The pump cover developed by sand casting manufacturers is one of the key components of marine dredging pumps. Its function is to form a relatively sealed chamber together with the volute, guiding the medium from the inlet to the impeller, collecting the medium thrown out by the impeller, and then guiding the collected medium to the outlet, forming a complete working path. The key points are the matching surfaces between the pump cover, volute, and protective plate. It is required that sand casting manufacturers develop cast steel pump covers without defects such as shrinkage holes, looseness, and inclusions. The quality of these key surfaces is the key to the development of cast steel pump covers, and it is also a technical difficulty for sand casting manufacturers to develop cast steel pump covers.
1.Main technical requirements and casting process analysis
1.1 Product Structure and Main Technical Requirements
The structure of the pump cover casting developed by the sand casting manufacturer is shown in Figure 1, with a maximum diameter size of nearly 2600 mm and a height of nearly 260 mm (excluding the foot). The key fitting position is on the outer circular surface and end face below the foot, and the material is ZG270-500. The chemical composition and mechanical properties are shown in Tables 1 and 2.
C | Si | Mn | Ni | Cr | Mo | P | S |
0.35~ 0.40 | 0.45~ 0.50 | 0.60~ 0.90 | 0.26~ 0.30 | 0.30~ 0.35 | 0.15~ 0.20 | ≤0.04 | ≤0.04 |
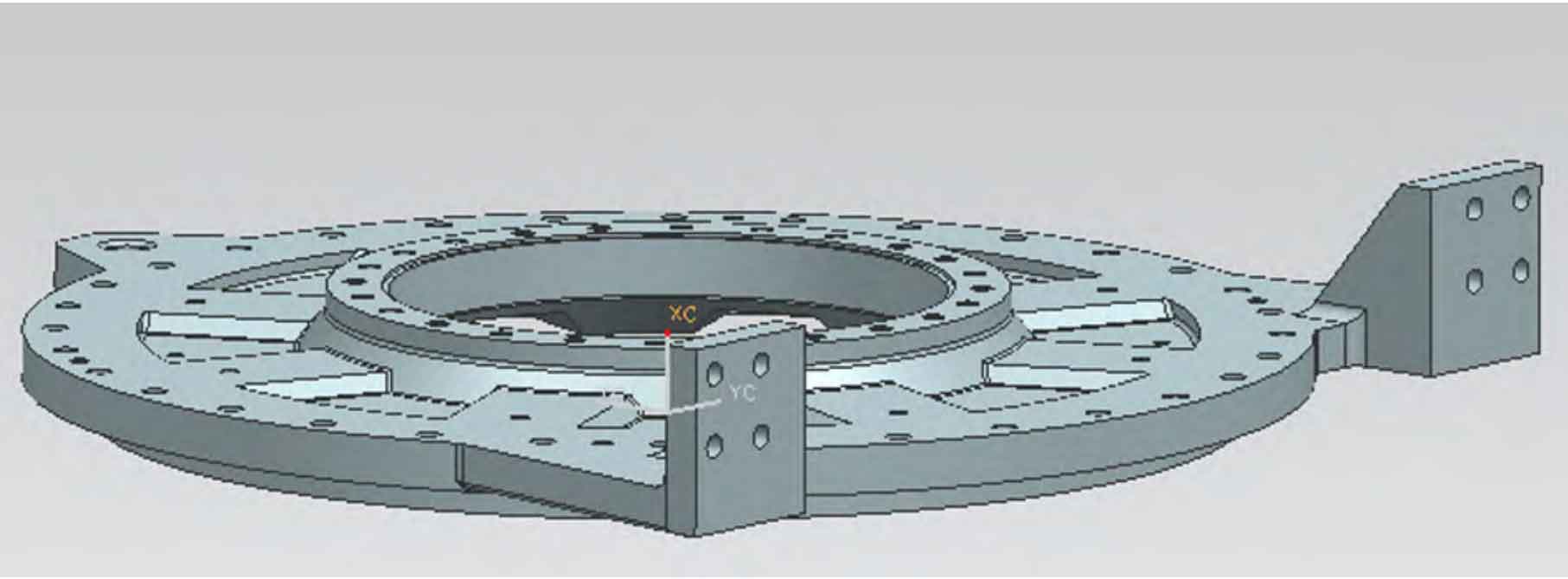
Tensile strength Rm/MPa | Yield strength Rp/MPa | Elongation after fracture A/% | Impact absorption energy Akv/J | Brinell hardness (HBW) |
≥500 | 270 | ≥18% | ≥27 | 217~255 |
1.2 Casting process analysis of pump cover castings
1) The sand casting manufacturer has developed a pump cover as a plate type casting with uneven wall thickness, with a maximum thickness of 180 mm and a minimum thickness of 80 mm. The hot joints are relatively dispersed, and a riser must be installed at each concentrated point to prevent shrinkage or porosity defects.
2) The main body of the pump cover castings developed by sand casting manufacturers is presented as a plate structure, with bottom feet designed on both sides of the maximum outer circle. The wall thickness difference around the middle inner hole is 80mm, and the hot spots are concentrated. There is a problem of insufficient shrinkage channels, and subsidies must be appropriately increased.
3) Sand casting manufacturers have developed pump cover steel castings with special structures and large dimensions. They now adopt the method of false box modeling for process design.
4) The sand casting manufacturer has developed a pump cover cast steel component made of medium carbon cast steel, which has certain toughness and plasticity, high strength and hardness, good cutting performance, and acceptable weldability.
5) In order to ensure the quality of the key mating surface of the pump cover, sand casting manufacturers place the key mating surface on the lower box during process design, and place a heating riser above it for shrinkage filling; When designing the tooling, increase the casting fillet at the root of the outer circular surface to prevent sand sticking.
Therefore, sand casting manufacturers must consider the influence of the above factors in the production process of pump cover castings.
2. Casting process design of pump cover steel castings
Due to the uneven wall thickness and dispersed hot spots of pump cover products developed by sand casting manufacturers, it is difficult to supplement and shrink them. Therefore, it is necessary to ensure their internal quality through reasonable casting process design to meet usage requirements. Design a reasonable riser and take measures such as increasing subsidies and tilting pouring to ensure its quality, avoiding casting defects as much as possible and reducing welding. Considering the high tendency of inclusions and sand sticking in castings, it is necessary to increase the casting fillet as much as possible without affecting the use of the castings.
2.1 Casting process
The sand casting manufacturer has developed a pump cover casting process as shown in Figure 2, which adopts a resin sand casting false box molding method. The gating system uses the company’s proprietary gate type ceramic gating basin and a predetermined specification ceramic gating channel for double-sided drainage pouring. The riser is fed with an elliptical heating riser combined with a conventional riser to supplement the molten iron.
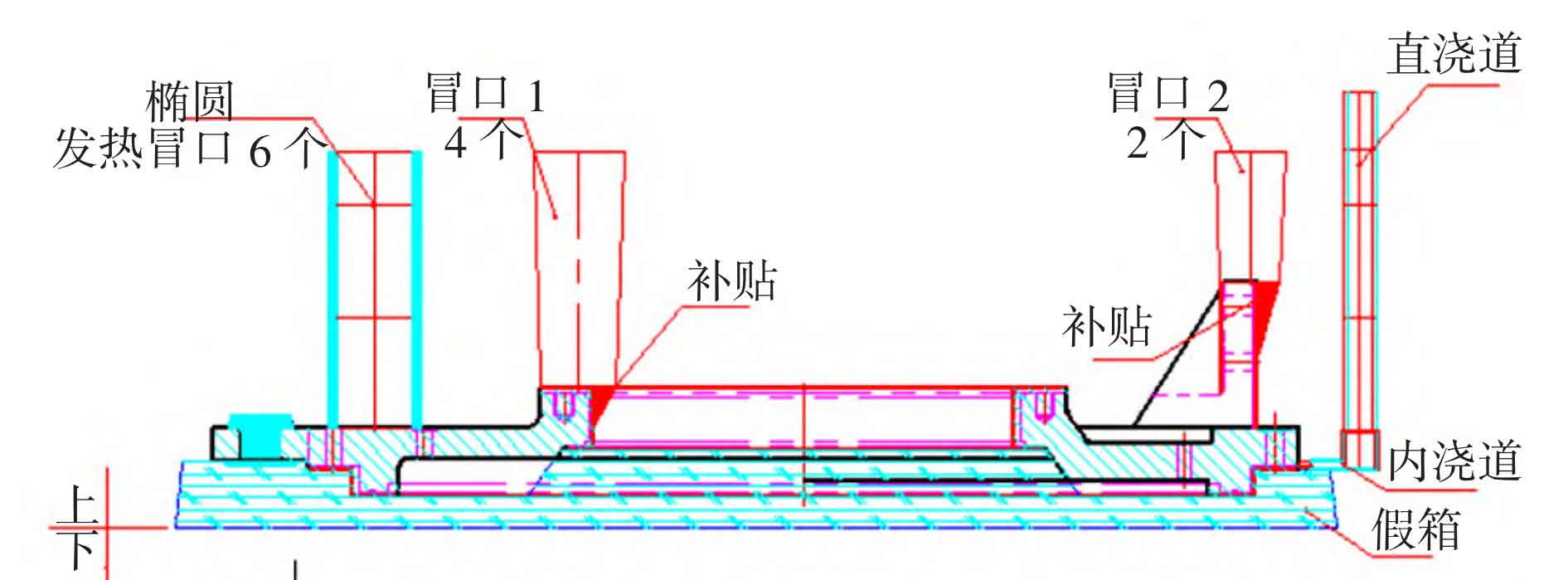
2.2 Pouring System Design
The principle of sand casting manufacturers in designing the pouring system is to ensure smooth filling and to quickly fill the mold cavity with molten steel to prevent casting defects such as air entrainment, oxide formation, and cold shut. The open pouring system has a smoother filling process and less flushing force on the mold cavity, which can prevent damage to the mold. The bottom pouring type internal runner can ensure smooth filling of the casting, rapid rise of steel liquid in the mold cavity, and no turbulence, therefore, the bottom pouring type internal runner is adopted.
The blocking area of the open gating system is designed according to the empirical formula provided in the casting manual. The ratio of the cross-sectional areas of each component in the open gating system is F straight: F horizontal: F internal=1: (1.2-2): (1.2-2). The specifications selected from the ZHY Castig proprietary ceramic gating size series are: φ 110 vertical sprue, 100 mm x 120 mm horizontal sprue, and 10 15mm x 60 mm internal sprues (single side). Due to the large size of the pump cover steel castings developed by sand casting manufacturers, the amount of molten iron used exceeds the capacity of a single ladle, and the main body is a plate type casting, a double-sided ladle tilting pouring method is adopted.
2.3 Riser design
There are various factors that affect the effect of riser shrinkage during the production process of pump cover steel castings by sand casting manufacturers, such as casting material, pouring temperature, pouring speed, casting structure, and riser placement position.
According to the structural characteristics of pump cover steel castings developed by sand casting manufacturers, the hot spot is mainly concentrated in two areas: one is the junction between the minimum inner circle and the flat plate, and the other is the T-shaped structure between the flat plate and the volute seal. Risers must be set up at each hot spot for shrinkage, as shown in Figure 2.
To simplify the calculation, both hot nodes can be considered as plate joints, forming a circle with a modulus equal to the radius of the hot node circle.
The modulus of the riser: M riser=(1-1.2) M pieces, so the specific size of the riser can be calculated. Riser 1 has a size of 200/300/500, Riser 2 has a size of 160/240/350, and the elliptical heating riser is selected as FT100-200/300/300
2.4 Subsidy design
To obtain castings with high density, if the feeding distance in the vertical direction of the riser cannot be reached, a subsidy should be set below the riser to ensure smooth directional solidification and feeding channels. However, due to the structural characteristics of pump cover steel castings developed by sand casting manufacturers, whether it is at the highest foot or the highest end face of the casting, it is necessary to artificially add a certain thickness of subsidy on the casting under the riser. The casting process is shown in Figure 3.
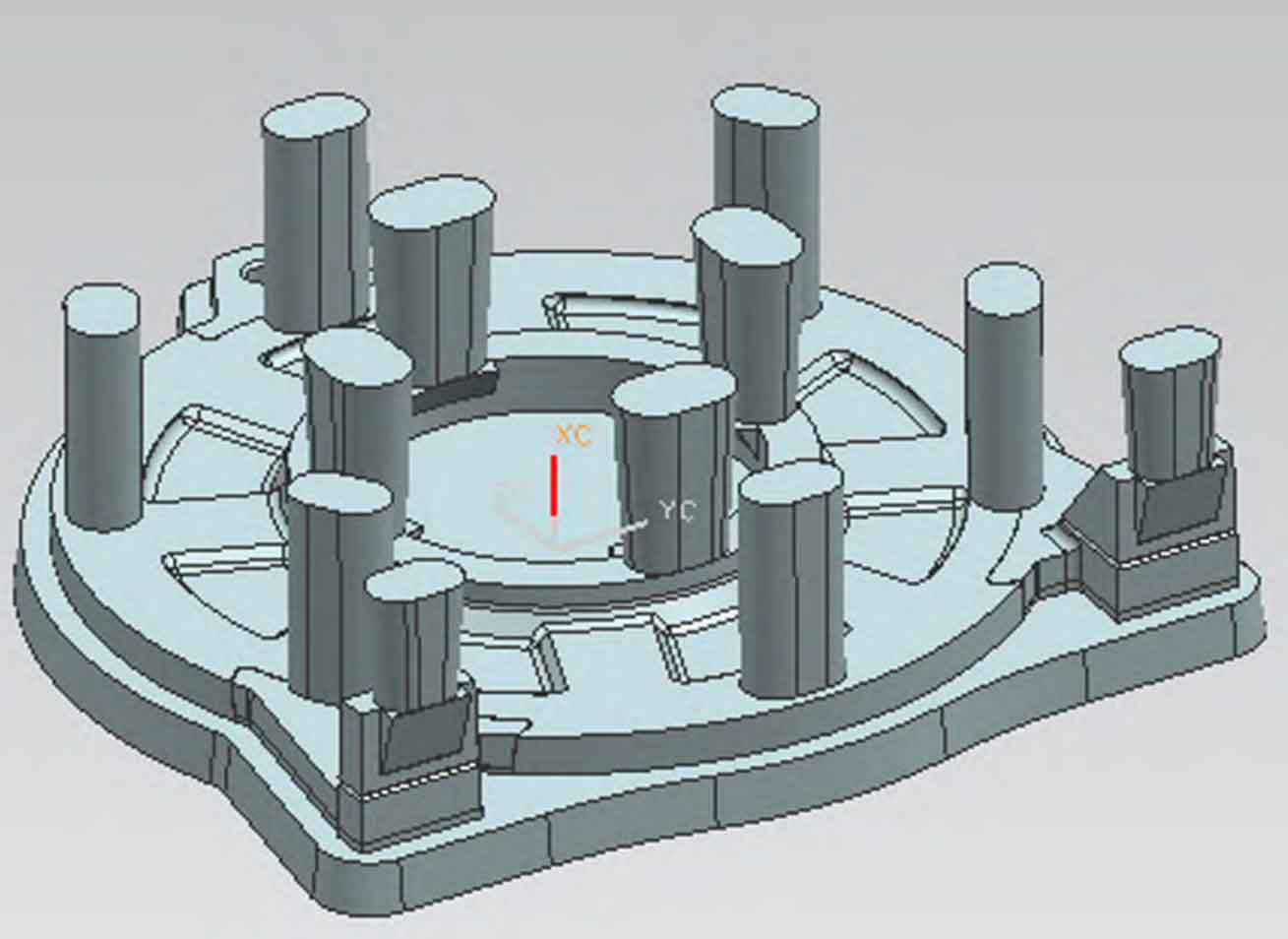
2.5 Solidification simulation analysis
Solidification simulation was conducted on the casting process plan of pump cover steel castings developed by sand casting manufacturers using CASTsoft casting simulation software. The calculation conditions for the pre-processing setting of numerical simulation are: the casting material is selected as ZG270-500; The casting material is furan resin sand; Pouring temperature: 1530 ℃; The initial temperature of the sand mold is 20 ℃; The heat transfer coefficient of castings/molds is C1000.0, the heat transfer coefficient of castings/air is C500, and the heat transfer coefficient of molds/air is C1000; The rest use software default values; The critical value of the shrinkage criterion function is set to 99.9999. The solidification simulation and shrinkage prediction results were obtained through numerical simulation. The solidification simulation and shrinkage prediction results are shown in Figures 4 and 5, indicating that there will be no casting defects such as shrinkage cavities and shrinkage porosity inside the products produced by this process.
3. Production practice
This casting process plan abandons the previous process design ideas and uses the process of cast iron fixtures with real samples and fake box shapes to produce the first pump cover cast steel part. The blank weight is 5000 kg, the amount of molten iron used is 7600 kg, and the process yield is 65.8% According to the aforementioned heat treatment process, the mechanical properties Rm=620 MPa, Rp=320 MPa, A ≥ 19.4%, Akv ≥ 28 J, and hardness of 235 HBW all meet the technical requirements. During the processing, there are no casting defects such as shrinkage holes and porosity on each processing surface of the casting, indicating that the process is reasonable and effective.
The problems that are prone to occur during the production process include:
1) Adhesive sand: Due to the high pouring temperature of steel castings, the mixing and brushing quality of coatings must be strictly carried out in accordance with the requirements of the process documents to ensure that the brushed surface does not bubble or crack; All corners and contour intersections must have rounded transitions, and the rounded corners should be as large as possible; When shaping, it is not easy to sand and compact near the riser and the root of the rounded corner. The sand mold has low strength and is prone to sand sticking defects. It is necessary to lay a certain thickness of chromium ore sand at the root of the riser and the root of the rounded corner to prevent sand sticking defects.
2) Shrinkage and loosening: Sand casting manufacturers develop pump cover steel castings with uneven wall thickness and scattered hot spots, which are prone to shrinkage or loosening casting defects. By increasing subsidies, increasing risers, and placing heating risers in key matching positions, process measures are taken to ensure sufficient shrinkage channels and liquid supply to prevent shrinkage or loosening defects.
4. Conclusion
1) Using modulus theory to design the casting process for large cast steel pump covers and using CASTsoft casting simulation software for solidification simulation verification, the pump cover steel castings produced by sand casting manufacturers have no casting defects such as shrinkage cavities and porosity.
2) The fake box molding process is a type of traditional resin sand molding process, suitable for mass production of castings that require sand excavation. In actual production, it eliminates the molding process of sand core drilling, brushing sand core, and flipping the box to lower the core, simplifying the molding process and reducing the probability of problems. At the same time, it provides strong assurance for the quality of pump cover steel castings developed by sand casting manufacturers.