Chapter 1: Mastering Sand Casting Part for Automotive
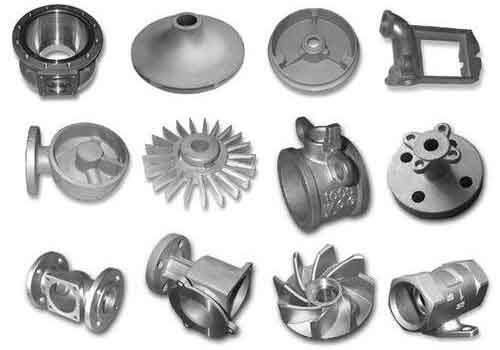
Mastering the art of sand casting part for automotive parts involves several key steps and considerations. Sand casting part a widely used method in the manufacturing of automotive parts due to its cost-effectiveness and ability to produce large, complex parts. Here’s a brief overview of the process and some important points:
- Design and Pattern Making:
- The first step is to create a design for the part you want to manufacture.
- A pattern is then made, typically from wood, metal, or plastic, which represents the external shape of sand casting part.
- Mold Preparation:
- Sand casting part involves creating a mold made of sand.
- The sand is mixed with a binding agent like clay and water.
- The prepared sand mixture is then packed around the pattern in a flask.
- Creating the Cavity:
- After the sand hardens, the pattern is removed, leaving a cavity in the shape of the part.
- Pouring the Metal:
- Molten metal is poured into the cavity of the sand mold.
- Common metals used include iron, steel, aluminum, and bronze.
- Cooling and Solidification:
- After pouring, the metal is allowed to cool and solidify within the mold.
- Mold Breakage and Removal of Casting:
- Once the metal has solidified, the sand mold is broken to retrieve the sand casting part.
- The part may still require further processes like sandblasting to remove any residual sand.
- Finishing:
- The sand casting part often subject to additional processes like machining, grinding, and finishing to achieve the desired dimensions and surface quality.
- Quality Control:
- Quality control is crucial. Inspections are conducted to ensure the part meets all specified dimensions, strength, and quality requirements.
- Environmental and Safety Considerations:
- Proper handling of materials and waste, as well as ensuring worker safety, are essential aspects of the process.
- Cost-Effectiveness and Efficiency:
- Sand casting part is generally more cost-effective for producing large, complex parts in relatively low quantities.
- Adapting to Modern Technologies:
- Technologies like 3D printing are now being used to create more precise and intricate patterns and molds, improving the efficiency and capabilities of sand casting part.
In the automotive industry, this process is commonly used for producing engine blocks, cylinder heads, manifolds, and other large, complex components. As with any manufacturing process, continuous improvement and adherence to quality standards are key to mastering sand casting part in the automotive sector.
Chapter 2: The Advancements in Sand Casting part for Machine
Recent advancements in sand casting part for machine parts focus on improving the process’s efficiency, quality, and environmental impact. Some of the key developments are:
- Squeeze Casting: This technique combines casting and forging methods. The metal is solidified under pressure, leading to a pore-free fine grain casting with properties similar to wrought materials. The application of pressure significantly reduces defects like porosity and shrinkage holes, and experiments have shown improvements in product hardness and mechanical properties.
- Sand Casting Improvements: Despite being an ancient technique, sand casting part has seen significant advancements. Modern sand casting part involves phases like alloying, molding, pouring, hardening, and finishing. There’s a focus on recycling sand, which is both cost-effective and environmentally friendly. Additive manufacturing (3D printing) has also been introduced to speed up production, reduce shrinkages, and enable the creation of more intricate components, like thin walls in automobile cylinder heads. However, challenges remain, such as ensuring uniform sand flow in 3D printing for optimal results.
- Investment Casting: Known for producing parts with excellent precision, investment casting involves creating patterns (often with wax) which are then invested into a ceramic slurry to create a mold. Recent advancements include the use of colloidal silica sol binders, which are more stable and capable of withstanding high temperatures, leading to more durable molds and the ability to create complex parts with high precision.
- Application of Artificial Intelligence (AI): AI is playing a significant role in enhancing various casting processes, including sand casting part. By using techniques like artificial neural networks, genetic algorithms, and fuzzy logic, AI can optimize the design of sand casting part systems, improve process control, and predict maintenance needs. This integration is a step towards the realization of ‘smart foundries,’ a key aspect of Industry 4.0.
These advancements not only enhance the efficiency and quality of the sand casting part but also align it with modern industrial demands and environmental standards.
Chapter 3: Basics and Benefits for Sand Casting Part Manufacturing
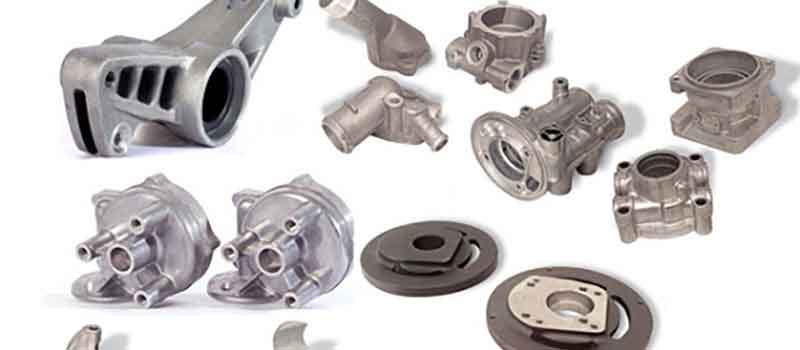
Sand casting part is a widely used process in manufacturing parts across various industries, owing to its simplicity, versatility, and economic efficiency. Let’s go through the basics and benefits of this method:
Basics of Sand Casting Part
- Process Overview:
- Pattern Making: A pattern, usually made of wood or plastic, is created to resemble the part to be cast. This pattern is slightly larger than the final part to account for shrinkage of the metal as it cools.
- Molding: Sand is mixed with a binder and packed around the pattern in a molding box. The sand hardens into the shape of the part.
- Core Making: If the part has internal cavities or undercuts, a sand core is made and placed in the mold cavity.
- Pouring: Molten metal is poured into the mold, filling the cavity and encapsulating the core if present.
- Cooling: The metal solidifies within the sand mold.
- Mold Breakaway: The sand mold is broken away, and the cast part is removed. The sand can often be recycled for future casts.
- Finishing: The part may require cleaning, grinding, machining, or other finishing processes to achieve the desired dimensions and surface finish.
- Materials:
- Common metals include iron, steel, aluminum, bronze, and brass.
- The sand is often a mixture of silica, clay, and water, though other compositions can be used.
Benefits of Sand Casting Part
- Versatility:
- Suitable for a wide range of metal alloys.
- Capable of producing complex geometries and large parts.
- Cost-Effectiveness:
- Relatively inexpensive tooling and equipment compared to other casting methods.
- The sand used can be recycled, reducing material costs.
- Low Volume Production:
- Ideal for small to medium production runs.
- Easy to change and modify designs between casts, offering flexibility in production.
- Tolerates High Melting Temperatures:
- Sand withstands high temperatures, making it suitable for sand casting part metals with high melting points.
- Rough Surface Finish and Tolerance:
- While the surface finish is rougher compared to other methods, it’s often acceptable for many applications. Precision machining can improve the finish if needed.
- Large Part Capability:
- Can produce very large parts that might be challenging or expensive to create with other methods.
Limitations
While there are many benefits, sand casting part also has limitations such as rough surface finish, lower dimensional accuracy compared to other casting methods, and a slower production rate.
In conclusion, sand casting part remains a valuable and versatile option in manufacturing, particularly suited for producing complex shapes and large parts in smaller production volumes at a lower cost.
Chapter 4: Utilizing Sand Casting Part for Industrial Creation
Utilizing sand casting part for industrial part creation is a common practice due to its versatility and cost-effectiveness. This method is particularly well-suited for industries where robust, large, and metal components are required. Let’s explore how sand casting part is used in various industrial contexts:
Industries Benefiting from Sand Casting Part
- Automotive Industry:
- Produces engine blocks, cylinder heads, manifolds, and other large parts.
- Ideal for both prototype development and full-scale production.
- Aerospace Industry:
- Used for casting part like turbine housings, engine components, and landing gear parts.
- The ability to cast high-strength, heat-resistant alloys is essential in this sector.
- Heavy Machinery and Equipment:
- Sand casting part is used for creating large parts like frames, gears, and components for construction and agricultural machinery.
- Marine Industry:
- Produces parts like propellers, ship engine parts, and other components exposed to corrosive marine environments.
- Rail Industry:
- Useful for making large, sturdy components such as railway wheels, undercarriage parts, and couplings.
- Energy Sector:
- Creates components for wind turbines, gas turbines, and parts for nuclear, hydro, and thermal power plants.
Advantages of Sand Casting Part in Industrial Creation
- Customization and Complexity:
- Sand molds can be tailored to complex shapes and sizes, offering a high degree of design flexibility.
- Material Diversity:
- Accommodates a wide range of metals and alloys, making it suitable for various industrial applications.
- Economical for Low to Medium Volume Production:
- Cost-effective for small batches, which is beneficial for custom or specialized industrial components.
- Scalability:
- While optimal for small to medium production runs, it can be scaled up for larger volumes if needed.
- Rapid Prototyping:
- Quick turnaround from design to production, which is crucial for prototyping and testing in industries like automotive and aerospace.
Considerations
- Quality Control: Industrial applications often demand high-quality standards. Regular checks are necessary to ensure that the sand casting part meet the required specifications.
- Finishing Processes: Depending on the application, additional machining and finishing may be needed to achieve the desired tolerances and surface finish.
- Environmental Impact: Attention to environmental impacts, particularly in sand disposal and recycling, is important.
Conclusion
Sand casting part as a foundational manufacturing process in the industrial sector, offering flexibility in design, material choice, and cost efficiency. It plays a crucial role in producing a variety of essential components across numerous industries, underscoring its enduring relevance in modern manufacturing.
Chapt 5: The Impact of Sand Casting Part in Manufacturing
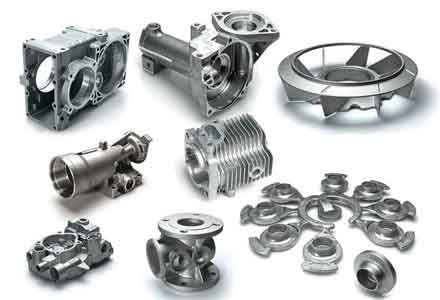
Sand casting part has a significant impact on the manufacturing industry, affecting various aspects from production capabilities to economic considerations. Understanding these impacts is crucial for businesses and manufacturers who rely on this process.
1. Economic Impact
- Cost-Effective Production: Sand casting part is one of the most economical casting methods, particularly for small to medium-sized production runs. The low cost of mold materials and relatively simple equipment required make it a financially viable option for many manufacturers.
- Versatility in Materials and Products: This method is not limited to specific metals, allowing manufacturers to work with a wide range of alloys. This versatility can lead to cost savings and the ability to meet diverse market demands.
2. Design and Flexibility Impact
- Complex Geometries: Sand casting part can produce parts with complex internal and external geometries that might be difficult or impossible to achieve with other manufacturing processes.
- Size Range: It’s suitable for producing very small to extremely large parts, offering a range of capabilities that many other casting methods can’t match.
3. Production and Efficiency Impact
- Speed of Production: While not as fast as some high-volume production methods, sand casting part is relatively quick, especially when it comes to setting up the process and producing the first few units.
- Prototyping and Customization: It’s excellent for prototyping due to the ease of altering mold designs, allowing for rapid iteration and customization.
4. Quality and Performance Impact
- Material Properties: Sand casting part can maintain the mechanical properties of the cast metal, which is critical in applications where strength, ductility, and resistance to wear and tear are essential.
- Surface Finish and Tolerances: Parts typically have a rougher surface finish and lower dimensional accuracy compared to other casting methods. This can be a drawback for applications requiring high precision, although secondary machining processes can rectify these issues.
5. Environmental and Sustainability Impact
- Resource Utilization: Sand casting part uses materials that are abundant and often recyclable, contributing to sustainable manufacturing practices.
- Energy Consumption: Generally, it requires less energy compared to high-precision manufacturing processes, which can be beneficial from an environmental standpoint.
6. Technological Advancements and Future Prospects
- Incorporation of Modern Technologies: Advancements in areas like 3D printing of sand molds and improved materials for binders and cores are pushing the boundaries of what can be achieved with sand casting part.
- Future Trends: The continued integration of technology could lead to greater precision, reduced waste, and even more complex geometries, keeping sand casting part relevant in modern manufacturing.
Conclusion
Sand casting part plays a crucial role in the manufacturing industry due to its cost-effectiveness, flexibility, and versatility. While it has some limitations in terms of surface finish and dimensional accuracy, its ability to produce complex shapes and large components makes it indispensable for many applications. Moreover, ongoing technological improvements are likely to enhance its capabilities and efficiency, ensuring its continued impact on the manufacturing sector.
Chapter 6: Sand Casting part for High-Precision Techniques
Using sand casting part for high-precision techniques presents a unique challenge, as traditional sand casting part is known more for its cost-effectiveness and versatility than for achieving high precision. However, advancements in the field have led to improved methods that can enhance the precision of sand casting part. Let’s explore these techniques and how they’re being applied:
1. Improved Sand Quality and Binders
- High-Quality Sand: Using finer and more uniform sand grains can lead to better surface finishes and more accurate castings.
- Advanced Binders: Modern chemical binders can help in achieving tighter control over the sand mold’s stability and permeability.
2. Precision Sand Molding Techniques
- 3D Printed Sand Molds: Utilizing 3D printing technology to create sand molds allows for more complex and precise geometries than traditional mold-making methods.
- Controlled Molding Processes: Processes like vacuum molding and precision sand casting part techniques can lead to better mold integrity and dimensional accuracy.
3. Use of Chills and Cores
- Chills: Inserting metal chills in the mold can help control the cooling rate of the metal, leading to a finer grain structure in the cast part, which can improve mechanical properties and precision.
- Advanced Cores: Precisely made cores can greatly improve the internal geometry of cast parts.
4. Secondary Machining and Finishing
- CNC Machining: Often, parts cast through sand casting part will undergo CNC machining to achieve the required dimensions and tolerances.
- Surface Finishing Techniques: Various techniques like grinding, polishing, and shot blasting are used to improve the surface finish of the cast parts.
5. Process Control and Quality Assurance
- Tight Process Control: Controlling every aspect of the sand casting part, from sand preparation to pouring, can result in more consistent and high-precision parts.
- Quality Checks: Using advanced inspection methods like X-ray or CT scanning ensures that the internal and external dimensions meet the required specifications.
6. Alloy Selection
- Material Choice: Some alloys have better flow and solidification characteristics, which can lead to more precise castings.
Conclusion
While traditional sand casting part may not be the first choice for high-precision parts, with the integration of modern technologies and advanced techniques, it is increasingly being used for applications that require higher levels of precision. This evolution broadens the scope of sand casting part, making it a more versatile choice in the manufacturing world. However, it’s important to balance the need for precision with the inherent limitations and cost implications of these advanced techniques.
Chapter 7: Exploring the Versatility of Sand Casting part in Custom Production
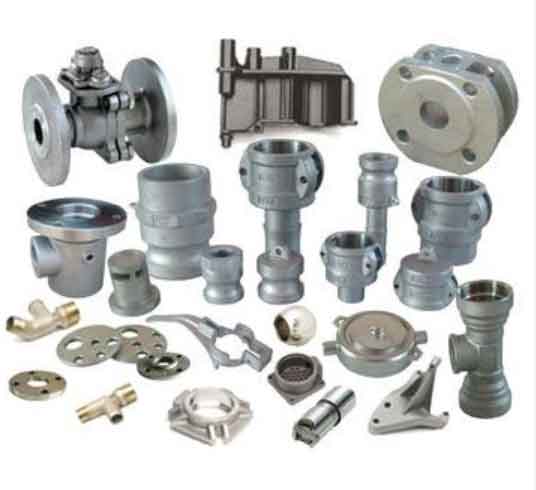
Sand casting part’s versatility makes it highly suited for custom production, offering a unique combination of flexibility, cost-effectiveness, and the ability to handle a wide range of materials and sizes. This makes it an attractive option for industries requiring bespoke parts or limited production runs. Let’s explore the aspects that make sand casting part so adaptable for custom manufacturing:
1. Design Flexibility
- Complex Geometries: Sand casting part can produce parts with intricate designs and complex internal structures that might be challenging to achieve through other manufacturing processes.
- Size Range: It can accommodate a wide range of part sizes, from small components to large industrial pieces.
2. Material Versatility
- Wide Range of Alloys: Sand casting part is not limited to specific metals, allowing manufacturers to work with various materials including iron, steel, aluminum, bronze, brass, and more, depending on the requirements of the custom part.
- Material Properties: Different alloys can be selected to meet specific strength, weight, corrosion resistance, or thermal properties.
3. Mold Making and Adaptability
- Ease of Mold Creation: Creating sand molds is relatively straightforward and cost-effective, allowing for quick adaptation to new designs.
- Prototype Development: This adaptability makes sand casting part ideal for prototyping, as molds can be rapidly produced and modified based on testing and feedback.
4. Cost-Effectiveness
- Economical for Small Batches: Sand casting part is particularly cost-effective for custom production and small to medium production runs, as it doesn’t require expensive tooling like some other manufacturing processes.
- Reduced Lead Times: The simplicity of the process can lead to shorter lead times, which is crucial for custom projects with tight schedules.
5. Secondary Operations
- Machining and Finishing: Custom parts may require precise tolerances and finishes. Sand cast parts can easily be machined, ground, or polished to meet specific requirements.
6. Application in Various Industries
- Automotive and Aerospace: For prototype parts or limited-run components.
- Art and Decorative Items: Custom sculptures and decorative pieces can be created.
- Machinery and Equipment: Custom gears, housings, and components for specialized machinery.
Conclusion
Sand casting part’s combination of flexibility in design, material selection, and cost efficiency makes it an ideal choice for custom production. Its ability to produce complex shapes and accommodate a wide range of sizes and materials allows manufacturers to meet specific and unique requirements of custom projects. As technology continues to evolve, incorporating advancements like 3D printed molds and precision casting techniques, sand casting part’s role in custom manufacturing is likely to expand even further.
Chapter 8: Advanced Sand Casting part Methods for Complex
Advanced sand casting part methods have evolved to address the demand for more complex and precise castings. These methods incorporate innovative techniques and technologies, enhancing the traditional sand casting part process to achieve higher accuracy, better surface finishes, and more intricate geometries. Let’s delve into some of these advanced methods:
1. 3D Printed Sand Molds
- Technology Integration: Utilizing 3D printing technology for creating sand molds allows for the production of highly intricate and complex shapes that would be difficult or impossible with traditional molding techniques.
- Design Flexibility: This method supports rapid prototyping and customization, enabling the quick transition from design to production.
2. Precision Sand Casting Part
- Tight Tolerances: Specialized techniques in sand preparation, mold making, and pouring are employed to achieve tighter dimensional tolerances than standard sand casting.
- Improved Surface Finish: These methods can result in a smoother surface finish, reducing the need for extensive post-casting machining.
3. Chemically Bonded Sand Systems
- Enhanced Mold Stability: Using chemical binders in the sand mixture improves the mold’s stability and strength, allowing for the production of more detailed and precise castings.
- Better Accuracy and Finish: These systems often result in higher accuracy and improved surface finishes compared to traditional green sand casting.
4. Controlled Solidification Techniques
- Directional Solidification: Managing the cooling and solidification process can reduce internal stresses and defects in the casting, leading to higher quality and strength.
- Use of Chills: Inserting metal chills in the sand mold can control the cooling rate, resulting in a finer grain structure and improved mechanical properties.
5. Vacuum Sand Casting Part
- Reduced Defects: By creating a vacuum around the mold, this method can minimize air entrapment and turbulence during pouring, leading to fewer defects.
- Improved Mechanical Properties: Vacuum casting can produce parts with better mechanical properties and a denser structure.
6. Automated Sand Casting Part
- Robotic Automation: Employing robotics for tasks like sand mixing, mold making, and pouring enhances precision and consistency, leading to improved quality.
- Efficiency and Reproducibility: Automation can increase production efficiency and ensure more consistent results, especially beneficial for complex parts.
Conclusion
The advancements in sand casting part is tailored to meet the increasing demand for complex and high-quality castings in various industries. By incorporating technologies like 3D printing, precision techniques, and automation, manufacturers can achieve greater accuracy, better surface finishes, and intricate geometries, extending the capabilities of traditional sand casting part to new heights.
Chapter 9: Enhancing Quality and Efficiency in Sand Casting Part for Automotive
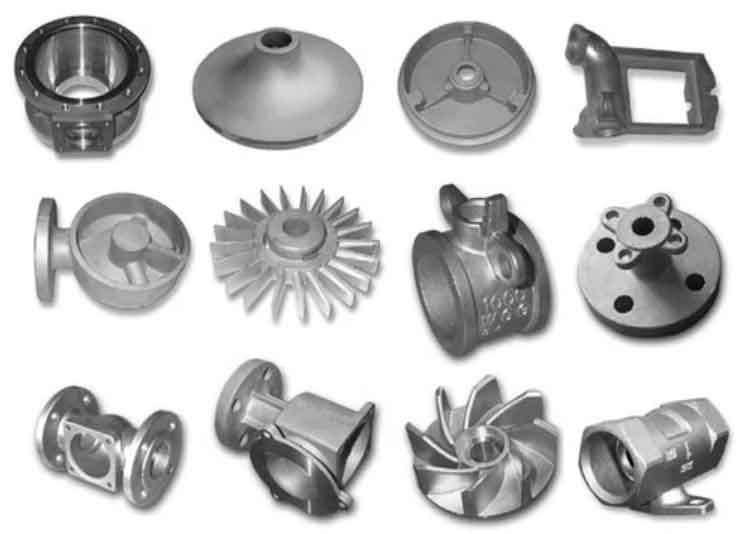
Enhancing quality and efficiency in sand casting part for automotive parts is crucial due to the industry’s high standards for durability, precision, and performance. Several strategies and technological advancements can be employed to achieve these objectives. Here’s how quality and efficiency in sand casting part for automotive components can be enhanced:
1. Advanced Mold Making Techniques
- 3D Printed Sand Molds: Utilizing 3D printing for mold making can significantly increase the precision of the molds, leading to better quality sand casting part with complex geometries.
- Computer-Aided Design (CAD): Employing CAD for mold design enhances accuracy and allows for quick alterations in design, reducing the time and cost involved in mold making.
2. High-Quality Materials
- Superior Sand and Binders: Using high-quality sand with appropriate grain size and advanced binders can improve the mold’s strength and surface finish of sand casting part.
- Specialized Alloys: Using alloys specifically designed for automotive applications can enhance the mechanical properties of the cast parts.
3. Process Control and Monitoring
- Automated Control Systems: Implementing automated systems for controlling and monitoring the casting process ensures consistent quality and reduces the likelihood of human error.
- Temperature and Pouring Control: Precise control over the temperature of the molten metal and the pouring rate can significantly impact the quality of the casting.
4. Post-Casting Treatments
- Heat Treatment: Applying heat treatments can improve the mechanical properties of cast parts, such as strength and ductility.
- Surface Finishing: Techniques like shot blasting, grinding, or machining can be used to improve surface finish and dimensional accuracy.
5. Quality Assurance Techniques
- Non-Destructive Testing (NDT): Employing methods like X-ray or ultrasound testing ensures internal quality without damaging the parts.
- Dimensional Inspection: Regular dimensional checks, using tools like CMM (Coordinate Measuring Machines), ensure that the parts meet the specified tolerances.
6. Lean Manufacturing Practices
- Waste Reduction: Implementing lean manufacturing techniques can help in reducing waste materials and optimizing resource usage.
- Efficient Workflow: Streamlining the workflow and reducing cycle times can increase overall production efficiency.
7. Environmental Considerations
- Recycling of Sand: Recycling the sand used in molds can minimize environmental impact and reduce costs.
- Energy-Efficient Practices: Adopting energy-efficient practices in melting and other processes can reduce the environmental footprint and operational costs.
Conclusion
In the automotive industry, where the demand for high-quality and efficient production is paramount, these strategies can significantly improve the outcomes of sand casting processes. By embracing technological advancements and optimizing production practices, manufacturers can meet the stringent requirements of automotive parts, ensuring reliability, performance, and sustainability.
Chapter 10: Cutting-Edge Innovations in Sand Casting Part for Aerospace Development
Sand casting part, a method of metal casting where sand is used as the mold material, has seen significant innovations, especially in aerospace development. Here are some of the cutting-edge advancements in this field:
- 3D Printing for Sand Molds: The integration of 3D printing technology has revolutionized sand casting part. It allows for the creation of complex geometries that are difficult or impossible to achieve with traditional methods. This innovation is particularly beneficial in aerospace, where parts often require intricate designs and high precision.
- Advanced Sand Materials: Research and development in sand materials have led to the creation of sands with better binding properties and thermal characteristics. These advances result in more accurate and durable molds, which is critical in aerospace applications where precision and reliability are paramount.
- Computer Simulation: Computer-aided engineering (CAE) software is now commonly used for simulating the sand casting part process. These simulations help in predicting mold filling, cooling rates, and the occurrence of defects. This predictive capability is essential in aerospace part development for minimizing waste and ensuring quality.
- Use of Robotics and Automation: Robotics and automation in sand casting part have led to improvements in consistency and efficiency. Automated systems can precisely control aspects of the casting part process, such as pouring rates and cooling, which is especially important for the consistent quality required in aerospace parts.
- Enhanced Quality Control Techniques: New quality control methods, such as real-time X-ray imaging and 3D scanning, have been employed to inspect sand-cast parts. These techniques allow for the detection of internal defects and ensure that the parts meet the stringent requirements of the aerospace industry.
- Environmentally Friendly Processes: Efforts have been made to make sand casting part more environmentally sustainable. This includes using recycled materials for molds and developing non-toxic binders. Such innovations are increasingly important as the aerospace industry moves towards greener manufacturing processes.
- Alloy Development: Advances in metallurgy have led to the development of new alloys that can be effectively used in sand casting part. These alloys often have superior properties, such as higher strength-to-weight ratios, which are crucial in aerospace applications.
- Integration with IoT and Data Analytics: The integration of Internet of Things (IoT) sensors and data analytics in sand casting part processes allows for better monitoring and optimization of production. In aerospace, where every minor detail can impact performance and safety, such data-driven approaches are invaluable.
These innovations in sand casting part for aerospace development not only improve the efficiency and quality of the manufacturing process but also open up possibilities for more complex and reliable aerospace components.
Chapter 11:Navigating the Challenges of Sand Casting Part for Large-Scale Production
Navigating the challenges of sand casting part for large-scale production involves addressing several key factors to ensure efficiency, quality, and cost-effectiveness. Here are some strategies and considerations:
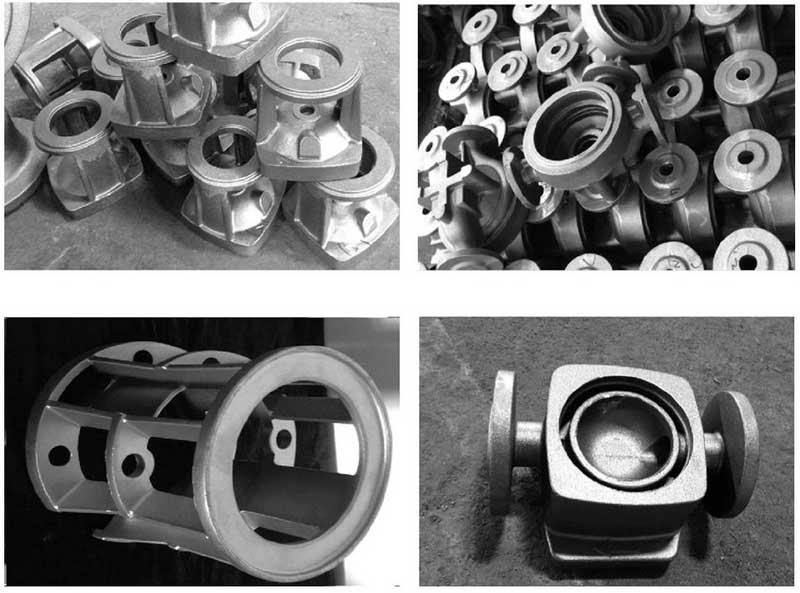
- Mold Material and Design: The quality of the mold material is crucial in sand casting part. For large-scale production, it’s important to use a sand mixture that can withstand repeated use without degrading. The mold design should also facilitate easy and quick removal of the cast part to speed up the production process.
- Pattern Making: Patterns must be precisely made and durable, especially for large-scale production. Consider using materials that can withstand wear and tear, and design patterns that simplify mold making and sand casting part.
- Automation and Process Control: Automation can greatly improve the efficiency and consistency of large-scale sand casting part. Automated molding machines, core making equipment, and conveyance systems can significantly speed up production while maintaining quality.
- Quality Control: Implement rigorous quality control measures to ensure that each cast meets the required standards. This may involve regular inspection of molds, patterns, and finished products.
- Casting Techniques: Optimize sand casting part techniques to suit large-scale production. This might include the use of continuous casting or other efficient methods that are suitable for the scale of your operations.
- Cooling and Finishing: For large-scale operations, efficient cooling and finishing processes are vital. Consider using automated methods for trimming, sandblasting, and finishing the casts.
- Workforce Training: Skilled operators and workers are essential. Ensure your workforce is well-trained in the specifics of large-scale sand casting part, including safety protocols and quality standards.
- Waste Management and Environmental Concerns: Large-scale production can lead to significant waste and environmental impact. Implement sustainable practices such as recycling used sand and minimizing emissions.
- Cost Management: Keep a close eye on costs, as large-scale production can quickly become expensive. This includes the cost of materials, labor, equipment maintenance, and any waste disposal fees.
- Adaptability and Scalability: Be prepared to adapt your processes and scale up or down as necessary, depending on market demand and other external factors.
Each of these areas requires careful planning and continuous improvement to ensure that your large-scale sand casting part operations are successful. Collaboration with experienced professionals and staying updated with the latest technologies and methods in the field can also provide valuable insights and advantages.
Chapter 12: The Role of Sand Casting Part in Modern Fabrication
Sand casting part is an essential and versatile process in modern fabrication. Here’s an overview of its role:
- Wide Range of Materials: Sand casting part is compatible with many metals, including iron, steel, aluminum, and bronze, making it highly versatile for different industrial applications.
- Cost-Effective for Large Parts: It’s particularly cost-effective for large sand casting parts, as the mold-making process is relatively inexpensive compared to other methods.
- Complex Geometries and Sizes: The process can create complex shapes that would be difficult or impossible to achieve with other methods. Sand molds can be made to almost any shape or size, suitable for producing a wide range of parts.
- Low Tooling Cost: Tooling costs in sand casting part generally lower than in other casting processes, making it a more economical choice for small to medium production runs.
- Short Lead Time: Sand casting part have shorter lead times compared to other methods, which is advantageous for projects with tight schedules.
- Prototyping and Customization: It’s a great choice for prototyping and custom manufacturing, as molds can be easily modified.
- Wide Industrial Applications: It’s used in various industries, including automotive, aerospace, construction, and machine manufacturing, for parts like engine blocks, machine tool beds, gears, and pulleys.
- Versatility in Quantity Production: Sand casting part suitable for both one-off projects and large production runs, providing flexibility in manufacturing scale.
Despite these advantages, there are limitations, like lower dimensional accuracy and surface finish compared to other methods, and the slower production rate for individual parts. However, ongoing advancements in sand casting part techniques, like improved sand quality and 3D printing of sand molds, are addressing these limitations, making it an ever-more crucial part of modern fabrication.