The surface slag inclusion defect is the most common and the most difficult to avoid on the surface of gas turbine intake cylinder casting surface, mainly concentrated in the upper plane of pouring position, the upper surface of air port surface and the dead angle position of casting filling process. The horizontal direction of air port surface is a large plane with wavy line, which is the most easy position to form slag inclusion defect. Macroscopically, the machined or polished surface shows irregular dark and lusterless slag inclusions with dense and discontinuous distribution, and flake or spherical graphite can be observed in microscopic microstructure.
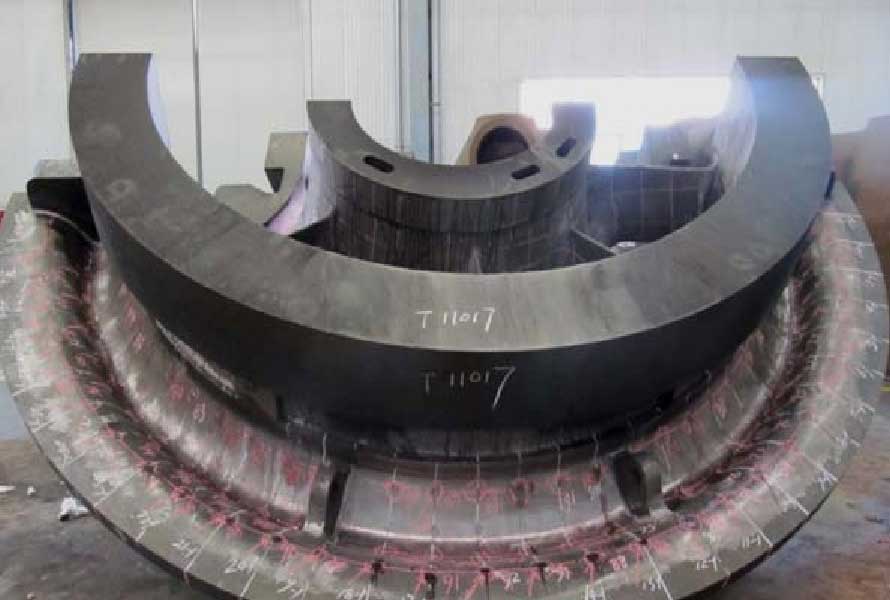
The technical requirements of the inlet cylinder casting surface 100% pass the MT test. Due to its complex chamber structure, the sand core will be covered by high temperature molten iron during casting, which is prone to surface defects such as slag inclusion, inclusion, air hole, serious sand sticking and sand core sintering. Some small defects can not be found by visual inspection, but can not be found in the casting Mt During the inspection, the magnetic trace obviously exceeded the standard, and the distribution of slag inclusion defects on the surface during the first trial production is shown in the figure.
The slag inclusion defect mainly refers to the slag or metal oxide dregs wrapped in the inner or surface of the intake cylinder casting, which is embedded in the casting body and has a serious impact on the mechanical properties of the casting, especially on the high toughness and yield strength of the gas turbine inlet cylinder casting. The stress concentration or crack will be formed at some special cross position of wall thickness, which will greatly reduce the fatigue strength of the casting. These slag inclusion defects are not allowed to exist in the acceptance standard of the intake cylinder casting.