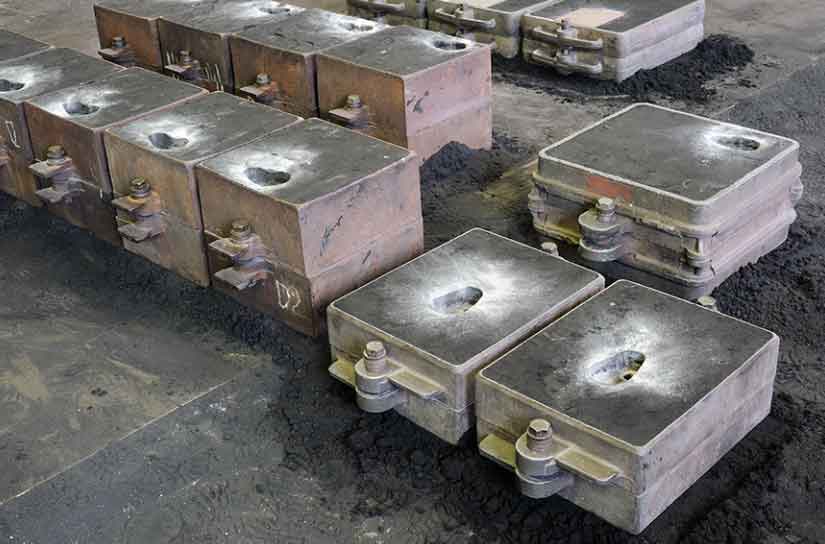
Resin sand casting is a favored method for producing automotive parts due to its ability to provide strength, reliability, and cost-effectiveness. The automotive industry demands high-performance components that can withstand various mechanical stresses and environmental conditions while maintaining consistent quality. Resin sand casting offers several benefits that make it well-suited for manufacturing automotive parts:
1. Material Versatility:
- Resin sand casting accommodates a wide range of materials used in the automotive industry, such as gray iron, ductile iron, aluminum alloys, and steel. Different materials can be selected to suit specific performance requirements.
2. Complex Geometries:
- Automotive parts often feature intricate shapes and complex geometries. Resin sand casting allows for the production of parts with undercuts, thin walls, and fine details, meeting the design demands of modern automotive components.
3. Structural Integrity:
- Resin sand castings exhibit excellent structural integrity, providing the necessary strength and durability for critical automotive applications like engine blocks, transmission housings, and suspension components.
4. Dimensional Accuracy:
- Resin sand casting delivers high dimensional accuracy, ensuring that automotive parts meet tight tolerances and fit seamlessly within the vehicle’s assembly.
5. Weight Optimization:
- Lightweighting is crucial for improving fuel efficiency and reducing emissions. Resin sand casting allows for optimized material use and the production of lightweight automotive components without compromising strength and reliability.
6. High-Volume Production:
- Resin sand casting can handle high-volume production, making it suitable for mass-producing automotive parts, such as cylinder heads, intake manifolds, and brake calipers.
7. Cost-Effectiveness:
- Resin sand casting is a cost-effective method for manufacturing automotive parts, especially for components with intricate designs and low to medium production volumes.
8. Consistent Quality:
- Resin sand casting’s reliable and repeatable process ensures consistent quality and uniformity in automotive parts, reducing the risk of defects and rejects.
9. Material Compatibility:
- Automotive parts require materials with excellent wear resistance, corrosion resistance, and thermal properties. Resin sand casting allows for the use of materials that meet these demands, ensuring parts’ reliability on the road.
10. Environmental Friendliness:
- Resin sand casting generates less waste compared to other casting methods, contributing to a more environmentally friendly manufacturing process for automotive parts.
Due to these advantages, resin sand casting is widely used in the automotive industry to produce a wide range of components, including engine blocks, cylinder heads, pistons, transmission housings, suspension parts, and more. It remains a key casting technology for automotive manufacturers seeking components that offer the strength, reliability, and performance necessary for safe and efficient vehicles.