Sand casting technology has indeed revolutionized the manufacturing industry, offering numerous benefits and advancements that have transformed the way metal parts are produced. Here are some ways in which sand casting technology has revolutionized manufacturing:
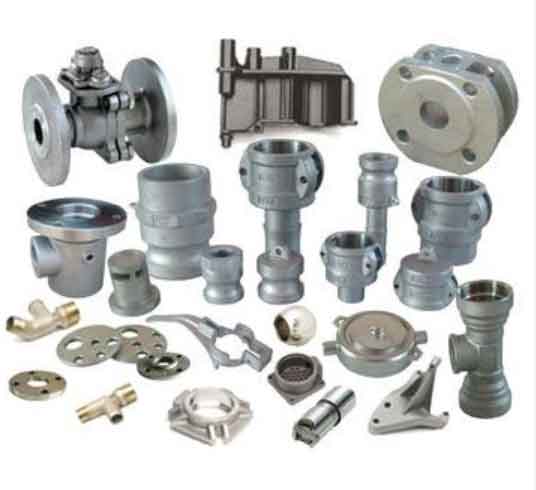
- Design Freedom and Complexity:
- Sand casting technology allows for the production of highly complex and intricate part designs with greater design freedom.
- It enables the creation of parts with internal cavities, thin walls, and complex geometries that were previously difficult to achieve through traditional manufacturing methods.
- Manufacturers can produce parts with intricate details and unique shapes, meeting the demands of modern design requirements.
- Improved Efficiency and Accuracy:
- Advancements in sand casting technology have significantly improved the efficiency and accuracy of the process.
- Digital design tools, computer-aided simulations, and optimization algorithms help optimize mold designs, gating systems, and process parameters.
- This leads to improved mold filling, reduced defects, and enhanced dimensional accuracy, resulting in higher-quality castings and minimizing the need for post-casting modifications.
- Advanced Materials and Alloys:
- Sand casting technology has expanded its capabilities to accommodate a wide range of materials and alloys.
- Manufacturers can cast parts using various metals, including aluminum, iron, steel, brass, and more, depending on the application requirements.
- Advanced alloys, such as high-strength and heat-resistant materials, can be successfully cast using sand casting technology, broadening its application possibilities.
- Additive Manufacturing Integration:
- The integration of additive manufacturing, or 3D printing, with sand casting has revolutionized the production of patterns, cores, and molds.
- 3D-printed patterns and cores allow for complex designs, rapid prototyping, and customization, reducing lead times and costs.
- The combination of sand casting and additive manufacturing enables manufacturers to produce intricate and customized parts with greater efficiency and accuracy.
- Automation and Robotics:
- Automation and robotics have been integrated into sand casting processes, improving productivity and consistency.
- Automated systems can handle tasks such as mold preparation, pouring, and shakeout, reducing manual labor and enhancing process control.
- Robots can perform repetitive tasks with precision, ensuring consistent mold quality, reducing errors, and increasing overall manufacturing efficiency.
- Sustainable Practices:
- Sand casting technology has embraced sustainable practices, minimizing environmental impact.
- Sand reclamation and recycling systems allow for the reuse of sand, reducing waste and conserving resources.
- Environmentally friendly binders and additives are being used, reducing emissions and improving the sustainability of the process.
- Cost-Effectiveness:
- Sand casting technology offers cost-effective solutions for manufacturing complex metal parts, especially in low to medium volume production.
- Lower tooling costs, shorter lead times, and the ability to produce customized parts without significant upfront investments make sand casting economically viable.
- The cost-effectiveness of sand casting has made it an attractive option for various industries, including automotive, aerospace, and consumer goods.
Sand casting technology has revolutionized manufacturing by enabling the production of complex parts with improved efficiency, accuracy, and sustainability. The integration of digital tools, additive manufacturing, automation, and sustainable practices has expanded the capabilities and applications of sand casting, making it a versatile and reliable manufacturing method in today’s industry.