The large cylinder block iron castings are typical thick large iron castings, and the riser free process is mainly used. Due to the thickness of the large cylinder block, the cooling rate is relatively slow and the shrinkage rate is small, and the shrinkage time is delayed compared with that of the small and medium-sized cylinder castings; because of the large size of the casting, the back filling effect of the pouring process is obvious, and the edge and surface of the cylinder body iron castings begin to expand graphitized first, and the expansion time is relatively advanced, so that the equilibrium point of the cooling and solidification of the iron castings reaches the feeding system in advance The moment of the end. The relationship among the mass (unit: kg), casting modulus (unit: cm), perimeter quotient of casting quality (unit: kg / cm), sectional area of ingate (unit: mm) and number of gates (unit: mm) were counted.
(1) According to the statistics, the sample modulus of cast iron castings of cylinder block is more than 2.5cm, which is in line with the technological conditions without riser under the guidance of proportional solidification theory, that is, the feeding of large cylinder body iron castings is completed by the post feeding effect in the pouring process and the graphitization expansion in the solidification process, and there is no need to design a feeding riser.
(2) The large number of gates indicates that the gating system adopts the way of dispersive introduction. The advantages of this method are: avoiding the formation of new hot spots due to centralized introduction, ensuring the smooth filling of mold during the pouring process, being conducive to the superposition of expansion and contraction and the uniformity and rationality of temperature field distribution of cylinder body iron castings, and reducing the possibility of deformation or cracks of cast iron castings due to uneven distribution of temperature gradient. In addition, for the cylinder block, the gate of gating system should be symmetrical to meet the requirements of structural uniformity of cylinder block iron castings.
The gating system adopts the step type quick casting process, which has the advantages of bottom pouring and top pouring. In the beginning, bottom injection was used to reduce the erosion of molten metal, and the top injection in the middle and late stage increased the temperature of the upper part of the cast iron to prevent overheating of the lower part and air holes in the upper part of the cast iron. The temperature gradient from bottom to top was formed in the casting of the cylinder block. The molten metal below solidified first and then entered into the graphitized expansion state, which could effectively compensate the shrinkage of the upper molten metal; When all the iron castings enter into the stage of graphitization expansion and the runner has solidified, the graphitization expansion effect of iron castings can be further fully utilized to better control the casting quality.
The section area ratio of gating system and the mass of cast iron (unit: kg) for riser free process.
The section area of runner in gating system is based on the theory of big hole
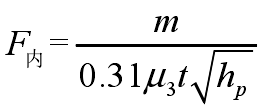
Where
M — Casting mass (kg)
μ 3 — discharge coefficient of ingate, recommended value is 0.50 ~ 0.60
T — pouring time (s)
HP — average head (mm)
In practical production, the pouring time is generally based on empirical formula,
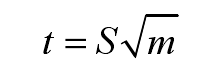
Where
S — relation coefficient
The empirical formula of runner area can be deduced
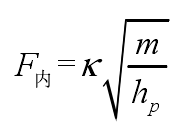
Where, κ – empirical coefficient, 3.43 ~ 4.68.