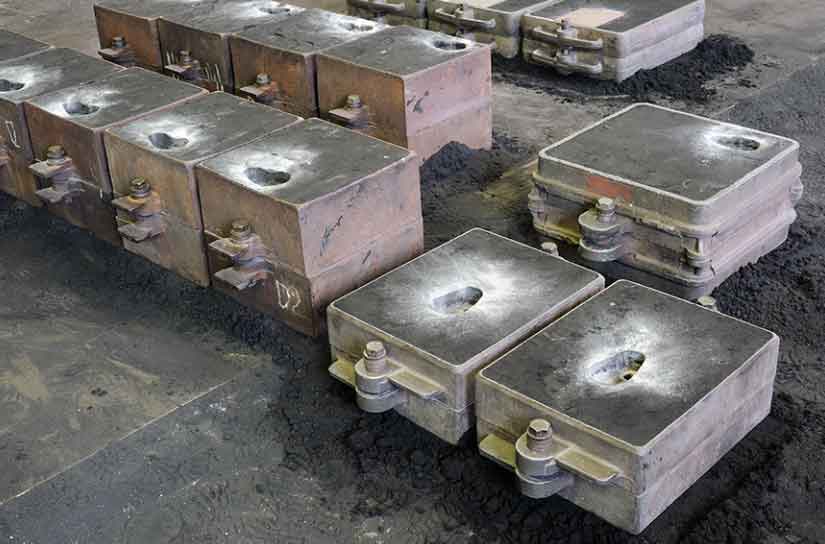
The evolution of foundry practices has seen the growing adoption and embracement of resin sand casting technology. Over the years, resin sand casting has become increasingly popular in the manufacturing industry due to its numerous advantages over traditional sand casting methods. Here are some key aspects of the evolution of foundry practices with the integration of resin sand casting technology:
1. Improved Dimensional Accuracy and Surface Finish:
- Resin sand casting offers better dimensional accuracy and surface finish compared to traditional green sand casting. Foundries have recognized the importance of producing components with precise dimensions and smoother surfaces, leading to improved product quality.
2. Enhanced Design Flexibility:
- Resin sand casting’s ability to create intricate geometries and fine details has revolutionized foundry practices. Manufacturers can now produce complex components that were previously challenging or impossible with traditional sand casting methods.
3. Rapid Prototyping and Shorter Lead Times:
- The use of 3D-printed patterns in resin sand casting has accelerated the prototyping process, allowing foundries to quickly iterate and refine designs. Shorter lead times are critical in meeting market demands and staying competitive.
4. Customization and Small Batch Production:
- Resin sand casting’s flexibility enables cost-effective production of custom components and small batch sizes without the need for expensive permanent tooling. This has opened up opportunities for manufacturers to cater to specialized industries and niche markets.
5. Material Diversity and Performance Optimization:
- Resin sand casting accommodates a wide range of materials, allowing foundries to optimize component designs based on specific performance requirements. The ability to choose from various metals and alloys enhances the versatility of the manufacturing process.
6. Sustainable Practices:
- The use of organic resin binders in resin sand casting aligns with the growing focus on sustainability in the manufacturing industry. Foundries have embraced this eco-friendly approach to reduce their environmental impact.
7. Advanced Simulation and Modeling:
- As foundries embrace digitalization, advanced simulation and modeling tools have become integral in optimizing the resin sand casting process. These tools help optimize mold designs, gating systems, and solidification processes, leading to improved efficiency and cost-effectiveness.
8. Integration of Additive Manufacturing:
- The integration of additive manufacturing, particularly 3D printing, has revolutionized pattern-making for resin sand casting. 3D-printed patterns offer increased design freedom and reduce the lead time for producing molds.
9. Streamlined Communication and Collaboration:
- Digital connectivity and communication tools have facilitated collaboration between foundries and customers. Real-time communication and data sharing have improved project management and resulted in higher customer satisfaction.
10. Industry-Wide Adoption:
- As the benefits of resin sand casting become more apparent, it has gained widespread adoption across various industries. Foundries worldwide have recognized the advantages of this technology, leading to its evolution as a standard casting method.
The evolution of foundry practices with the embracement of resin sand casting technology has brought about advancements in design, efficiency, and sustainability. As the manufacturing landscape continues to evolve, resin sand casting will likely remain a key player in meeting the demands for complex components, rapid prototyping, and efficient production processes.