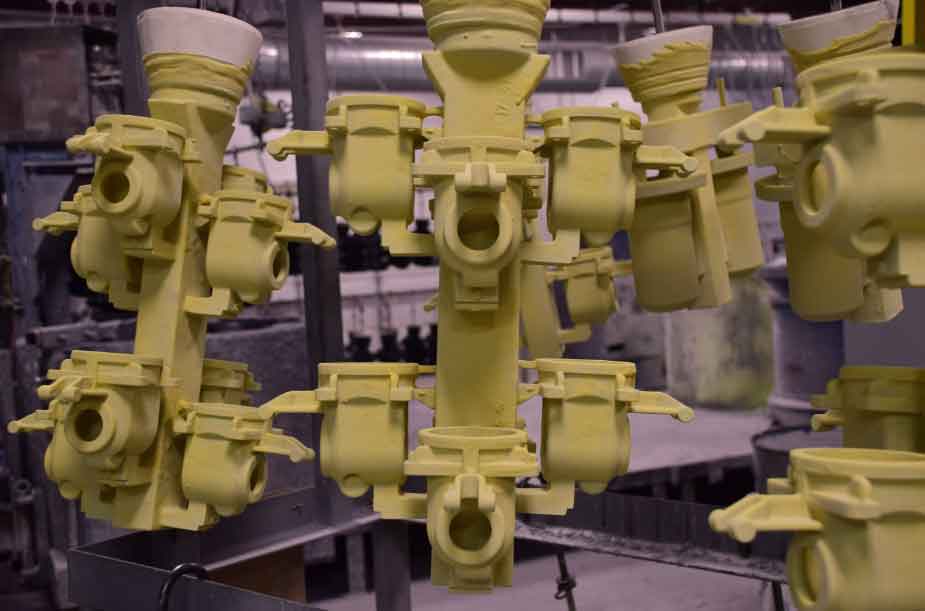
Sand casting serves as a vital bridge between the design and production stages in manufacturing, offering several advantages that facilitate the translation of design concepts into physical metal parts. Let’s explore how sand casting bridges the gap between design and production.
Design Flexibility and Complexity
Sand casting provides designers with the freedom to create complex and intricate part designs. Designers can incorporate features such as undercuts, thin walls, and internal cavities into their designs, pushing the boundaries of what is achievable with other manufacturing processes. This flexibility enables designers to translate their creative concepts into tangible designs without significant limitations.
Prototyping and Iterative Design
Sand casting is well-suited for prototyping and iterative design processes. The relatively low cost of tooling and the ability to modify sand molds easily make it an ideal process for producing prototypes. Designers can quickly evaluate and test their designs, making necessary adjustments and improvements before moving into mass production. This iterative design approach reduces the risk of costly design errors and ensures that the final product meets the desired specifications.
Design for Manufacturability
Sand casting encourages the practice of “design for manufacturability,” wherein designers consider the constraints and requirements of the casting process during the design phase. By understanding the capabilities and limitations of sand casting, designers can optimize their designs to enhance manufacturability and improve the efficiency of the production process. This collaboration between designers and casting engineers helps ensure that the final design is both aesthetically pleasing and feasible to produce.
Collaboration and Communication
Sand casting fosters collaboration and effective communication between designers, engineers, and casting specialists. The iterative nature of the sand casting process encourages continuous feedback and discussion among stakeholders. Designers can work closely with casting engineers to optimize the design for the casting process, addressing issues such as mold filling, solidification, and cooling. This collaboration ensures that the design intent is preserved while accommodating the technical requirements of the casting process.
Design Validation and Verification
Sand casting allows for the validation and verification of designs before committing to mass production. By producing physical castings, designers can assess the functionality, fit, and performance of the parts. This validation process ensures that the design meets the intended requirements and functionality. Any necessary modifications or improvements can be made at an early stage, reducing the risk of costly design changes during later phases of production.
Seamless Transition to Production
Once the design is validated and optimized, sand casting facilitates a seamless transition from design to production. The molds are created based on the finalized design, and molten metal is poured into the molds to produce the desired castings. With proper planning and coordination, the design information can be transferred directly to the production stage, minimizing the potential for errors and ensuring consistency between the design intent and the manufactured parts.
Conclusion
Sand casting serves as a critical bridge between design and production in the manufacturing process. It enables designers to explore complex geometries, prototype designs, optimize for manufacturability, collaborate with casting specialists, validate designs, and smoothly transition to mass production. By leveraging the advantages of sand casting, manufacturers can bridge the gap between design creativity and the realization of physical metal parts, ensuring that innovative and functional designs are successfully brought to life.