Ductile iron casting, also known as nodular iron casting or spheroidal graphite iron casting, has evolved significantly over time from a traditional material to a modern engineering solution. Let’s explore the evolution of ductile iron casting and its journey in the engineering field:
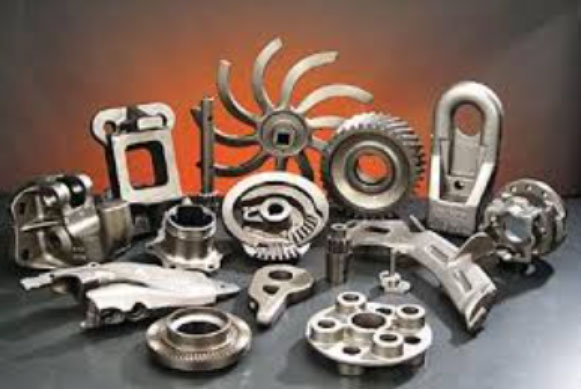
1. Discovery and Development: Ductile iron casting was first discovered in the 1940s by Keith Millis and his team at the International Nickel Company (INCO) in the United States. They found a way to introduce magnesium into molten iron, resulting in the formation of graphite nodules instead of flakes. This discovery revolutionized the properties and applications of cast iron, leading to the development of ductile iron casting.
2. Improved Microstructure: The development of ductile iron casting involved understanding and controlling the microstructure of the material. By adding small amounts of magnesium and other elements to molten iron, graphite nodules with a spherical shape formed instead of the typical flake-like graphite in grey cast iron. This modification improved the strength, ductility, and toughness of the material.
3. Advancements in Production Techniques: Over the years, advancements in production techniques and casting processes have contributed to the widespread adoption of ductile iron casting. Modern methods, such as sand casting, investment casting, and precision casting, have been developed to produce complex shapes and precise components with ductile iron.
4. Alloying and Heat Treatment: The properties of ductile iron casting can be further enhanced through alloying and heat treatment processes. Alloying elements like chromium, molybdenum, nickel, and copper can be added to improve specific properties such as corrosion resistance, wear resistance, and high-temperature strength. Heat treatment processes like quenching and tempering can also be applied to optimize the material’s mechanical properties.
5. Quality Control and Standardization: With the growing adoption of ductile iron casting in various industries, quality control and standardization have played a significant role in its evolution. International standards and specifications have been established to ensure consistent quality, dimensional accuracy, and performance of ductile iron castings, providing manufacturers and end-users with confidence in the material’s reliability.
6. Design Optimization: Ductile iron casting’s versatility and properties have led to design optimization in engineering applications. With improved understanding of its capabilities, engineers have been able to optimize component designs to take full advantage of the material’s strength, ductility, and other desirable properties. This has resulted in more efficient and cost-effective designs across industries.
7. Sustainable Practices: In recent years, the focus on sustainability and environmental impact has influenced the evolution of ductile iron casting. Efforts have been made to reduce the environmental footprint of the casting process, improve energy efficiency, and explore recycling and reuse of ductile iron scrap.
Today, ductile iron casting has become a widely used material in various engineering applications, including automotive, machinery, construction, power generation, and more. Its evolution from a traditional material to a modern engineering solution has been driven by advancements in production techniques, alloying, heat treatment, quality control, and design optimization. Ductile iron casting continues to offer a balance of strength, toughness, ductility, and cost-effectiveness, making it a reliable choice for a wide range of engineering challenges.