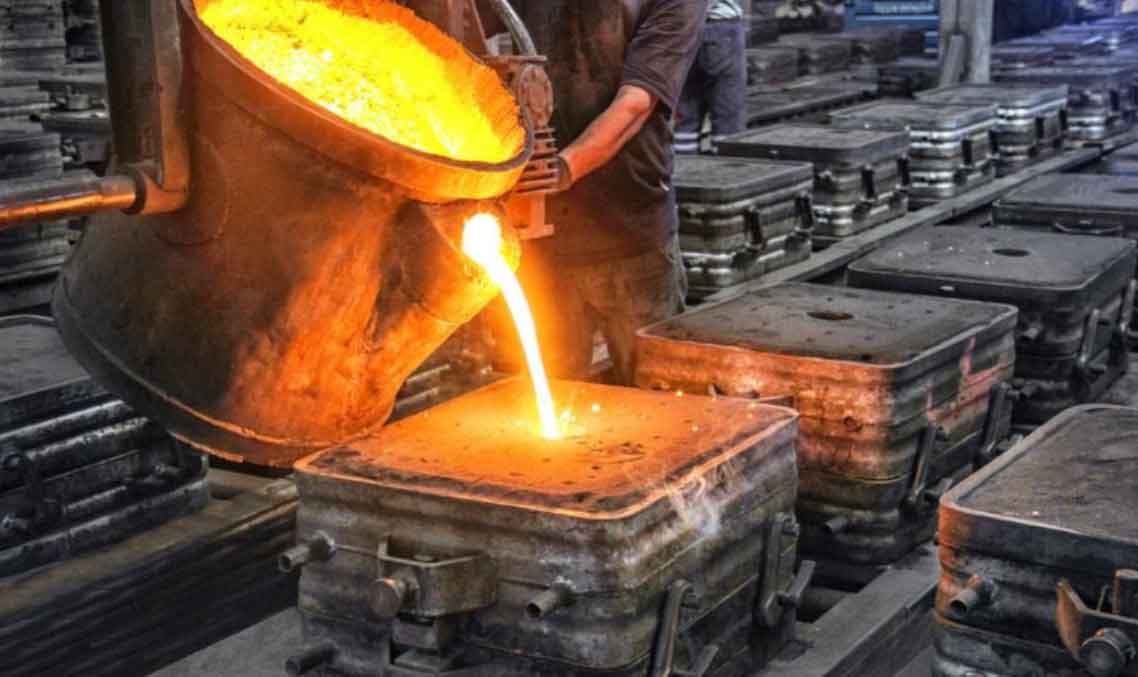
Automation and robotics play a significant role in modern sand casting manufacturing, transforming the way castings are produced and improving overall efficiency, productivity, and quality. The integration of automation and robotics offers numerous benefits to foundries, making the sand casting process more competitive and adaptable to the demands of the industry. Here are some key roles of automation and robotics in modern sand casting manufacturing:
1. Mold Handling and Manipulation:
- Automated systems and robots are used to handle molds and manipulate them throughout the casting process. They can move heavy and bulky molds with precision and consistency, reducing the manual labor required and ensuring safe and efficient handling.
2. Core Assembly and Placement:
- Robots can assemble cores and place them accurately within the mold cavities. This ensures that complex geometries are correctly formed, leading to high-quality castings with intricate details.
3. Pouring and Metal Delivery:
- Automated pouring systems and robots are used to control the pouring of molten metal into the molds. They ensure a consistent and controlled flow of metal, minimizing the risk of defects such as turbulence and inclusions.
4. Gating and Riser System Design:
- Robots and automation assist in the design and optimization of gating and riser systems using advanced simulation and modeling tools. This helps achieve better mold filling and solidification patterns, leading to improved casting quality.
5. Mold Coating and Preparation:
- Robots are employed to apply mold coatings and prepare the molds for casting, ensuring uniform and consistent coatings for improved mold release and surface finish.
6. Sand Handling and Recycling:
- Automation helps in the handling and preparation of sand, including sand mixing, conditioning, and recycling. Automated systems can efficiently separate and recycle used sand, reducing waste and material consumption.
7. Post-Casting Finishing:
- Robots are utilized in post-casting finishing processes, such as trimming, grinding, and deburring, to achieve consistent and precise results. This improves the surface finish and ensures that castings meet the required specifications.
8. Real-Time Monitoring and Quality Control:
- Automation and robotics facilitate real-time monitoring of the casting process, allowing for data collection and analysis. This data-driven approach enables quick identification and resolution of potential issues, leading to better quality control and reduced scrap rates.
9. Flexible Manufacturing and Customization:
- Automation and robotics enable foundries to be more flexible in handling diverse casting requirements and customization. Robots can quickly switch between different tasks and adapt to changing production needs.
10. Improved Safety and Ergonomics:
- By automating repetitive and physically demanding tasks, automation and robotics improve the safety and ergonomics of the working environment for foundry personnel.
By incorporating automation and robotics into the sand casting process, foundries can enhance their overall competitiveness, reduce lead times, improve quality, and optimize resource utilization. The combination of human expertise and advanced automation technologies creates a modern sand casting manufacturing environment that meets the demands of today’s fast-paced and dynamic industries.