As shown in the figure, the turbine housing parts are complex in structure and moderate in batch. They are molded by sand casting and are made of aluminium alloy with wide crystallization temperature range. This alloy tends to solidify in volume and is very easy to produce dispersive shrinkage in the casting.
The part structure is characterized by uniform wall thickness of 4mm as a whole, in which the center height of the spiral case is a gradient curve, the right end of the spiral case has an elbow flange with a downward length of 70mm, and the center of the spiral case has a straight pipe parallel to the horizontal section of the elbow; the bottom of the spiral case has eight uniformly distributed bumps and the inside of the spiral case has a horn-shaped structure with a wall thickness gradient of 14mm at the thickest point.Turbine housing is a hydraulic part, and the internal quality of casting blank must meet the requirements of air-tight test.
The structure of the part is complicated. Sand casting is considered for casting blank. As shown in the casting process drawing of the turbine housing in Figure 2, the casting needs to be multi-box moulding. When casting, the casting is placed with 8 convex bosses facing downwards. The processing allowance of 3mm is considered for each processing surface. The top flange, bend flange disc, straight pipe, inner flare and 8 convex bosses are all hot joints and shrinkage is considered.
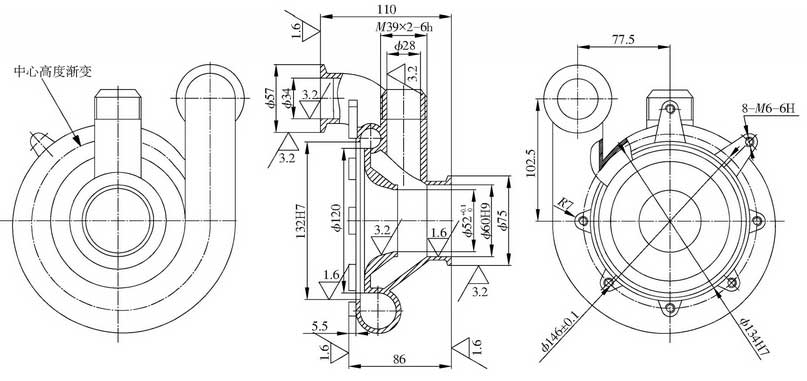
The top flange uses top riser, the bend flange plate uses dark riser, the straight pipe end uses side riser, the inner flare uses metal core, and the eight convex surfaces use outer chiller to realize directional solidification, eliminating casting defects.