The sand casting is a gear oil pump housing, the structure and size are shown in Figure 1, the material is HT200 (gray cast iron), the overall structure is a housing structure, the structure is compact and complex, and has a hollow inner cavity. The overall dimension of the sand casting is 150 mm × 120 mm × 64 mm, the main wall thickness is 20 mm, the thickest wall thickness is 25 mm, the thinnest wall thickness is 6 mm, and the wall thickness is generally uniform.
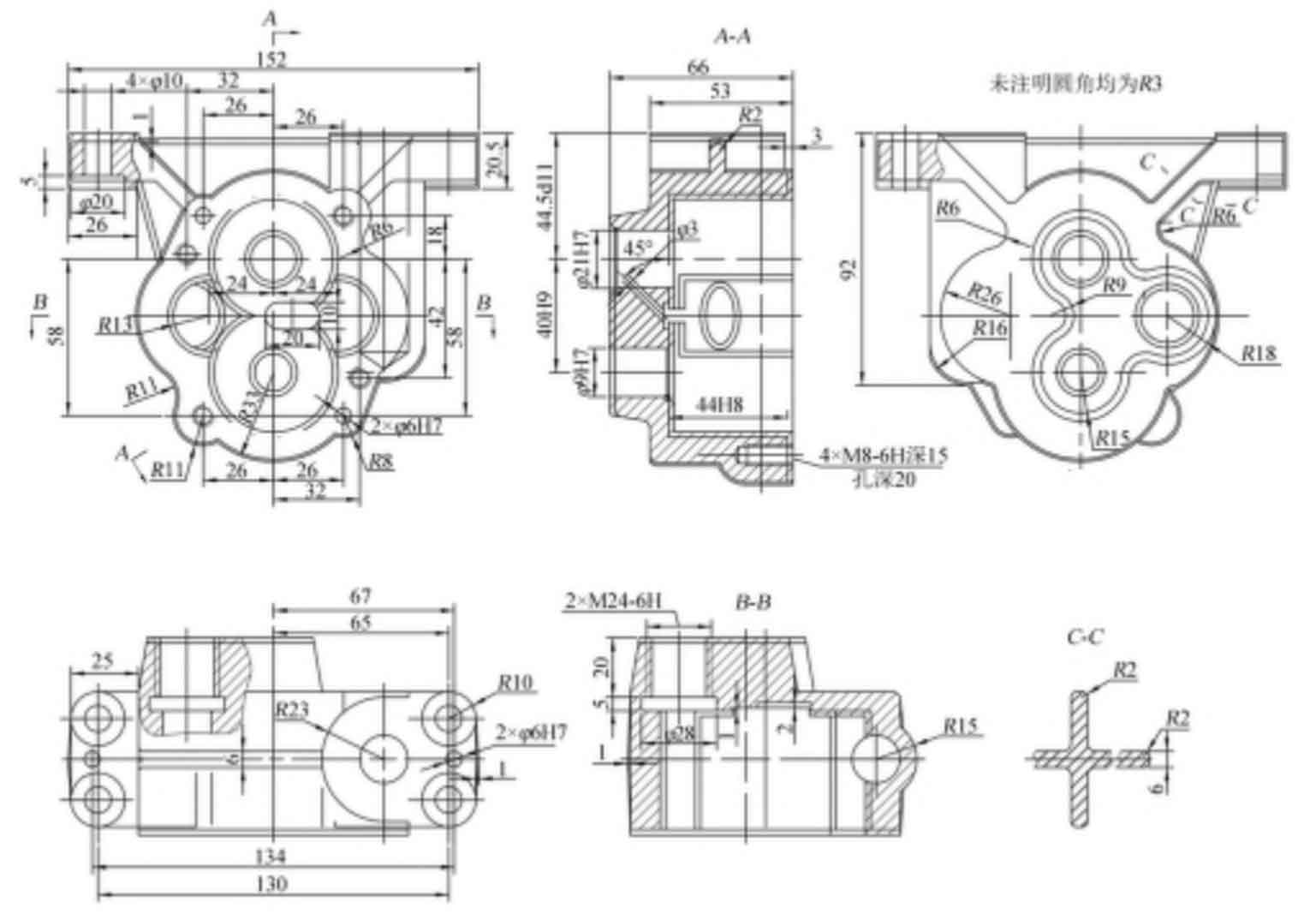
1. Sand casting process
(1) The wall thickness of the sand casting is relatively uniform, the transition and connection between the walls are relatively gentle, and the weak parts of the structure (as shown in the C-C section in Figure 1) are provided with stiffeners to prevent cracks. The minimum wall thickness of the casting is 6 mm, which is 3~4 mm larger than the allowable minimum wall thickness of the sand casting, meeting the requirements.
(2) The gear oil pump is a small casting, which can be wet cast in sand casting, which is easy to operate and has a small workload.
(3) The sand casting with reinforcing rib will hinder the draft, so the parting surface should be selected in the middle of the top view. This parting method is convenient for the draft, and the number of sand cores is not large, which is conducive to the fixation and exhaust of sand cores.
(4) The sand casting is a gear oil pump housing. In order to prevent oil leakage and prolong the service life of the gear, the precision requirement is high.
To sum up, in order to facilitate the sand casting process and save costs on the premise of ensuring the casting quality, it is decided to adopt the wet casting method in sand casting for production.
2. Existing problems
(1) There are many holes on the sand casting. Except for the large hole in the middle, other holes should not be cast after considering the machining allowance, as shown in Section A-A in Figure 1, 4 × The hole of M8-6H depth 15 (hole depth 20) cannot be cast because of its wall thickness of 25 mm, 2 ×φ 6H7 can not be cast. 4 on the base ×φ The 20 mm hole can be cast and formed, but it is not cast and formed due to the consideration of draft and lack of core. After sand casting, it is formed by mechanical processing.
(2) The casting material of the sand casting is gray cast iron, which has good fluidity and large shrinkage, and is prone to defects such as insufficient pouring, cold shut and cold crack during the pouring process. In addition, the plane of the parting surface of the sand casting is large and easy to produce inclusion defects.
(3) The wall thickness of the sand casting is uneven, and the difference between the main wall thickness of the stiffener and the sand casting is large, which is easy to produce cracks.
3. Determination of sand casting process
The sand casting is used for manual molding and mass production. The dimensional tolerance grade of the sand casting is CT11-CT14, and the machining allowance is 2 mm. In the design, the method of increasing thickness is used to obtain the draft angle. According to the Foundry Technology α Draft=1 ° 25 ′, a draft=1 mm, as shown in Figure 2.
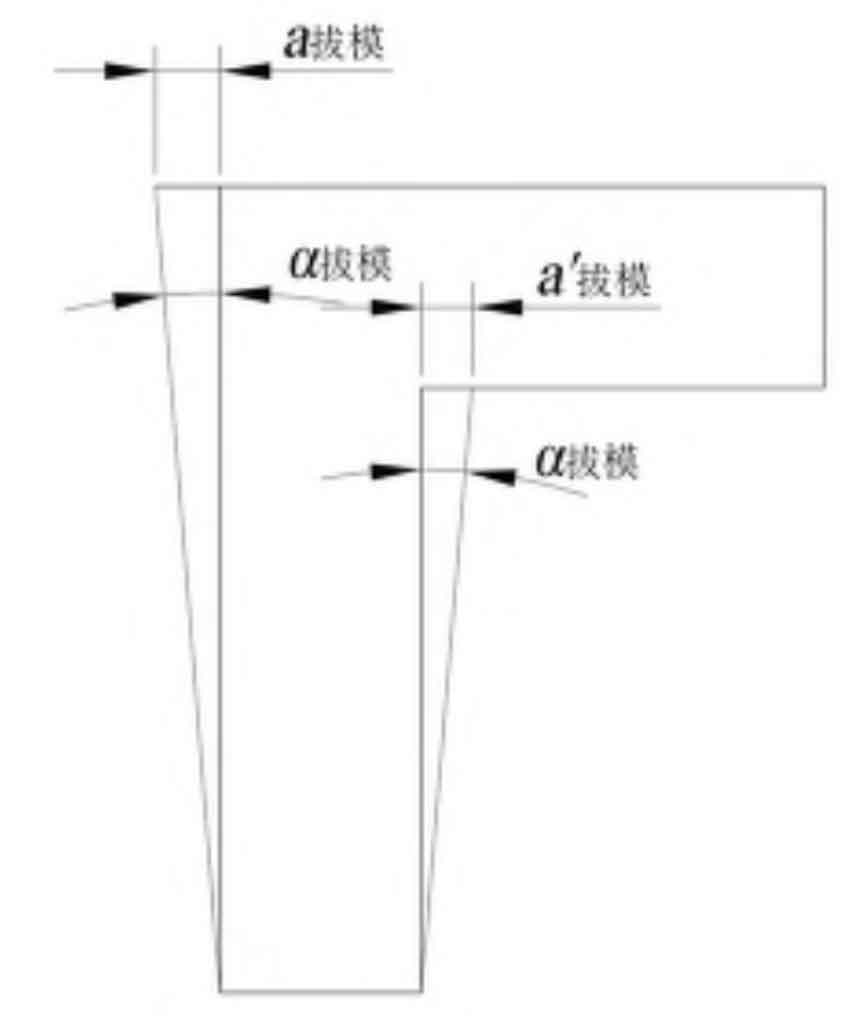
4. Selection of parting surface
Due to the mass production of sand castings, in order to facilitate casting molding and save costs, the wet casting method in sand casting is selected, and the clay sand with lower fire resistance requirements and lower cost is selected.

The selection of the parting surface of the gear oil pump housing should be conducive to the core lowering and box closing. The pouring system adopts the middle injection type to ensure smooth pouring. The selection of the parting surface is shown in Figure 3.