1. Wax mold manufacturing
The deformation is controlled by adding three-dimensional support to the sand casting; By preheating PS parts before waxing, adjust the preheating temperature, and slow down the cooling rate after waxing. Figure 1 shows the wax mold model of the cover sand mold casting. From the three-dimensional scanning test results in Figure 2, the overall deformation of the wax mold is significantly reduced.
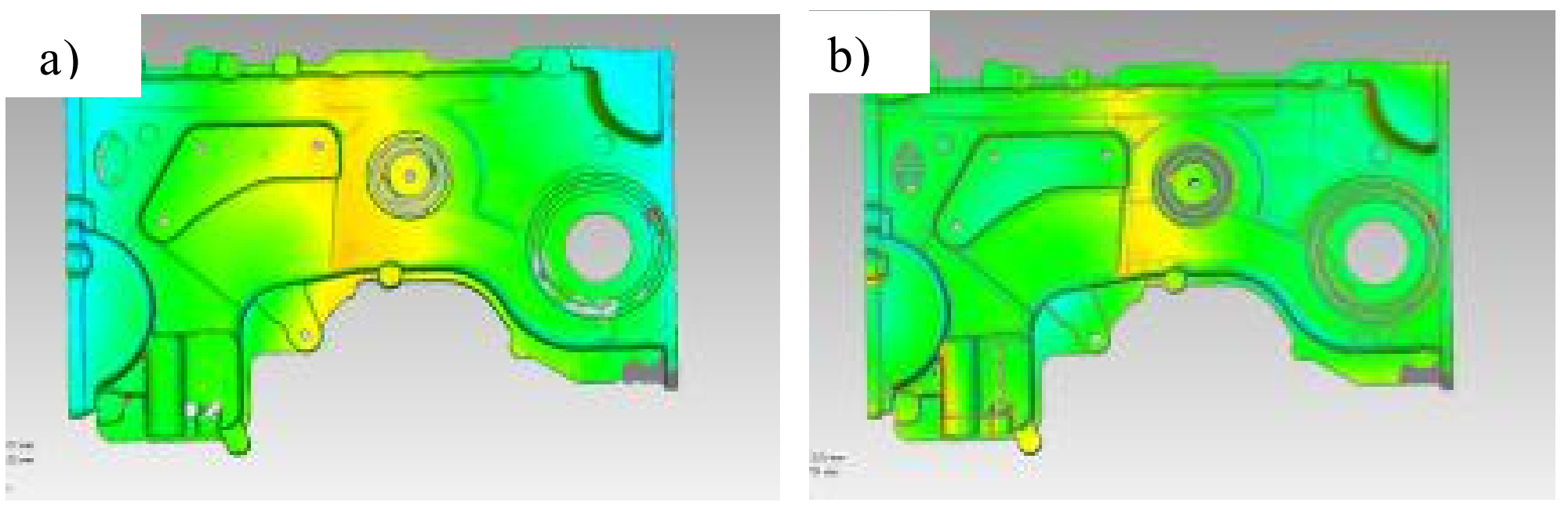
2. Shell making and pouring
Laser sintering wax mold contains PS powder matrix, which is different from general precision casting wax. It has the following characteristics: high melting point and non fixed, and the melting process is long; The viscosity is large, and it needs a high temperature to reach the viscosity that can be dewaxed, which exceeds the dewaxing temperature of conventional boiling or steam process; Therefore, it needs to be decomposed in the roasting process, but a certain amount of ash residue will remain after decomposition.
The pouring process of sand mold casting adopts the method of vacuumizing first and then pressurizing in the vacuum tank. Vacuumizing can solve the problems of insufficient pouring and pores caused by suffocation in the pouring process. Pressure solidification can improve the feeding capacity of the casting riser by increasing the solidification pressure, so as to reduce the risk of shrinkage porosity and casting defects of sand castings, and improve the microstructure compactness of sand castings. The vacuum degree used for sand casting pouring is -0.06mpa, the pressurization pressure is 0.5MPa, and the pressure is maintained for 600s. The obtained sand castings are shown in Figure 3. There are slight bumps on the surface of sand castings. After manual grinding and cleaning, the surface quality meets the service requirements of sand castings.
3. Inspection of sand castings
Fig. 4 shows the three-dimensional scanning dimension test results of the cover sand mold casting. Most of the dimension deviations are within the range of ± 0.3mm, and some dimensions are between ± 0.3mm – ± 0.5mm.
The castings are tested by industrial CT, and some results are shown in Fig. 5. Most of the internal quality of sand castings is good, and pinholes only appear in the local position of the large plane, but it is better than the pinhole defect of the die-casting process cover, which meets the quality requirements of trial sand castings.
Sample number | Tensile strength / RM (MPA) | Hardness (HBW) | Elongation A / (%) |
1# | 171 | 86.0 | 1.5 |
2# | 163 | 89.0 | 2.0 |
The test results of mechanical properties of cover sand casting samples are shown in the table, and the metallographic matrix structure analysis is α Solid solution + rod eutectic silicon, as shown in Figure 6.