Resin sand casting and die casting are two popular casting methods used in manufacturing. Let’s compare these two methods:
Resin Sand Casting:
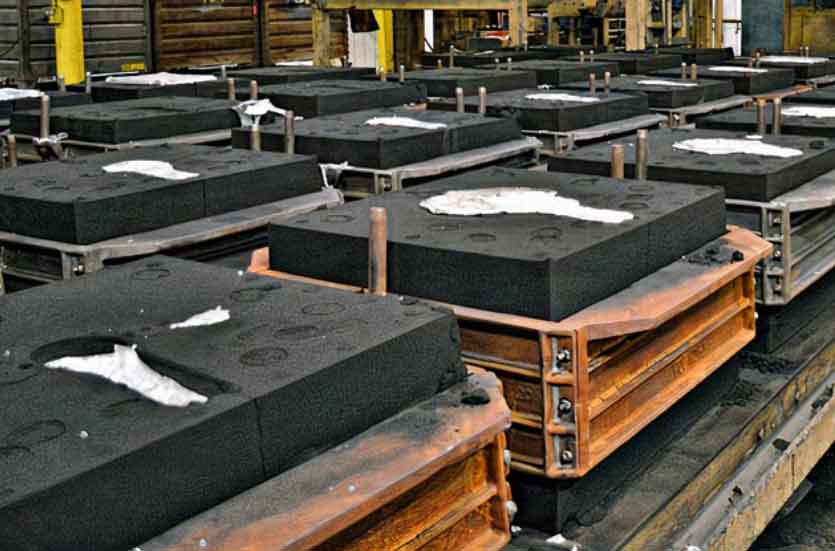
Advantages:
- Design Flexibility: Resin sand casting allows for the production of complex shapes, intricate details, and thin-walled components that may be challenging to achieve with die casting.
- Cost-Effectiveness: Resin sand casting is generally more cost-effective for small to medium-sized production runs, as it requires less expensive tooling and setup compared to die casting.
- Material Flexibility: Resin sand casting supports a wide range of metal alloys, providing flexibility in material selection to meet specific application requirements.
- Surface Finish: Resin sand casting can produce castings with good surface finish and dimensional accuracy, reducing the need for extensive post-casting machining or surface treatments.
- Rapid Prototyping: Resin sand casting enables the quick production of functional prototypes, facilitating faster product development cycles and design iterations.
Considerations:
- Mold Preparation Time: The preparation and curing time of the resin sand mold can be relatively longer compared to die casting, extending the overall production time, particularly for larger or more intricate molds.
- Lower Production Efficiency: Resin sand casting generally has a slower production rate compared to die casting, making it less suitable for high-volume production.
- Size Limitations: Resin sand casting is typically better suited for smaller to medium-sized components, while die casting is capable of producing larger parts.
- Mold Fragility: Resin sand molds can be more fragile compared to the durable steel or aluminum dies used in die casting, requiring careful handling and transportation to avoid mold breakage.
Die Casting:

Advantages:
- High Production Efficiency: Die casting is highly efficient, making it suitable for high-volume production runs. It allows for rapid production cycles, high repeatability, and fast cooling times.
- High Precision and Surface Finish: Die casting offers high dimensional accuracy and excellent surface finish, often requiring minimal post-casting machining or surface treatments.
- Thinner Walls and Complex Shapes: Die casting can achieve thinner wall sections and produce parts with more intricate details and complex shapes compared to resin sand casting.
- Reduced Scrap and Material Waste: Die casting generates less material waste compared to resin sand casting, as it utilizes precise amounts of molten metal.
- Automation Potential: Die casting can be highly automated, reducing labor costs and increasing production efficiency.
Considerations:
- Higher Tooling Costs: Die casting requires expensive steel or aluminum dies, resulting in higher upfront tooling costs compared to resin sand casting.
- Limited Material Selection: Die casting is typically limited to non-ferrous metals such as aluminum, magnesium, and zinc alloys, whereas resin sand casting supports a wider range of materials.
- Design Limitations: Die casting may have limitations in producing complex shapes with thin walls or intricate details compared to resin sand casting.
- Longer Lead Times for Tooling: The fabrication of dies for die casting may require longer lead times compared to resin sand casting, as dies need to be machined and finished before production can begin.
In summary, resin sand casting offers design flexibility, cost-effectiveness for small to medium production runs, and the ability to use a wide range of materials. It is suitable for complex shapes and components with thinner walls. Die casting, on the other hand, provides high production efficiency, excellent surface finish, and precision for high-volume production runs. It is particularly advantageous for non-ferrous metals and parts with intricate details. The choice between resin sand casting and die casting depends on factors such as part complexity, production volume, desired surface finish, material requirements,and cost considerations.