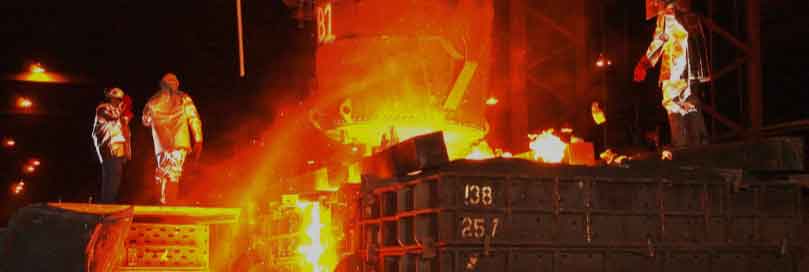
Sand casting is a highly versatile manufacturing process that can produce a wide range of component sizes, from small intricate parts to large-scale structures. Its adaptability to different sizes makes it a preferred choice in various industries. Let’s explore the versatility of sand casting in terms of producing both small components and large structures.
Small Components
- Intricate Designs: Sand casting can produce small components with intricate designs, including intricate patterns, complex geometries, and fine details. The use of high-quality molding sand and precise pattern-making techniques allows for the reproduction of intricate features with excellent dimensional accuracy.
- Thin Walls and Fine Features: Sand casting is capable of producing small components with thin walls and delicate features. With proper gating and risering design, the molten metal can fill even the narrowest sections of the mold, ensuring the integrity of thin walls and intricate details.
- High Precision: Sand casting can achieve high precision in small components. Skilled pattern makers and mold makers ensure that the molds are accurately crafted, resulting in precise dimensions and tight tolerances in the final castings.
- Cost-Effective Production: Sand casting is a cost-effective option for small component production, especially when the production volume is relatively high. The low-cost tooling, readily available materials, and efficient production processes make sand casting economically viable for small parts.
Large Structures
- Size Scalability: One of the remarkable advantages of sand casting is its scalability to produce large castings. Sand casting is capable of producing structures ranging from a few kilograms to several tons in weight. The use of larger molds, specialized molding techniques, and appropriate equipment allow for the creation of large-scale castings.
- Complex Shapes: Sand casting can accommodate the production of large structures with complex shapes and configurations. It can handle the casting of large and irregularly shaped components, such as engine blocks, pump housings, and structural components for buildings and infrastructure.
- Structural Integrity: The solidification process in sand casting enables the creation of structurally sound large-scale castings. The controlled solidification and cooling rates ensure proper grain structure and integrity, resulting in strong and reliable castings for load-bearing applications.
- Cost-Effective Alternative: Sand casting provides a cost-effective alternative for producing large structures compared to other manufacturing methods, such as forging or welding. The relatively low tooling and equipment costs, as well as the ability to produce complex shapes in a single casting, contribute to cost savings in the production of large structures.
- Design Adaptability: Sand casting offers design adaptability for large structures. Design modifications can be easily implemented by modifying the patterns or molds, allowing for quick adjustments and improvements to meet specific project requirements.
Conclusion
Sand casting demonstrates remarkable versatility by catering to the production of both small components and large structures. Its adaptability to intricate designs, thin walls, and high precision makes it suitable for small components, while its scalability, ability to produce complex shapes, and cost-effectiveness make it a preferred choice for large-scale structures. Sand casting provides a flexible and efficient manufacturing solution across a broad size spectrum, meeting the diverse needs of industries ranging from automotive and aerospace to construction and energy.