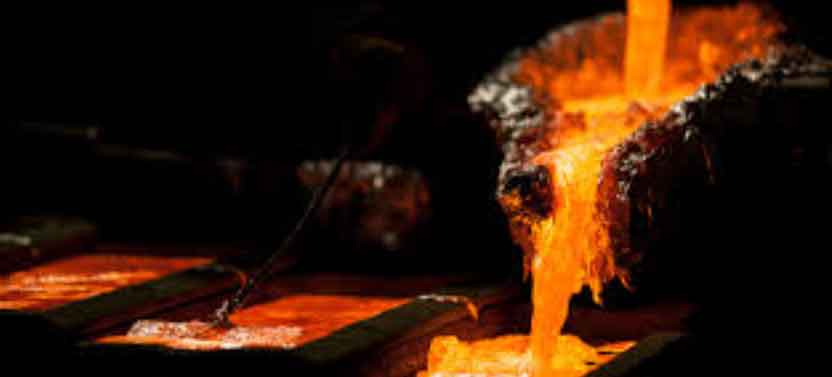
The sand casting process has a long history and is deeply rooted in traditional manufacturing practices. However, with modern manufacturing demands, it becomes crucial to balance tradition with advancements in technology and industry requirements. Here are some key considerations for striking this balance:
1.Design and Simulation Tools:
Utilize modern computer-aided design (CAD) software and simulation tools to optimize the design of castings, gating systems, and risers. These tools can help identify potential defects, predict solidification behavior, and optimize the process parameters before physical production begins. This integration of technology allows for improved efficiency and reduced trial-and-error.
2.Additive Manufacturing for Tooling:
Incorporate additive manufacturing (3D printing) techniques to produce complex and customized tooling components, such as patterns, cores, and molds. 3D printing allows for rapid prototyping, reduced lead times, and greater design flexibility. It can also help in the production of intricate geometries that are challenging to achieve with traditional methods.
3.Advanced Sand Mixtures:
Explore new sand mixtures and binders that offer improved dimensional accuracy, better surface finish, and enhanced collapsibility. These advanced materials can help reduce casting defects, improve mold strength, and minimize environmental impact. Additionally, automated sand mixing systems can ensure consistent properties and reduce variability in the sand casting process.
4.Real-time Process Monitoring:
Implement sensors and monitoring systems to capture real-time data during the casting process. These systems can track parameters such as temperature, pressure, and flow rates, allowing for immediate adjustments and proactive defect detection. Real-time monitoring enables process optimization, reduces scrap rates, and enhances overall quality control.
5.Robotics and Automation:
Integrate robotics and automation into sand casting operations to improve productivity and consistency. Automated systems can handle tasks like mold handling, pouring, and shakeout, reducing human error and enhancing efficiency. Robotics can also be used for quality inspection, ensuring accurate and consistent measurements.
6.Material Development and Control:
Focus on the development of new alloys and metal compositions specifically tailored for sand casting. Advanced metallurgical techniques and material characterization can enhance the mechanical properties, corrosion resistance, and overall performance of the castings. Additionally, precise control of melt temperature, composition, and treatment methods can optimize the casting process and minimize defects.
7.Environmental Considerations:
Address environmental concerns by implementing sustainable practices in sand casting. This includes utilizing eco-friendly binders, recycling sand, reducing energy consumption, and minimizing waste generation. Environmentally conscious manufacturing practices not only align with modern expectations but also contribute to the long-term viability and competitiveness of the industry.
8.Continuous Improvement and Training:
Foster a culture of continuous improvement and invest in employee training. Encourage innovation, knowledge sharing, and cross-functional collaboration within the sand casting team. Training programs can keep the workforce updated with the latest techniques, equipment, and industry trends, ensuring that they are well-equipped to balance tradition with modern manufacturing demands.
By embracing technological advancements, process optimization, and sustainable practices, sand casting can meet the demands of modern manufacturing without compromising the inherent benefits of this traditional casting method. Striking a balance between tradition and innovation allows for improved efficiency, higher quality, and enhanced competitiveness in the sand casting industry.