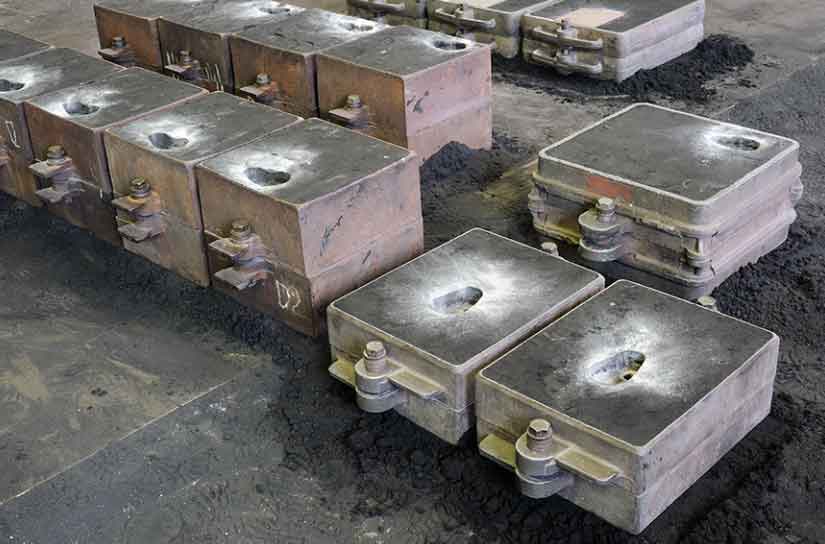
Resin sand casting is a versatile and efficient casting method that can overcome challenges in high-volume production. While high-volume production typically poses challenges related to time, cost, and consistency, resin sand casting can address these challenges in the following ways:
- Mold and Pattern Durability: In high-volume production, molds and patterns need to withstand repeated use without significant degradation. Resin sand casting can utilize durable patterns, such as those made from metal or composite materials, to ensure longevity and maintain dimensional accuracy over multiple casting cycles. This helps minimize downtime and maintain consistent production rates.
- High-Speed Molding and Core-Making: Resin sand casting allows for rapid mold and core production. With efficient mold preparation techniques and the ability to reuse sand, resin sand casting supports high-speed molding and core-making processes. This reduces cycle times and increases the overall productivity of the casting operation.
- Automated Handling and Processing: Automation plays a crucial role in achieving high-volume production in resin sand casting. Automated systems can handle various tasks, including mold handling, sand preparation, pouring, and post-casting operations. By implementing robotics and automation, foundries can achieve consistent and efficient production, reducing the reliance on manual labor and increasing throughput.
- Process Optimization and Control: High-volume production requires stringent process optimization and control to ensure consistent quality and productivity. Resin sand casting can leverage advanced process monitoring and control systems to maintain stable process parameters such as temperature, humidity, and sand quality. Real-time monitoring helps identify process variations or issues early on, allowing for prompt adjustments and minimizing the risk of quality defects.
- Efficient Gating and Riser Design: Gating and riser design optimization is crucial for high-volume production to ensure consistent casting quality and minimize scrap or rework. Resin sand casting can benefit from advanced simulation software that enables designers to optimize gating and risering systems for improved metal flow, reduced defects, and efficient use of material.
- Material Handling and Melting Efficiency: Handling large volumes of materials and optimizing melting efficiency is essential in high-volume production. Resin sand casting can employ efficient material handling systems, such as automated sand delivery and storage solutions, to ensure a continuous supply of materials. Additionally, energy-efficient melting techniques and equipment can be utilized to minimize energy consumption and maximize production throughput.
- Quality Assurance and Inspection: Quality assurance is crucial in high-volume production to maintain consistent product quality. Resin sand casting can integrate quality control systems such as non-destructive testing, dimensional inspections, and real-time monitoring to ensure adherence to specifications. Statistical process control (SPC) techniques can be employed to monitor process performance and identify potential quality issues before they impact production.
- Lean Manufacturing Principles: Applying lean manufacturing principles can help optimize high-volume resin sand casting production. Techniques such as value stream mapping, 5S organization, and waste reduction methodologies can identify bottlenecks, streamline processes, and eliminate non-value-added activities, leading to improved efficiency, reduced costs, and increased productivity.
Resin sand casting, when properly optimized and integrated with automation, process control, and lean manufacturing principles, can overcome challenges in high-volume production. By addressing issues related to durability, speed, automation, process optimization, and quality assurance, resin sand casting can deliver consistent, cost-effective, and high-quality castings in high volumes.