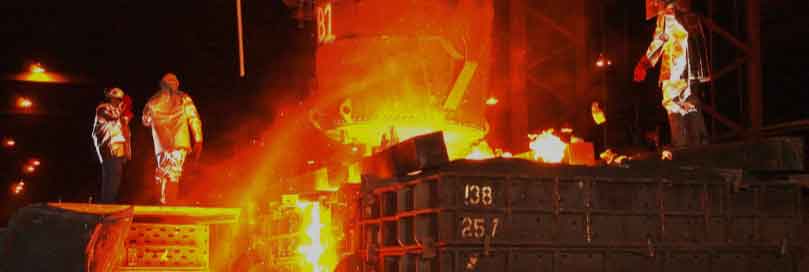
Comparing sand casting with other commonly used casting methods, such as die casting and investment casting, helps highlight the distinct advantages and disadvantages of each process. Here is a comparative analysis of the three casting methods:
- Sand Casting:
- Pros:
- Low tooling cost: Sand molds are relatively inexpensive to produce, making it cost-effective for small to medium-sized production runs.Versatility: Can produce complex geometries and large-sized components with intricate details.Wide material selection: Compatible with various metals and alloys, offering flexibility in material choices.Suitable for prototypes: Allows for rapid prototyping and easy modification of molds.
- Lower dimensional accuracy and surface finish compared to other casting methods.
- Longer lead times: Preparing sand molds and cooling times can lead to longer production cycles.
- Labor-intensive: Requires skilled labor for mold preparation and casting.
- Pros:
- Die Casting:
- Pros:
- High dimensional accuracy and surface finish: Die-cast components typically require minimal post-processing.High production rates: Rapid and repeatable production cycles make it ideal for large-scale manufacturing.Thin-walled parts: Die casting is suitable for producing thin-walled components with precision.Lower material waste: Less material is wasted during the process compared to sand casting.
- High tooling cost: The cost of die casting molds is relatively high, making it more suitable for high-volume production.
- Limited material selection: Die casting is primarily used for non-ferrous metals like aluminum, zinc, and magnesium.
- Complexity constraints: Die casting may have limitations in producing highly complex designs.
- Pros:
- Investment Casting:
- Pros:
- Excellent surface finish and dimensional accuracy: Produces parts with intricate details and tight tolerances.Versatility: Suitable for a wide range of alloys, including ferrous and non-ferrous metals.Complex geometries: Investment casting can handle intricate shapes and thin walls.Low material waste: The process minimizes material waste, making it efficient for expensive metals.
- High tooling cost: The process requires pattern-making and ceramic mold preparation, leading to higher initial costs.
- Longer lead times: The multi-step process may result in longer production cycles.
- Limited production rates: Investment casting is more suitable for smaller production runs.
- Pros:
The choice of casting method depends on the specific requirements of the project, such as the complexity of the part, desired surface finish, material selection, production volume, and budget constraints. Sand casting offers versatility and lower initial costs, making it a suitable choice for prototyping and small to medium-scale production. Die casting excels in high-volume production with excellent dimensional accuracy and surface finish. Investment casting is preferred for complex geometries and applications that demand high precision and a wide range of materials. Ultimately, manufacturers should consider these factors to select the most suitable casting method for their specific needs.